固定夾的沖壓成形工藝與模具設計說明書
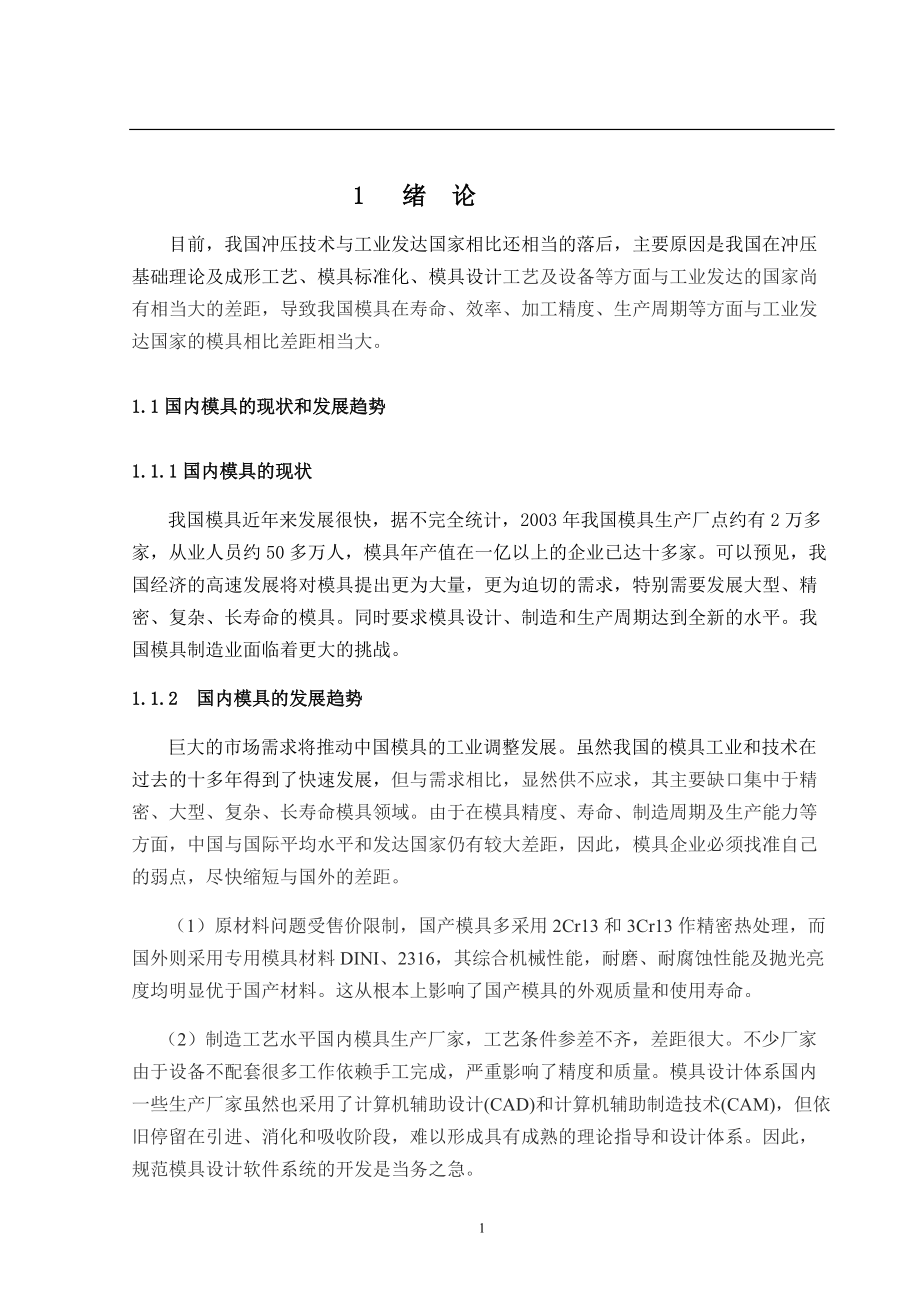


《固定夾的沖壓成形工藝與模具設計說明書》由會員分享,可在線閱讀,更多相關《固定夾的沖壓成形工藝與模具設計說明書(28頁珍藏版)》請在裝配圖網上搜索。
1、 1 緒 論 目前,我國沖壓技術與工業(yè)發(fā)達國家相比還相當的落后,主要原因是我國在沖壓基礎理論及成形工藝、模具標準化、模具設計工藝及設備等方面與工業(yè)發(fā)達的國家尚有相當大的差距,導致我國模具在壽命、效率、加工精度、生產周期等方面與工業(yè)發(fā)達國家的模具相比差距相當大。 1.1國內模具的現狀和發(fā)展趨勢 1.1.1國內模具的現狀 我國模具近年來發(fā)展很快,據不完全統(tǒng)計,2003年我國模具生產廠點約有2萬多家,從業(yè)人員約50多萬人,模具年產值在一億以上的企業(yè)已達十多家。可以預見,我國經濟的高速發(fā)展將對模具提出更為大量,更為迫切的需求,特別需要發(fā)展大型、精密、復雜、長壽命的模具。同時要求
2、模具設計、制造和生產周期達到全新的水平。我國模具制造業(yè)面臨著更大的挑戰(zhàn)。 1.1.2 國內模具的發(fā)展趨勢 巨大的市場需求將推動中國模具的工業(yè)調整發(fā)展。雖然我國的模具工業(yè)和技術在過去的十多年得到了快速發(fā)展,但與需求相比,顯然供不應求,其主要缺口集中于精密、大型、復雜、長壽命模具領域。由于在模具精度、壽命、制造周期及生產能力等方面,中國與國際平均水平和發(fā)達國家仍有較大差距,因此,模具企業(yè)必須找準自己的弱點,盡快縮短與國外的差距。 (1)原材料問題受售價限制,國產模具多采用2Cr13和3Cr13作精密熱處理,而國外則采用專用模具材料DINI、2316,其綜合機械性能,耐磨、耐腐蝕性能及拋光亮度
3、均明顯優(yōu)于國產材料。這從根本上影響了國產模具的外觀質量和使用壽命。 (2)制造工藝水平國內模具生產廠家,工藝條件參差不齊,差距很大。不少廠家由于設備不配套很多工作依賴手工完成,嚴重影響了精度和質量。模具設計體系國內一些生產廠家雖然也采用了計算機輔助設計(CAD)和計算機輔助制造技術(CAM),但依舊停留在引進、消化和吸收階段,難以形成具有成熟的理論指導和設計體系。因此,規(guī)范模具設計軟件系統(tǒng)的開發(fā)是當務之急。 (3)調試水平模具就其本質而言屬于工裝,生產出合格制品才是最終目的。因此,模具的質量、性能依賴試模結果檢驗。國內模具廠因交貨期短,試模設備局限,往往把質量檢驗工作放在用戶處試模,易給
4、用戶造成大量的損失和浪費。而且由于修模受時間,場地限制,往往難以調試出最佳狀態(tài)。而國外一些發(fā)展較好的企業(yè)都擁有自己的試模場所和設備,可以模擬用戶的工作條件試模,所以能在最短的時限達到很好的效果。 (4)配套體系我國模具生產企業(yè)習慣埋頭搞生產科研,而忽視了與其他設備供應商、原料供應商合作。無形中使用戶走了許多彎路。我們的模具廠必須和其他廠家及各大科研院所共同合作,為用戶創(chuàng)造最佳的制品,創(chuàng)造更大的利潤。 (5)專業(yè)化、標準化、商品化的程度低、協作差由于長期以來受"大而全""小而全"影響,許多模具企業(yè)觀念落后,模具企業(yè)專業(yè)化生產水平低,專業(yè)化分工不細,商品化程度也低。目前國內每年生產的模具,商品
5、模具只占45%左右,其馀為自產自用。模具企業(yè)之間協作不好,難以完成較大規(guī)模的模具成套任務,與國際水平相比要落后許多。模具標準化水平低,標準件使用覆蓋率低也對模具質量、成本有較大影響,周期影響較甚。 (6)價格因素:目前一些廠商只關心價格,而忽略了模具的技術質量,對用戶而言合理的質量價格比是最優(yōu)選擇,所以進口模具價格比國產模具高8~10倍,仍有其市場空間。國內一些模具廠,迫于競爭需要,盲目壓價,甚至以次充好,粗制濫造,是一種不負責任的短期行為,將為國產模具的發(fā)展帶來重創(chuàng)。當然,在確保品質的前提下,加強管理,擴大規(guī)模,降低成本無疑是努力的方向。 1.2 國外模具的現狀和發(fā)展趨勢 模具是工業(yè)
6、生產關鍵的工藝裝備,在電子、建材、汽車、電機、電器、儀器儀表、家電和通訊器材等產品中,60%-80%的零部件都要依靠模具成型,模具工業(yè)已成工業(yè)發(fā)展的基礎,其生產技術水平的高低,已成為衡量一個國家制造業(yè)水平高低的重要標志,近幾年,全球模具市場呈現供不應求的局面。美國、日本、法國、瑞士等國家年出口模具量約占本國模具年總產值的三分之一,國外模具總量中,大型、精密、復雜、長壽命模具的比例占到50%以上;國外模具企業(yè)的組織形式是"大而專"、"大而精"。2004年中國模協在德國訪問時,從德國工、模具行業(yè)組織--德國機械制造商聯合會(VDMA)工模具協會了解到,德國有模具企業(yè)約5000家。2003年德國模具
