機械畢業(yè)設計(論文)-汽車空調缸體前蓋工藝及擴Φ9孔夾具設計【全套圖紙】
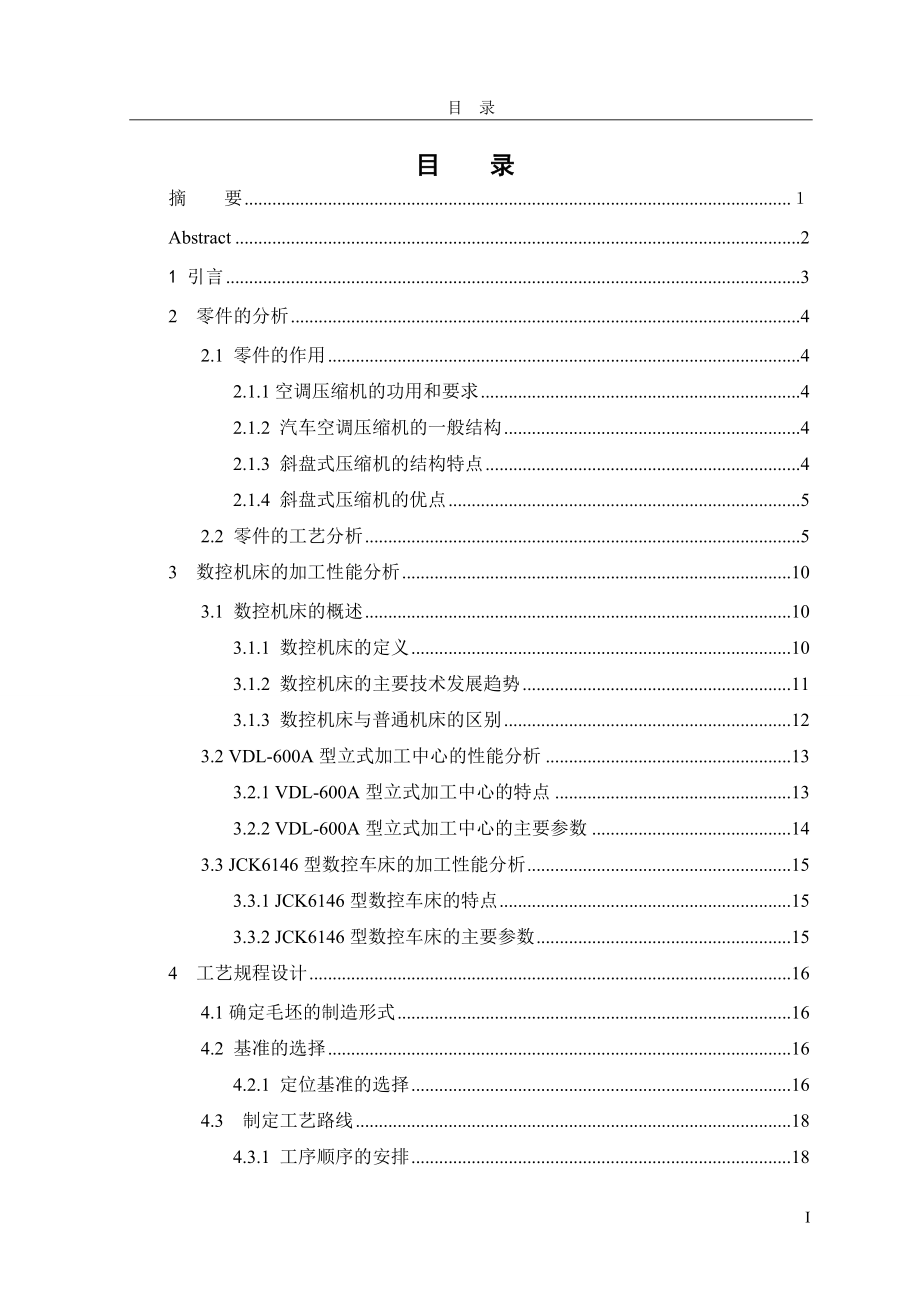


《機械畢業(yè)設計(論文)-汽車空調缸體前蓋工藝及擴Φ9孔夾具設計【全套圖紙】》由會員分享,可在線閱讀,更多相關《機械畢業(yè)設計(論文)-汽車空調缸體前蓋工藝及擴Φ9孔夾具設計【全套圖紙】(46頁珍藏版)》請在裝配圖網(wǎng)上搜索。
1、目 錄 I 目目 錄錄 摘 要 Abstract 2 1 引言3 2 零件的分析4 2.1 零件的作用4 2.1.1 空調壓縮機的功用和要求.4 2.1.2 汽車空調壓縮機的一般結構4 2.1.3 斜盤式壓縮機的結構特點4 2.1.4 斜盤式壓縮機的優(yōu)點5 2.2 零件的工藝分析5 3 數(shù)控機床的加工性能分析10 3.1 數(shù)控機床的概述10 3.1.1 數(shù)控機床的定義10 3.1.2 數(shù)控機床的主要技術發(fā)展趨勢11 3.1.3 數(shù)控機床與普通機床的區(qū)別12 3.2 VDL-600A 型立式加工中心的性能分析 .13 3.2.1 VDL-600A 型立式加工中心的特點 .13 3.2.2 VDL
2、-600A 型立式加工中心的主要參數(shù) .14 3.3 JCK6146 型數(shù)控車床的加工性能分析.15 3.3.1 JCK6146 型數(shù)控車床的特點.15 3.3.2 JCK6146 型數(shù)控車床的主要參數(shù).15 4 工藝規(guī)程設計16 4.1 確定毛坯的制造形式.16 4.2 基準的選擇16 4.2.1 定位基準的選擇16 4.3 制定工藝路線18 4.3.1 工序順序的安排18 目 錄 II 4.3.2 加工階段的劃分.18 4.3.3 工藝方案的分析.19 4.4 機械加工余量,工序尺寸及毛坯尺寸的確定19 4.4.1 加工余量19 4.4.2 工序余量的影響因素19 4.4.3 加工余量的確
3、定19 4.4.4 工序尺寸與公差的確定20 4.4.5 工藝尺寸鏈20 4.4.6 時間定額和提高生產(chǎn)率的工藝途徑21 4.5 工藝分析.22 4.6 確立切削用量及基本工時.23 5專用夾具設計.31 5.1 機床夾具概述.31 5.1.1 機床夾具及其組成.31 5.2 VDL-600A 型加工中心夾具設計 .32 5.2.1 問題的提出32 5.2.2 定位基準的選擇.32 5.2.3 定位誤差分析.32 5.2.4 夾緊裝置的確定.33 5.2.5 切削力和夾緊力計算.35 5.2.6 定位元件的選擇38 5.2.7 夾具體的設計及其它元件的選擇40 5.2.8 繪制夾具總裝配圖、零
4、件圖及配合與公差的選擇41 結 論43 致 謝44 參考文獻45 摘 要 摘摘 要要 本次畢業(yè)設計的任務是完成汽車壓縮機前缸蓋的加工工藝和相關夾具的設計。 根據(jù)生產(chǎn)要求和技術要求,編寫了機械加工工藝卡片,并且設計了相關工序所用的 工裝夾具。制定合理的工藝要求,可以提高壓縮機的制冷效果和密封效果,也能夠 提高壓縮機的使用壽命。機械加工工藝是實現(xiàn)產(chǎn)品設計,保證產(chǎn)品的質量,節(jié)約能 源降低消耗的重要手段,是企業(yè)進行生產(chǎn)準備,計劃調度,加工操作,安全生產(chǎn), 技術檢測和健全勞動組織的重要依據(jù),也是企業(yè)上品種,上質量,上水平加速產(chǎn)品 更新提高經(jīng)濟效益的技術保證。而大批生產(chǎn)的 GDC-170 型壓縮機的設計采