7、產值達48億歐元。其中(VDMA)會員模具企業(yè)有90家,這90家骨干模具企業(yè)的產值就占德國模具產值的90%,可見其規(guī)模效益。其發(fā)展趨勢是高效、精密、數控自動化。 1.3 沖裁復合模及彎曲模具設計與制造方面 1.3.1沖裁復合模及彎曲模具設計的設計思路 沖孔和落料是沖壓基本工序之一。它是利用沖裁模在壓力機作用下,將板料沿一定輪廓線產生分離的一種加工方法。它不僅可以直接沖出成品零件,也可以為彎曲、拉深、成形等其他工序備料,還能對已成形的工件進行再加工。 彎曲屬于成形工序,也是沖壓加工的基本工序之一。它是利用金屬的塑性變形,將板料、棒料、型材或管材等按設計要求彎成一定曲率和一定角度的零件的
8、一種沖壓工序。與沖裁模相比彎曲模準確工藝計算較難,模具動作復雜、結構設計規(guī)律性不強。 1.3.2沖裁復合模及彎曲模具設計的進度 1.了解目前國內外沖壓模具的發(fā)展現狀,所用時間5天; 2.確定加工方案,所用時間15天; 3.模具的設計,所用時間30天; 4.模具的調試.所用時間10天。 2 固定夾沖壓工藝的分析 2.1制件的工藝性分析 原始資料:如圖所示 圖2-1 制件圖 材 料: 08鋼 厚 度: 1.2mm 該零件是一個簡單的固定夾。零件工作時受力不大,對強度、剛度和精度要求不高,
9、零件形狀簡單對稱,大批量生產,由沖裁和彎曲加工即可成形。 2.2 制件的工藝計算和工藝方案的確定 制件的工藝計算是工藝設計中的一個環(huán)節(jié),本制件的工藝計算屬于最簡單的彎曲工藝的計算。 2.2.1 工藝方案的分析和確定 根據制件的工藝分析可知,制件進行沖壓加工的基本工序為沖孔、落料和彎曲。其中沖孔和落料屬于簡單的分離工序,半圓形彎曲屬于簡單的成形工序,可一次成形。 該制件上直徑為3.5㎜孔的邊與彎曲中心的距離為5.25㎜,大于1.0t(1.2㎜),彎曲時不會引起孔變形,因此四個孔可以在壓彎前沖出。 根據零件特點和工藝要求,可能有的沖壓工藝方案有: 方案一:沖直徑為3.5㎜的孔和落
10、料工序復合,然后進行半圓形的彎曲。 方案二:全部工序組合采用帶料連續(xù)沖裁。 沖壓工藝方案的分析如下: 方案一:模具結構簡單,模具壽命長,制造周期短,投產快,工件的回彈容易控制,尺寸和形狀準確,表面質量高,操作比較簡單方便。但是工序分散,模具數量多,生產效率低。 方案二:工序集中,用一副模具完成全部工序,由于它實質上是把方案一的各工序布置到級進模的個工位上,所以它具有方案一的各項優(yōu)點。但是模具結構復雜,安裝、調試、維修困難,制造周期長。 綜上所述,考慮到該零件的批量較大,為保證各項技術要求選用方案一。其工序如下:落料和沖直徑為3.5㎜的孔,彎曲半徑為2㎜的半圓。 落料和沖孔的復合工序
11、可用復合沖裁模來完成,由于正裝復合模的沖孔廢料需要從上模引出,該制件孔較多,沖孔廢料易落入下模部分,造成清理麻煩,而且制件上沖裁孔邊距離較大,因此可選用倒裝的復合模來完成沖裁。而彎曲工序可依靠簡單的單工序彎曲模彎曲成形。由于制件的相對彎曲半徑較小,卸載后彎曲圓角半徑的變化很小,則不需采用壓邊裝置。 2.2.2 毛坯尺寸的計算 因為圓角半徑r2和r3大于0.5t,則可根據柸料總長度等于彎曲件直線部分長度和彎曲圓角部分應變中性層長度之和,即 圖2-2 毛坯展開長度L0: L0=2(l1+l2)+l3 (1-1) 由毛坯圖得:
12、L1=9㎜, L2=∏(r2+xt)/180 =3.14180(2+0.4571.2) =8㎜,(根據r/t可得應變中性層系數x的值為0.457) L3=∏(r3+xt)/180 =3.1490(1+0.4571.2) =0.8㎜, 因此 L0=2(9+0.8)+8=27.6㎜ 2.2.3 排樣和裁板方案的選擇 柸料形狀為矩形,查表可得,取搭邊值a=1.2㎜,a1=1.5㎜, B=(D+2a)0-△,查表得△=0.15 側條料寬度 B=(27.6+21.2)0-0.15=300-0.15㎜ 側送
13、料布距 A=25+1.5=26.5㎜ 板料規(guī)格選用 1.2㎜400㎜1800㎜ 采用縱排法: 每板條料數 n1=400/30=13(條),余10㎜ 每條制件數 n2=(1000-1.2)/26.5=37(條),余19.5㎜ 101000余料利用件數 n3=1000/30=33(條),余10㎜ 每板制件數 n=n1n2+n3=1337+33=514(件) 材料利用率 =514(27.625-43.143.52)/400100﹪=68.9﹪ 采用橫排法: 每板條料數 n1=1000/30=33(條),余10㎜= 每條制件數 n
14、2=(400-1.2)/26.5=15(條),余2.5㎜ 201000余料利用件數 n3=400/30=13(條),余10㎜ 每板制件數 n=n1n2+n3=3315+13=508(件) 材料利用率 η=508(27.625-43.143.52)/4001000﹪=68.1﹪ 由此可見,縱排利用率高,但橫排時彎曲線與纖維方向垂直,彎曲性能好。08鋼塑性好,為提高效率,降低成本,選用縱向單排法。柸料尺寸為1.2㎜30㎜1000㎜。 排樣圖如圖2-3所示。圖2-3 2.3 沖壓力的計算及沖壓設備的選用 2.3.1 落料與沖孔復合工序沖
15、壓力的計算 由于沖裁工序選用倒裝復合模,因此沖壓力的計算只需計算推件力和卸料力。 查表可得b=360MPa,K卸=0.05,K推=0.05,凹模刃口高度取8㎜,則可推出制件數n=8/1.2=6 沖裁力:F=Ltb=(225+227.6+43.5)1.2360 =51494.4(N) 卸料力:F卸=K卸F=0.0551494.4=2574.72(N) 推件力:F推=nK推F=60.0551494.4=15448.32(N) 則 沖壓力F總=(F+F卸+F推)=51494.4+2574.72+15448.32=69517.44(N) 2.3.2 彎曲工序沖壓力的計算 由于半圓形
16、彎曲開始為U形彎曲,因此按U形件彎曲計算。 自由彎曲力: F自=0.7Kbt =0.71.3251.2360/(2+1.2)=3685.5N 因為制件相對彎曲半徑較小,r/t﹤0.5,由于變形程度大,卸載后彎曲圓角半徑的變化很小,可以不予考慮,而僅考慮彎曲中心角的回彈量,因此需要校正彎曲。 校正彎曲力:F較=Ap=(625)50=7500(N) 校正面積 A=625=150(㎜2),單位校正力 P=50MPa 為安全可靠,將自由彎曲力F自和校正彎曲力F較合在一起。 即沖壓力為 F總=F自+F較=3685.5+7500=11185.5(N) 2.3.3
17、 壓力中心的確定 由制件圖分析,制件前后左右結構均對稱,因此沖孔和落料復合模的壓力中心P在制件的中心。 2.3.4 落料與沖孔復合工序沖壓設備的選擇 為使壓力機能安全工作,取 P壓機≧(1.6~1.8)F總 則 P壓機=1.769.517(KN)=118.18(KN) 因此可選用160KN的開式壓力機,其型號為J23-16F。其主要技術參數如下: 公稱壓力:160KN 最大封閉高度:205㎜ 滑塊行程:70㎜ 封閉高度調節(jié)量:45㎜ 工作臺尺寸:300㎜450㎜ 墊板孔尺寸:210㎜ 模柄孔尺寸:φ40㎜60㎜
18、 墊板厚度:40㎜ 2.3.5 彎曲工序沖壓設備的選擇 為使壓力機能安全工作,取 P壓機≧(1.6~1.8)F總 則 P壓機=1.711.19(KN)=19.023(KN) 因此可選用31.5KN的開式壓力機,其型號為J23-3.15。其主要技術參數如下: 公稱壓力:31.5KN 最大封閉高度:120㎜ 滑塊行程:25㎜ 封閉高度調節(jié)量:25㎜ 工作臺尺寸:160㎜250㎜ 墊板孔尺寸:110㎜ 模柄孔尺寸:φ25㎜40㎜ 墊板厚度:30㎜ 3 模具的結構設計 3.1 模具工作部分
19、的計算 3.1.1 落料沖孔復合模的尺寸計算 因為零件圖中的尺寸公差為未注公差,在處理這類零件公差的等級時均按IT14級要求。由于制件結構簡單,精度要求不高,所以采用凸、凹模分開加工的方法制作凸、凹模。其中凸、凹模尺寸計算如下: 查表可得,凸、凹模制造公差: £凸=0.02㎜,£凹=0.02㎜ 校核:查表可知Zmax=0.126,Zmin =0.180,Zmax-Zmin=0.066㎜,而£凸+£凹=0.04,滿足Zmax-Zmin≧£凸+£凹的條件 查表可得,IT17級時磨損系數 x=0.5。 按公式可得: d凸=(dmin+x△)0-£凸 =(3.5+0.50.3)0-0
20、.02㎜=3.650-0.02㎜ d凹=(d凸+Zmin)0+£凹 =(3.65+0.126)0+0.02㎜=3.7760+0.02㎜ 所以沖孔凸凹模的尺寸為:d凸=3.650-0.02㎜,d凹=3.7760+0.02㎜,L=170.12㎜。 由于制件結構簡單,精度要求不高,所以采用凸、凹模分開加工的方法制作凸、凹模。因為零件圖中的尺寸公差為未注公差,在處理這類零件公差的等級時均按IT14級要求,查相關文獻可得外形尺寸的極限偏差為:250-0.52㎜,27.60-0.52㎜。凸、凹模尺寸計算如下: 查表可得,凸、凹模制造公差: £凸=0.02㎜,£凹=0.025㎜ 校核:查表可知
21、Zmax=0.126,Zmin =0.180,Zmax-Zmin=0.066㎜,而£凸+£凹=0.045,滿足Zmax-Zmin≧£凸+£凹的條件 按公式 D凹=(Dmax-x△)0+£凹,D凸=(D凹-Zmin)0-£凸 零件尺寸為25㎜處凸、凹模的尺寸: D凹1=(25-0.50.52)0+0.025㎜=24.740+0.025㎜ D凸1=(24.74-0.126)0-0.02㎜=24.5140-0.02㎜ 零件尺寸為27.6㎜處凸、凹模的尺寸: D凹2=(27.6-0.50.52)0+0.025㎜=27.340+0.025㎜ D凸2=(27.34-
22、0.126)0-0.02㎜=27.1140-0.02㎜ 所以落料凸模和凹模的尺寸為: D凹1=24.740+0.025㎜, D凸1=24.5140-0.02㎜ D凹2=27.340+0.025㎜, D凸2=27.1140-0.02㎜ 3.1.2 彎曲模具的尺寸計算 凸模圓角半徑的計算: 因為彎曲半徑為2㎜,尺寸較小,但不小于工件材料所容許的最小彎曲半徑 rmin=0.4t㎜=0.48㎜,則可取凸模圓角半徑r凸等于或略小于彎曲件內側的圓角半徑。因此可取凸模半徑r凸=2㎜。 凹模圓角半徑的計算: 凹模圓角半徑r凹的大小對彎曲力以及彎曲件的質量均有影響。r凹過小會使彎矩的彎曲力臂減
23、小,毛坯沿凹模圓角滑入時的阻力增大,彎曲力增加,并易使工件表面擦傷甚至出現裂紋。凹模兩邊的圓角半徑應一致,否則在彎曲時會發(fā)生偏移。實際生產中r凹通常根據材料的厚度t選?。? 當t﹤2㎜時,r凹=(3~6)t; 當t=2~4㎜時,r凹=(2~3)t; 當t﹥4㎜時,r凹=2t; 該制件厚度t=1.2㎜,故凹模圓角半徑r凹=51.2=6㎜ 3.2 模具的總體設計 3.2.1 落料與沖孔復合工序模具的總體設計 根據上述的各項分析,本零件的沖壓包括沖孔和落料兩個工序,且孔邊距較大,采用倒裝復合模進行沖裁時,可直接利用壓力機上的打桿裝置進行推件,卸料可靠,便于操作。工件留在落料