5、用鋁合金 高壓鑄造,通過使用數(shù)控機床、數(shù)控加工中心進行加工,保證了零件的加工精度。 相應的夾具本著裝卸簡單,使用方便的原則,結合數(shù)控加工中心進行總體設計,以 達到工件的裝夾及生產(chǎn)技術的要求。 關鍵字關鍵字:壓縮機前缸蓋;加工中心;工藝規(guī)程; 夾具 全套圖紙,加全套圖紙,加 153893706 Abstract 2 Abstract The graduation design task is to be completed after the car compressor cylinder and the rear cover the processing and related fixture
6、 design. According to the production and technical requirements, the preparation of the mechanical processing card, and the design of related processes used in the fixture. Formulate a reasonable technical requirement can improve compressor refrigeration effect and sealing effect, also to improve th
7、e life of the compressor. Mechanical processing technology is to achieve product design, to ensure the quality of products, reduce consumption of energy conservation an important means Enterprise is ready for production, planning and scheduling, processing operations, security, technical testing and
8、 perfecting labor organizations, the important basis Enterprise is also on the species, on quality, on the level of accelerated product upgrade technology to ensure cost-effective. And the production of a large number of GDC - 162-type compressor designed with high-pressure cast aluminum alloy, thro
9、ugh the use of CNC machine tools, CNC machining centers for processing, guarantee the accuracy of the processing components. In the corresponding fixture handling simple, easy-to-use, combined CNC machining centers for design, to achieve workpiece fixturing and production technology requirements. Ke