24、凹??锥粗?,應在凹??自O置推件塊;卡于凸凹模上的廢料可由卸料版推出;而沖孔廢料則可以在下模座中開設通槽,使廢料從孔洞中落下。由于在該模具中壓料是由落料凸模與卸料版一起配合工作來實現。所以卸料版還應具有壓料作用,應選用彈性卸料版來卸下條料廢料。 因為是大批量生產,則可采用手動送料裝置,從右往左送料。 因為該制件采用的是倒裝復合模,所以直接用擋料銷和導料銷即可。 為確保零件的質量及穩(wěn)定性,選用導柱、導套導向。由于該零件導向尺寸較小,且精度要求不是太高,所以易采用后側導柱模架。 3.2.2 彎曲半圓形工序模具的總體設計 根據上述的各項分析,該模具采用彎曲單工序模,由于該制件為半圓形彎曲
25、,且彎曲時回彈較小,制件結構對稱,因此不需要采用壓料裝置。上模主要由上模座、凸模等零件組成,下模主要由下模座、凹模、凹模固定板和定位板、墊板、螺釘等零件組成。由于該零件彎曲是回彈較小,因此不需要采用壓邊裝置。 因為該制件為半圓形彎曲,所以采用手工前后脫模,不需要采用彈頂裝置。 3.3 模具主要零部件的設計 3.3.1 落料凹模的結構設計 沖裁時凹模承受沖壓力和側向擠壓力的作用,因此凹模的外形尺寸應保證有足夠的強度和剛度。在落料凹模內部,由于需要設置推件塊。所以凹模刃口應采用直筒形刃口,經查相關資料可取得刃口高度h=8㎜。該凹模的結構簡單,宜采用整體式。 查表可得厚度系數k=0
26、.5,則凹模厚度H=ks=0.527.6=13.8(㎜),由于凹模壁厚要大于等于15㎜,因此凹模厚度為15㎜。 凹模壁厚 C=1.5H=1.513.8=20.7(㎜) 凹模外形尺寸的確定: 凹模外形長度: L=27.6+220.7=69(㎜) 凹模外形寬度: B=25+220.7=66.4(㎜) 依據設計尺寸,按沖模標準確定凹模外形尺寸為:75㎜75㎜25㎜。凹模的上下表面應保持平行,凹模孔軸線應與凹模頂面保持垂直型 孔表面粗糙度要求Ra=0.8~0.4μm。凹模結構如下圖3-1所示: 圖3-1 3.3.2 沖直徑為3.5㎜孔凸模的結構設計 為了增加凸模的強度
27、與剛度,凸模非工作部分應制成逐漸增大的多級形式,這種凸模在裝配修模時也很方便。 凸模固定板厚度取h=0.7H=0.713.8(㎜)=8.8(㎜)。 凸模長度根據結構上的需要來確定: L=h凸模固定板+h落料凹模=8.5+25=33.8(㎜),取35㎜. 由于此凸模直徑不大,長度較短且料厚較薄,則剛度和強度足夠,所以無需對其進行強度校核。沖裁時凸模進入凹模刃口1㎜。 凸模結構如圖3-2所示: 圖3-2 3.3.3 沖裁模具中凸凹模的結構設計 本模具為復合沖裁模,除了沖孔凸模和落料凹模外還有一個凸凹模。根據整體模具的結構設計需要,確定凸凹模安排在模架的位置時,要依據計算的壓力中心的數據
28、,使壓力中心與模柄中心重合。凸凹模的結構簡圖如上圖3-3所示。圖3-3 校核凸凹模的強度:查表可得凸凹模的最小壁厚為3.2㎜,而實際制件中的最小壁厚為3.4㎜,大于所要求的最小壁厚,因此復合強度要求。凸凹模的刃口尺寸按落料凹模的尺寸配制,并保證雙面間隙為0.246㎜~0.36㎜。凸凹模上孔中心與邊緣距離尺寸5㎜的公差,應比零件所標注的精度高3~4級,即定為(50.048)㎜。 3.3.4 沖裁模具中彈性元件的結構設計 為了得到較平整的工件,此模具采用彈頂式卸料結構,使條料在落料和沖孔中始終處在一個穩(wěn)定的壓力之下,從而改善了毛坯的變形穩(wěn)定性,避免材料在切向應力作用下起皺的可能。彈性卸料
29、裝置由卸料板、彈性元件、卸料螺釘等組成。在彈性元件的選用時,考慮到橡膠可以承受的負荷較彈簧大,且安裝調試方便,因此落料卸料采用橡膠作為彈性元件。 橡膠的自由高度 H自由=(3.5~4)S工作 式中 H自由—橡膠的自由高度,㎜; S工作—工作行程與模具修模量或調整量(4~6㎜)之和,㎜。 S工作=10+1+5=16(㎜) H自由=(3.5~4)16=(57.6~64)㎜ 取H自由=60㎜。 橡
30、膠的裝配高度 H裝配=(0.85~0.9)H自由=(0.85~0.9)60=(51~54)㎜取H裝配=52㎜。橡膠的截面面積,在裝配時按模具空間大小確定。 3.3.5 沖裁模具中定位零件的結構設計 沖裁模定位零件的作用是使條料或半成品毛坯在模具上能迅速放正,便于實施沖裁。毛坯在模具中的定位有兩方面的內容:一是在與條料送料方向垂直的方向上的限位,保證條料沿著正確的方向送進,稱為送進導向或稱導料;二是在送料方向的限位,控制條料一次送進的距離稱為送料定距或稱擋料。
31、 送進導向零件的設計:由于采用的是彈性卸料裝置,因此不需要選用導料板或者承料板等其它結構,只要選用導料銷作為送進導向零件即可。導料銷一般有兩個,設在條料的同側,條料沿著兩個導料銷確定的直線送進。因為該沖裁模具從右向左,則導料銷可裝在模具后側,并固定在彈性卸料板上。導料銷的尺寸可按標準結構選擇,直徑可為6㎜。 送料定距零件的設計:由于該模具采用的是倒裝復合模,因此可選用圓頭形式的固定擋料銷,并安裝在彈性卸料板上。 擋料銷的形狀如右圖3-4所示:圖3-4 3.3.6 沖裁模模架的設計 模架各零件標記如下: 上模座:
32、150㎜130㎜25㎜ 下模座:150㎜130㎜30㎜ 導 柱:B25h5100㎜17.5㎜ 導 套:B25H645㎜25㎜ 模 柄:φ30㎜60㎜ 墊板厚度:75㎜70㎜9㎜ 卸料板厚度:75㎜70㎜12㎜ 凸模固定板厚度:75㎜70㎜8.8㎜ 凸凹模固定板厚度:75㎜70㎜10㎜ 模具閉合高度: H閉=h上模座+h墊板+h凸模固定板+h落料凹模+t+h卸料版+h橡膠裝配+h凸凹模固定板+h下模座 =25+9+8
33、.8+25+1.2+12+52+10+40=183(㎜) 由于所選沖床的最大閉合高度為205㎜,安裝模具時,需在工作臺面上配備墊塊,墊塊的實際尺寸可配制。沖裁所需的總壓力為118.18KN,而沖床的總稱壓力為160KN,因此滿足使用要求。而且模具的最大安裝尺寸為150㎜130㎜,沖床工作臺臺面尺寸為300㎜450㎜,也可以滿足模具的正確安裝。因此所選沖床滿足使用要求。 3.3.7 半圓形彎曲凸、凹模的設計 由于該制件為半圓形彎曲,制件結構對稱,且彎曲相對半徑較小,因此彎曲凸??蛇x用半徑為2㎜的圓柱形凸模。 彎曲凹模深度的選取要適當,若太小,則彎曲件兩端自由部分太長,工件回彈大,不
34、平直;若深度過大,則凹模增高,多耗模具材料,并需要較大的壓力機行程。因為直邊高度不大,且兩邊要求平直,因此凹模深度應大于工件的深度。查相關資料可得知,彎曲時凹模的底部最小厚度為4㎜,因此選擇凹模深度為10㎜。 3.3.8 彎曲模具中導向零件的結構設計 為提高模具壽命和工件質量,方便安裝調整,該模具采用中間導柱的導向方式。 3.3.9半圓形彎曲模架的設計 由于彎曲模不是標準模架,因此需要自主設計。 模架各零件標記如下: 下模座:100㎜60㎜20㎜ 模 柄:φ25㎜40㎜ 凸 模:40㎜4㎜29㎜ 凹模
35、板厚度:40㎜40㎜20㎜ 頂板厚度:80㎜40㎜10㎜ 中間的安全距離:20㎜ 彎曲模閉合高度是指沖床運行到下止點時,模具工作狀態(tài)的高度。因此模具閉合高度為:H=H模柄+H凹模板+H安全距離+H頂板厚度+H頂桿 =25+20+20+10+30.2=105.2(㎜) 經計算校核,前面所選的型號為J23-3.15的彎曲模壓力機的最大閉合高度可以滿足使用要求。由于所選沖床的最大閉合高度為120㎜,安裝模具時,需在工作臺面上配備墊塊,墊塊的實際尺寸可配制。沖裁所需的總壓力為19.023KN,而沖床
36、的總稱壓力為31.5KN,因此滿足使用要求。而且模具的最大安裝尺寸為100㎜60㎜,沖床工作臺臺面尺寸為300㎜450㎜,也可以滿足模具的正確安裝。由于此壓力機的滑塊行程為45㎜,大于工件高度的兩倍,因此滿足支承板彎曲時的沖壓行程。 4 模具的裝配與調試 4.1 模具的裝配 模具裝配沒有嚴格的工藝規(guī)程。裝配工藝過程由鉗工掌握。 模具裝配是模具制造中關鍵的一個環(huán)節(jié),也是體現模具鉗工技術能力的標志。模具裝配就是將加工達到要求的模具零件組合,連接起來,成為一副與規(guī)定的技術要求相符合的合格模具。模具的質量和使用壽命不僅與模具零件的加工質量有關,更與模具的裝配質量有關。比如一副沖裁模具凸模和
37、凹模的尺寸在加工時已經得到保證,但是如果裝配調整的不好,凸模、凹模配合間隙不均勻,沖制的工件質量就差,甚至會出廢品,模具的壽命也會大大降低。 模具的裝配工藝過程視模具類型結構的不同會有所差別,但是模具制造屬單件、不批量、生產類型、裝配精度和技術要求比較嚴格和特殊,為了保證裝配精度和技術要求,主要采用修配和調節(jié)的裝配方法。 模具的裝配包括組件裝配、總裝和調試等階段,整個裝配過程中的調試工作及其重要,在組裝尤其視在總裝中常常反復裝拆、調整、修配,直至試模合格才算裝配完成。 4.1.1 模具的安裝要求 1)組成模具的各零件的材料、尺寸公差、形位公差、表面粗糙度和熱處理等均應符合相應圖樣的要
38、求。 2)模架的三項技術指標:上模座上平面對下模座下平面的平行度,導柱軸心線對下模座下平面的垂直度和導套孔軸心線對上模座上平面的垂直度均應達到規(guī)定的精度要求。 3)模架的上模沿導柱上、下移動應平穩(wěn),無阻滯現象。 4)裝配好的沖裁模,其封閉高度應符合圖樣規(guī)定的要求。 5)模柄的軸心線對上模座上平面的垂直度公差在全長范圍內不大于 0.05㎜。 6)凸模和凹模之間的配合間隙應符合圖樣要求,周圍的間隙應均勻一致。 7)定位裝置要保證定位準確可靠。 8)卸料及頂件裝置活動靈活、正確,出料孔暢通無阻,保證制件及廢料不卡在沖模中。 9)模具應在生產的條件下進行試驗,沖出的零件應符合圖樣要求。
39、 4.1.2 沖裁模的安裝 由于本模具采用的是落料沖孔復合模,因此裝配時的順序應先裝凸凹模,然后再裝凹模和凸模,最后總裝。裝配過程如下: 1) 以下模座為下模部分的基準件,壓裝導柱。 2)以下模的中心線為基準,找正凸凹模的位置后,用平行夾將凸凹模與下模座夾緊,按凸凹模型孔在模座上劃出漏料孔線,取下凸凹模,加工下模座上的漏料孔。 3)按下模座的中心線為基準,用平行夾頭將凸凹模固定板與下模座夾緊,以凸凹模固定板上的螺釘過孔、銷孔為引導,在下模座上鉆螺紋孔底孔,攻螺紋,鉆、鉸銷孔。然后將下模座與凸凹模固定板分離。 4)以凸凹模固定板與凸凹模組件的基準件,
40、鉚接后磨平凸凹模尾部和端部。 5)將卸料版套裝在正裝入凸凹模固定板的凸凹模上,兩者之間墊入適當高度的等高墊鐵,用平行夾頭夾緊,以卸料版上的螺釘定位,在凸凹模固定板上鉆出錐窩,然后拆去墊板,以錐窩定位,鉆凸凹模固定板的螺釘過孔。 6)將卸料版、橡膠、凸凹模與凸凹模固定板組件都安裝在下模座上,以圓柱銷定位,用螺釘連接。 7)以上模座為上模部件的基準件,壓入導套。 8)在上模座上壓裝模柄后磨平,騎縫配鉆,鉸防轉銷孔,裝上防轉銷釘。 9)以凸模固定板與凸模組件的基準件,壓裝上凸模,鉚接后磨平凸模尾部和端部。 10)將四個凸模通過推件塊插入凸凹模相應的型孔中,在凸凹模與推件塊之間墊等高墊鐵,