10、y words:A body front the compressor; Process the center; technological process; Tongs 引言 3 1 1 引言引言 隨著空調的進一步發(fā)展,越來越來多的企業(yè)和個人對空調有了更新的認識。在 空調歷史中,美國已經(jīng)發(fā)展和改進了有風管的中央單元式系統(tǒng),并得到了正在現(xiàn)場 安裝和修理有風管的單元式空調系統(tǒng)的空調設備分銷商和經(jīng)銷商的強力支持。WRAC 是最簡單和最便宜的系統(tǒng),能夠很容易的在零售商店中購得,并在持續(xù)高溫來的時 候自己安裝。同時,無風管的 SRAC 和 SPAC 自 70 年代起在有別于美國市場的動力下 在日本得到
11、發(fā)展和改進。之后,設備設計和制造技術在 90 年代被轉讓到中國,這是 通過與當?shù)毓?包括主要元件如壓縮機、熱交換器、電勸機、精細閥和電子控制器 的本地制造商)組成的合資公司進行的。在 90 年代中國也從其它先進國家吸收了較 大型空調設備的先進高新技術,并與多數(shù)是美國的大公司組成合資企業(yè)?,F(xiàn)今,中 國已是一個頂級國家,她的當?shù)刂饕S和合資企業(yè)制造了大量 SRAC 和 SPAC 以滿 足增長的國內市場和出口需要。 而汽車空調更加以驚人的速度給世人帶來驚喜。隨著汽車動力的更新和新技術 的應用,對汽車空調系統(tǒng)提出了新的挑戰(zhàn),也給許多新技術的應用創(chuàng)造了機會?!懊商?利爾議定書“規(guī)定,原來在汽車空調系
12、統(tǒng)使用的工質12,在發(fā)達國家的使用已經(jīng) 在 1996 年停止,在發(fā)展中國家則在 2006 年停止。由于各方面的努力,12 已逐 漸被134所取代,我國從 2001 年 1 月 1 日起已禁止在新生產(chǎn)的車輛中使用 12 為工質的汽車空調。134具有(大氣臭氧層破壞指數(shù))為零、 (溫室效應指數(shù))為12 的六分之一、不可燃、低毒性、制冷量和系統(tǒng)性 能與12 相當?shù)葍?yōu)點,因而作為“過渡性“的替代工質在世界范圍內得到認可,但 由于它的溫室效應指數(shù)仍然較高(為2的 1300 倍),已列入“京都協(xié)議“規(guī)定限制發(fā) 展的工質范疇。 空調壓縮機作為空調系統(tǒng)的核心力量,為汽車提供制冷、取暖、除霜、除霧、 空氣過濾和
13、濕度控制功能。本文以 GDC-170 汽車空調壓縮機為例,全面分析壓縮機 的前缸蓋的加工工藝,以數(shù)控加工中心和數(shù)控車床為主要機床,作為此零件的加工 載體,以確保零件的精度。夾具作為加工零件的主要載體,它的安裝精度和調整方 法也就更加重要。而本文以數(shù)控加工中心上的裝夾夾具為例,全面分析此夾具的設 計思路和設計原理,用典型的一面兩銷來達到零件夾緊的目的。 2 零件的分析 4 2 零件的分析零件的分析 2.1 零件的作用零件的作用 2.1.1 空調壓縮機的空調壓縮機的功用和要求功用和要求 1.空調壓縮機的功用 壓縮機是汽車空調的心臟,是維持制冷劑在制冷系統(tǒng)的循環(huán),吸收來自蒸發(fā)器 的低溫、低壓制冷劑蒸
14、汽,壓縮制冷蒸汽使其壓力和溫度升高,并將制冷劑送往冷 凝器。 2.空調壓縮機的要求 汽車空調壓縮機與一般用途的壓縮機相比,在結構和性能上有下列特殊的要求: 1) 制冷能力強,尤其要求有良好的低速性能,以確保汽車在低速行駛和怠速是 也有足夠的制冷能力。 2) 節(jié)省動力,尤其是汽車在高速行駛時動力消耗不能過大,否則不僅使經(jīng)濟性 降低,還會影響汽車的動力性。 3) 對于轎車和輕型汽車來說,壓縮機必須在發(fā)動機艙有限的空間內安裝固定, 因此要求壓縮機的體積和質量都要小。 4) 汽車在高溫怠速的情況下,發(fā)動機艙里的壓縮機溫度可達 120。C;汽車行駛 時顛簸震動也很大,要求壓縮機在高溫和顛簸的情況下能正常