41、使凸模插入凸凹模型孔的深度保持在1㎜左右;放上墊板和落料凹模,裝上上模座,用平行夾將凸凹模固定板、墊板與上模座夾持在一起(不完全夾緊);將模具整個翻轉過來,用透光法通過下模座的漏料孔觀察,調整凸、凹模配合間隙的均勻性,調整好后擰緊平夾;將模具再翻轉過來,輕擊上模座使沖孔凸模從凸凹模型孔中退出,墊紙片試沖,在調整,再試沖,直至間隙均勻為止。 11)擰緊平夾,取下上模部件;配鉆銷釘孔,配鉆、鉸銷釘孔。 12)裝上銷釘(定位)和螺釘(連接)。 13)將裝好的模具裝在沖床上試沖,檢查送料是否通暢,凸、凹模配合間隙是否均勻,步距是否靈活,沖件是否符合圖紙要求。 4.1.3 彎曲模的安
42、裝 由彎曲模的裝配圖樣分析,該模具應先裝配上模,以上模部分的凹模板為基準,調整裝配下模部分的凸模及其他零件。裝配過程如下: 1)以上模座為上模部分的基準件,在上模座上壓裝模柄后磨平,騎縫配鉆,鉸防轉銷孔,裝上防轉銷釘。 2)以上模座為基準件,按上模座的中心線為基準,找正凹模板的位置后,用平行架將凹模與上模座夾緊,以凹模上的銷釘孔為引導,在上模座上攻螺紋、鉆、鉸銷孔。 3)將凹模板與上模座用銷釘定位。 4)用螺釘將凸模固定板與下模座和凸模連接在一起,插入頂桿,然后把頂板套裝在凸模上。 5)將凸模插入凹模型孔,并在其之間墊上等高墊鐵,用透光法通過凸、凹模相鄰兩側的間隙觀察,調整凸
43、、凹模之間配合間隙的均勻性,調整好后,墊紙片試彎,在調整,再試彎,直至間隙均勻為止。 6)裝上銷釘(定位)和螺釘(連接)。 7)將裝好的模具裝在沖床上試彎,檢查凸、凹模配合間隙是否均勻,彎曲件是否符合圖紙要求。 4.2 模具的調試 模具按圖紙技術要求加工與裝配后,必須在符合實際生產條件的環(huán)境中進行試沖,通過試沖可以發(fā)現模具設計與制造的缺陷,找出產生原因,對模具進行適當的調整和修理,直到模具正常工作制造處合格的制件為止。 4.2.1 沖裁模的調試要點 1. 模具閉合高度的調試 模具應與沖壓設備配合好,保證模具應有的閉合高度和開啟高度。 2.凸、凹模配合深度調整 沖
44、裁模的上、下模要有良好的配合,即應保證上、下模的工作零件凸、凹模相互咬合深度要適少,不能太深與太淺,應以能沖下合適的零件為準。凸、凹模的配合深度.是依靠調節(jié)壓力機連桿長度來實現的。 3.凸、凹模間隙調整 沖裁模的凸、凹模間隙要均勻。對于有導向零件的沖模,其調整比較方便,只要保證導向件運動順利而無發(fā)澀現象即可保證間隙值;對于無導向沖模,可以在凹模刃口周圍襯以紫銅皮或舊紙板進行調整,也可以用透光及塞尺測試方法在壓機上調整,直到上、下模的凸、凹?;ハ鄬χ?,且間隙均勻后,用螺釘將沖模緊固在壓力機上,進行試沖。試沖后檢查一下試沖的零件.看是否有明顯毛刺及斷面質量,不合適應松開下模,再按前述方法繼續(xù)調
45、整,直到間隙合適為止。 4.定位裝置的調整 檢查沖模的定位零件如定位銷、定位塊、定位板,是否符合定位要求,定位是否可靠。假如位置不合適,在調整時應進行修整,必要時要進行更換。 5.卸料系統(tǒng)的調整 卸料系統(tǒng)的調整主要包括卸料板或頂件器是否工作靈活;卸料彈簧及橡膠彈性是否足夠;卸料器的運動行程是否足夠;漏料孔是否暢通無阻;打料桿、推料桿是否能順利推出制品與廢料。若發(fā)現故障.應給以調整,必要時可重新更換。 6. 導向機構的調試 導柱、導套要有好的配合精度,保證模具運動平穩(wěn)、可靠。 4.2.2沖裁模的調試方法 (1)將裝配后的模具順利的裝在指定的壓力機上。
46、 (2)用指定的坯料(或材料)穩(wěn)定地在模具上指出合格的制品零件。 (3)檢查制品零件的質量,若發(fā)現制品零件有缺陷,應分析原因,設法對模具進行修整和調試,知道能生產出一批完全符合圖樣要求的零件為止。 (4)根據設計要求,進一步確定出某些模具須經試驗后所決定的尺寸,并修整這些尺寸,直到符合要求為止。 (5)在試模時,應排除影響生產、安全、質量和操作等各種不利因素,使模具達到能穩(wěn)定、批量生產的目的。 (6)經試模后,為公藝部門提供編制模具成批生產制品的工藝規(guī)程依據。 4.2.3 沖裁模試沖時出現的問題及調試方法 沖模安裝后即可進行試沖,在試沖過程
47、中,可能會出現這樣或那樣的毛病,這時必須要根據所產生的毛病原因.確定正確的調制與修整方法,以使其正常工作。 該沖裁模試沖時出現的問題及調整方法如下表所示:表1 存在問題 產生原因 調整方法 送料不通暢或料 被卡住 ① 凸模與卸料板之間間隙過大,使搭邊翻扭 ② 兩導料板之間的尺寸過小或有斜度 ① 減小凸模與卸料板之間的間隙 ② 根據情況銼修或磨或重裝 制件有毛刺 ① 刃口不鋒利或淬火硬度低 ② 配合間隙過大或過小 ③ 間隙不均勻使沖件的一邊有顯著的帶斜角的毛刺 ① 刃磨刃口,使其鋒利 ② 調整凸凹模之間間隙 卸料不正常 由于裝配不正確,使卸料機構不
48、能動作 休整卸料板 刃口相啃 上模座下模座固定板凹模墊板等零件安裝面不平行 修整有關零件,重新裝上模或下模 凹模被脹裂 凹??子械瑰F現象,即上口大,下口小,或凹模刃口深度太長,積存的制件太多,脹力太大 修整凹模刃口,消除倒錐現象或減小凹模刃口長度,使沖下的制件盡快漏下 由相關資料可知,毛刺的產生是由很多原因造成的。上述刃口變鈍只是其一種,故在調整沖模時,應從多方面來分析,直至沖出合格的沖壓件來。 例如,由于凸、凹模之間局部間隙大,會使沖壓件局部產生毛刺,造成沖壓件質量不好。此時可將間隙大的一邊另鑲人一塊鑲件后重新做刃口,使之間隙均勻,消除毛刺。若無法鑲件時,可以采用
49、熱壓辦法來解決.其方法是:將凹模加熱到800℃左、右.用壓柱在毛刺大的部位(間隙大)壓之。 在熱壓時,壓柱的面積最好要大,經壓而敲出的部位最少可為0.3一O.4mm,深度為6—7mm,熱壓后材料內部產生組織應力和熱應力,應立即將凹模進行正?;幚?,然后再重新精加工此凹???,使之間隙合適,毛刺減小。 對于間隙不是很大情況下,也可以用擠壓的方法使之間隙往小變化,即在離凹模刃口3—4mm處(未經淬火或經淬火后應退火的凹模)用壓塊通過手錘力使孔往中心部位擠壓,來促使間隙變小,使之合
50、適。 凹模經淬硬后發(fā)現間隙小而沖出有毛刺時,則可以用油石修磨一下,使間隙增大一點,有時孔若縮小的很多,可以用研磨桿研磨—下即可。 4.2.4 彎曲模的調試要點 1.彎曲模上、下模在壓力機上的相對位置調整 由于該模具是無導向裝置的彎曲模。上、下模在壓力機上的相對位置.一般由調節(jié)壓力機連桿的長度方法調整。在調整時,最好把事先制做的樣件放在模具的工作位置上(凹模型腔內),然后調節(jié)壓力機連桿,使上模隨滑塊調整到下極點時,即能壓實樣件又不發(fā)生硬性頂撞及咬死現象。然后將下模緊固。 2.凸、凹模間隙的調整 上、下模在壓力機上的相對位置粗略調整后.再在凸模下平面與下
51、模卸料板之間墊一塊比坯件略厚的墊片( 一般為彎曲坯料厚度的1—1.2倍),繼續(xù)調節(jié)連桿長度,一次又一次用手搬動飛輪,直到使滑塊能正常地通過下死點而無阻滯的情況下為止。 上、下模的側向間隙,可采用墊紙板或標準樣件的方法來進行調整,以保證間隙的均勻性。間隙調整后,可將下模板固定、試沖。 3.定位裝置的調整 彎曲模定位零件的定位形狀應與坯件相一致。在調整時,應充分保證其定體的可靠性和穩(wěn)定性。利用定位塊及定位釘的彎曲模,假如試沖后,發(fā)現位置及定位不準確,應及時調整定位位置或更換定位零件。 4.卸件、退件裝置的調整 彎曲模的卸料系統(tǒng)行程應足夠大,卸料
52、用彈簧或橡皮應有足夠的彈力;頂出器及卸料系統(tǒng)應調整到動作靈活,并能順利地卸出制品零件,不應有卡死及發(fā)澀現象。卸料系統(tǒng)作用于制品的作用力要調整均衡,以保證制品卸料后表面平整,不致于產生變形和翹曲。 4.2.5彎曲模的調試方法 (1)將裝配后的模具順利的裝在指定的壓力機上。 (2)用指定的坯料(或材料)穩(wěn)定地在模具上指出合格的制品零件。 (3)檢查制品零件的質量,若發(fā)現制品零件有缺陷,應分析原因,設法對模具進行修整和調試,知道能生產出一批完全符合圖樣要求的零件為止。 (4)根據設計要求,進一步確定出某些模具須經試驗后所決定的尺寸,并修整這些尺寸,直到符合要求為止。
53、 (5)在試模時,應排除影響生產、安全、質量和操作等各種不利因素,使模具達到能穩(wěn)定、批量生產的目的。 (6)經試模后,為公藝部門提供編制模具成批生產制品的工藝規(guī)程 4.2.6 彎曲模試沖時出現的問題及調試方法 該彎曲模試沖時出現的問題及調整方法如下所示:表2 存在問題 產生原因 調整方法 制件產生回彈 彈性變形的存在 ① 減小凸凹模之間間隙 ② 改變凸模的形狀和角度大小 ③ 增加凹模型槽的深度 制件表面有擦傷 ① 凹模的內壁和圓角處 表面不光,太粗糙 ② 板料被粘附在凹模表面 ① 將凹模內壁及圓角修光,在凸?;虬寄5墓ぷ鞅砻驽冇层t厚0.02㎜
54、 ② 將凹模進行化學熱處理如氮化處理 制件底部平面 不平 ① 壓料力不足 ② 頂件用頂桿的著力點 分布不均,將制件底面頂 變形 ① 增大壓料力最好校正一下 ② 將頂桿位置分布均勻頂桿面積不可太小 彎曲角變形部 分有裂紋 ① 彎曲半徑太小 ② 毛坯有毛刺的一面向外 ③ 材料的塑性差 ① 加大彎曲半徑 ② 使毛刺在彎曲的內側 ③ 將板料進行退火處理 制件尺寸過長或不一 ① 間隙過小或材料擠長 ② 壓料裝置的力過大將料擠長 ③ 計算錯誤 ① 加大間隙 ② 減小壓料裝置的壓力 ③ 落料尺寸應在彎曲模試沖后確定 5 結束語 固定夾屬于落料沖孔工序和
55、彎曲工序的復合件,分析其工藝性,并確定工藝方案。根據計算確定本制件是一次沖裁和一次彎曲復合加工而成的,由于制件為半圓形彎曲因此沖裁模和彎曲模在設計時應分開設計。本設計主要是設計各個零件的配合,由于模具較復雜零件較多,可以逐步確定模具的總體尺寸和模具零件的結構,然后根據上面的設計繪出模具的總裝圖。 由于在零件制造前進行了預測,分析了制件在生產過程中可能出現的缺陷,采取了相應的工藝措施。因此,模具在生產零件的時候才可以減少廢品的產生。 由于固定夾的形狀結構一般,而且高度不太高,因此在落料沖孔復合沖裁模設計
56、時適合選用標準模架,由于彎曲模不是標準模架,因此在設計時應自主設計。要保證零件的順利加工和取件,必須有足夠的高度,因此必須選好模架以達到要求。模具工作零件的結構由于對稱,它相應的簡化了模具結構,便與以后的操作、調整和維護。 固定夾模具的設計,是理論知識與實踐有機的結合,更加系統(tǒng)地對理論知識做了更深切貼實的闡述。也使我認識到,要想做為一名合理的模具設計人員,必須要有扎實的專業(yè)基礎,并不斷學習新知識新技術,樹立終身學習的觀念,把理論知識應用到實踐中去,并堅持科學、嚴謹、求實的精神,大膽創(chuàng)新,突破新技術,為國民經濟的騰飛做出應有的貢獻。 致 謝 首先感謝本人的導師于智宏老