15、工作。 5) 要求壓縮機啟動、運轉平穩(wěn)、震動小、噪聲低、工作可靠。 2.1.2 汽車空調壓縮機的一般結構汽車空調壓縮機的一般結構 曲軸連桿式壓縮機式是一種應用較為廣泛的制冷劑壓縮機,現(xiàn)在大、中型客車 匯總仍然在使用。壓縮機的活塞在氣缸內不斷地運動,改變拉氣缸的容積,從而在 制冷系統(tǒng)中起到了壓縮和輸送制冷劑的作用。其構造簡單,主要有活塞、曲軸、氣 缸、進氣閥和排氣閥。工作過程可分為壓縮、排氣、膨脹、吸氣等四個過程。 2.1.3 斜盤式壓縮機斜盤式壓縮機的結構特點的結構特點 斜盤式壓縮機是一種軸向往復活塞式壓縮機。目前,它是汽車空調壓縮機中使 用最為廣泛的一種。國內常見的轎車,如奧迪轎車、捷達轎車
16、以及富康等轎車皆采 用斜盤式壓縮機,作為汽車空調的制冷壓縮機。 2 零件的分析 5 斜盤式壓縮機的主要零件由缸體,前后缸蓋,前后閥板,活塞。它的斜盤固定 在主軸上,鋼球用滑靴和活塞的聯(lián)結架固定。鋼球的作用是使斜盤的旋轉運動經(jīng)鋼 球轉換為活塞的直線運動時,由滑動變?yōu)闈L動。這樣可減少摩擦阻力和磨損,以及 延長滑板的使用壽命。如今斜盤和滑靴都以耐磨質輕的高硅鋁合金材料,活塞也用 硅鋁合金。這樣既減輕拉壓縮機運動機件的質量,又可提高壓縮機的轉速。 由于斜盤式壓縮機的活塞雙向作用,所以在它的兩邊都裝有前、后閥總成,各 總成上都裝有吸氣閥片和排氣閥片。且前后缸蓋上有個自相通的吸氣腔和排氣搶, 吸、排氣腔用
17、閥墊隔開。 2.1.4 斜盤式壓縮機的優(yōu)點斜盤式壓縮機的優(yōu)點 由于斜盤式壓縮機無連桿結構,所以工作可靠,結構也緊湊,體積小,重量輕, 排氣脈沖比曲軸連桿式小。且它是軸向臥式結構,所以能方便地直接安裝在發(fā)動機 機體上,而不需要另配機架,這些都是斜盤式壓縮機的優(yōu)點。 2.22.2 零件的工藝分析零件的工藝分析 壓縮機缸蓋是空調壓縮機上的重要零件,工藝技術要求的高低直接影響到空調 壓縮機的制冷和密封,因此制定合理的工藝要求,可以提高壓縮機的制冷效果和密 封效果,也能夠提高壓縮機的使用壽命。機械加工工藝是實現(xiàn)產(chǎn)品設計,保證產(chǎn)品 的質量,節(jié)約能源降低消耗的重要手段,是企業(yè)進行生產(chǎn)準備,計劃調度,加工操
18、作,安全生產(chǎn),技術檢測和健全勞動組織的重要依據(jù),也是企業(yè)上品種,上質量, 上水平加速產(chǎn)品更新提高經(jīng)濟效益的技術保證。 現(xiàn)在分別簡述一下汽車空調壓縮機后缸蓋重要的工藝技術要求。 JCK6146 數(shù)控車床加工表面,其間有一定位置要求。分述如下: 1. 粗車大端 以不加工的大端面作為粗基準,車大端面,保證外圓直徑為 114mm,深度 12 . 0 08 . 0 為 170.03mm,粗糙度為6.3;將作為后續(xù)加工定位的基準,為達到工件的性能要 a R 求,要求其平面度公差為 0.02mm,與貫穿孔中心距為 20.7mm。 0.3 0 2 零件的分析 6 圖 2.1 2. 精車大端 車大端內徑,保證內
19、徑尺寸為,內孔底面和貫穿孔的中心距為, 0 0.10 106 0 0.30 34.8 內孔底面與大端面的中心距為,如圖 2.1 所示。 0 0.1 54.5 3.精車小端 軸承外徑尺寸為mm,主要影響離合器裝配;線圈直徑mm,主 0.01 0.03 30 0 0.04 64 要影響離合器配合;距離mm,主要影響皮帶輪卡簧裝配;內徑mm,為 0.1 0 27 0.01 0.05 23 2 零件的分析 7 后工序擠光留余量;距離 7.50.1mm 和mm,主要影響軸封卡簧裝配;外徑 0.2 0 1.3 mm,深度 0.6mm,影響軸封卡簧裝配;如圖 5.3 所示。 0.2 0.3 24 0.2 0