57、師,她在我做畢業(yè)設計之際提出了很多寶貴的意見和建議。由于本人資質有限,很多知識掌握的不是很牢固,因此在設計中難免要遇到很多難題,在有課程設計的經驗及老師的不時指導和同學的熱心幫助下,克服了一個又一個的困難,使我的畢業(yè)設計日趨完善。畢業(yè)設計雖然很辛苦,但是在設計中不斷思考問題,研究問題,咨詢問題,一步步提高了自己,一步步完善了自己。同時也汲取了更完整的專業(yè)知識,鍛煉了自己獨立設計的能力,使我受益匪淺,我相信這些經驗對我以后的工作一定有很大的幫助,而且也鍛煉我的吃苦耐勞的精神,讓我在這個競爭的社會里有立足之地。于智宏老師淵博的知識,誠懇的為人,使我受益匪淺,在畢業(yè)設計的過程中,特別是遇到困難時,她
58、給了我鼓勵和幫助,在這里我向她表示真誠的感謝! 感謝母?!幽蠙C電高等專科學校的辛勤培育之恩!感謝材料工程系給我提供的良好學習及實踐環(huán)境,使我學到了許多新的知識,掌握了一定的操作技能。 感謝和我在一起進行課題研究的同窗張金果、張書寧同學,和她們在一起討論、研究使我受益非淺。 最后感謝各位老師在三年之中的教導和在做設計的過程中對我的幫助。使我在大學三年里不但學到了更多知識,而且學到了怎么做人、怎么做事。在此衷心對各位老師的辛勤教導表示感謝。雖然我就要走出學校進入社會,但是老師對我的教導和幫助我想我一輩子也不會忘記!那講課的聲音在我耳邊久久回蕩,那寫字的身影在腦海里留下了深深的印記,如果還
59、有下一次做學生我仍然選擇做您的學生! 我非常慶幸在三年的的學習、生活中認識了很多可敬的老師和可親的同學,感激師友的教誨和幫助,并向你們致意崇高的敬意,以后到社會上我一定努力工作,不辜負你們給予我的知識和對我寄予的厚望!!畢業(yè)之后,我一定會努力工作的,不辜負各位老師對我們的深切期望,在這里也說一聲:老師你辛苦了。 祝各位老師,身體健康、萬事如意! 參考文獻 [1] 原紅玲主編.沖壓模具設計與制造 [M].北京:機械工業(yè)出版社,2008 [2]翟德梅、段維峰主編.模具制造技術 M
60、].北京:化學出版社,2005 [3]趙志偉等.模具發(fā)展現狀[J].模具制造,2007,6:2~4 [4]劉建超、張保忠主編.沖壓模具設計與制造 [M].北京:高等教育出版社,2004 [5 ]孝陪主編.沖壓成形工藝及模具簡明手冊 [M] . 北京:機械工業(yè)出版社,2000 [6]具制造手冊編寫組.模具制造手冊 [M].北京:機械工業(yè)出版社, 1996 [7]炳堯韓泰榮蔣文生主編.模具設計與制造簡明手冊 [M].上??茖W技術出版社,1998 [8]賈潤禮程志遠主編.實用沖模設計手冊 [M].中國輕工業(yè)出版社,2000 [9]唐志玉主編.模具設計師指南 [M].國防工業(yè)出版社,1999 [10]建聲主編.簡明模具工實用技術手冊 [M].機械工業(yè)出版社,1993 [11]紹林、馬長福主編.實用模具技術手冊 [M].上海:科學技術出版,1998 [12]陳錫棟、周小玉主編.實用模具技術手冊[M].北京:機械工業(yè)出版社,2001 28
- 溫馨提示:
1: 本站所有資源如無特殊說明,都需要本地電腦安裝OFFICE2007和PDF閱讀器。圖紙軟件為CAD,CAXA,PROE,UG,SolidWorks等.壓縮文件請下載最新的WinRAR軟件解壓。
2: 本站的文檔不包含任何第三方提供的附件圖紙等,如果需要附件,請聯系上傳者。文件的所有權益歸上傳用戶所有。
3.本站RAR壓縮包中若帶圖紙,網頁內容里面會有圖紙預覽,若沒有圖紙預覽就沒有圖紙。
4. 未經權益所有人同意不得將文件中的內容挪作商業(yè)或盈利用途。
5. 裝配圖網僅提供信息存儲空間,僅對用戶上傳內容的表現方式做保護處理,對用戶上傳分享的文檔內容本身不做任何修改或編輯,并不能對任何下載內容負責。
6. 下載文件中如有侵權或不適當內容,請與我們聯系,我們立即糾正。
7. 本站不保證下載資源的準確性、安全性和完整性, 同時也不承擔用戶因使用這些下載資源對自己和他人造成任何形式的傷害或損失。
最新文檔
- 2025年防凍教育安全教育班會全文PPT
- 2025年寒假安全教育班會全文PPT
- 初中2025年冬季防溺水安全教育全文PPT
- 初中臘八節(jié)2024年專題PPT
- 主播直播培訓提升人氣的方法正確的直播方式如何留住游客
- XX地區(qū)機關工委2024年度年終黨建工作總結述職匯報
- 心肺復蘇培訓(心臟驟停的臨床表現與診斷)
- 我的大學生活介紹
- XX單位2024年終專題組織生活會理論學習理論學習強黨性凝心聚力建新功
- 2024年XX單位個人述職述廉報告
- 一文解讀2025中央經濟工作會議精神(使社會信心有效提振經濟明顯回升)
- 2025職業(yè)生涯規(guī)劃報告自我評估職業(yè)探索目標設定發(fā)展策略
- 2024年度XX縣縣委書記個人述職報告及2025年工作計劃
- 寒假計劃中學生寒假計劃安排表(規(guī)劃好寒假的每個階段)
- 中央經濟工作會議九大看點學思想強黨性重實踐建新功