20、 4. 銑貫穿孔兩端面 寬度要求為 830.08mm,主要影響工件在機車上的裝配,其粗糙度為3.2, a R 與 114mm 的對稱度公差為 0.15mm,如圖 2.4 所示。 圖 2.4 5.鉆定位銷孔 要求定位銷孔相對大端和 114mm 的中心軸線的位置度公差為 0.2mm,銷孔 徑為mm,孔的加工表面粗糙度為3.2,孔深度為 90.2mm,主要影 0.1 0 3.2 a R 響零件之間的裝配;如圖 2.5 所示。 2 零件的分析 8 圖 2.5 6. 加工線夾部位 鉆mm 孔,主要影響線夾的固定,如圖 2.6 所示。60.1 圖 2.6 7.擴螺紋連接孔 鉆孔徑為mm 孔,要求孔相對大端
21、內孔底面和工件軸向的設計基準的90.3 位置度為,且有最大實體要求,主要影響整機的裝配,如圖 2.7 所示.0.3 2 零件的分析 9 圖 2.7 8. 鉆貫穿孔 如圖 2.7 所示,要求孔徑為 9mm 和 11,孔間距為 1380.2mm,大孔 0.3 0 0.1 0 深度為 10mm,保證與機車連接確保精度。 0.6 0.3 圖 2.8 9.孔擠光23 按工藝要求,對mm 孔擠光處理,以大端的外徑和大端底面為加工基準,23 表面粗糙度為3.2,要求比較高,如圖 2.9 所示。 a R 3 數(shù)控機床的加工性能分析 10 3 數(shù)控機床的加工性能分析數(shù)控機床的加工性能分析 3.1 數(shù)控機床的概述
22、數(shù)控機床的概述 3.1.1 數(shù)控機床的定義數(shù)控機床的定義 數(shù)字控制(Numerical control)是用數(shù)字化信號對機床的運動及其加工過程進行 控制的一種控制方法。 數(shù)控技術是用數(shù)字信息對機械運動和工作過程進行控制的技術,是現(xiàn)代化加工 的一門新型的,發(fā)展十分迅速的高新技術。數(shù)控裝備是以數(shù)控技術為代表的新技術 對傳統(tǒng)制造產(chǎn)業(yè)和新興制造業(yè)的滲透形成的機電一體化產(chǎn)品,即所謂的數(shù)字化裝備; 其技術范圍所覆蓋的領域有:機械制造技術;微電子技術;信息處理、加工、傳輸 拉術;自動控制技術;伺服驅動技術;檢測監(jiān)控技術、傳感器技術;軟件技術等。 數(shù)控技術及裝備是發(fā)展新興高新技術產(chǎn)業(yè)和尖端工業(yè)(如信息技術及其
23、產(chǎn)業(yè)、生物技 術及其產(chǎn)業(yè)、航空、航天等國防工業(yè)產(chǎn)業(yè))的使能技術和最基本的裝備。在提高牛產(chǎn) 率、降低成本、保證加工質量及改善工人勞動強度等方面,都有突出的優(yōu)點;待別 是在適應機械產(chǎn)品迅速更新?lián)Q代、小批量、多品種生產(chǎn)方面,各類數(shù)控裝備是實現(xiàn) 先進制造技術的關鍵。 數(shù)控機床是采用了數(shù)控技術的機床,或者說是裝備了數(shù)控系統(tǒng)的機床。國際信 息處理聯(lián)盟第五技術委員會,對數(shù)控機床作如下定義:數(shù)控機床是一種裝了程序控 制系統(tǒng)的機床。該系統(tǒng)能邏輯地處理具有使用號碼或其他符號編碼指令規(guī)定的程序。 數(shù)控機床,是把數(shù)字化了的刀具移動軌跡的信息輸入數(shù)控裝置,經(jīng)過譯碼運算, 從而實現(xiàn)控制工件與刀具相對運動,加工出所需零件的
24、一種機床。國際信息處理聯(lián) 盟第五技術委員會對數(shù)控機床的定義是:數(shù)控機床是一個裝有程序控制系統(tǒng)的機床, 該系統(tǒng)能夠邏輯地處理具有使用號碼或其他符號編碼指令規(guī)定的程序。即數(shù)控機床 是采用了數(shù)控技術的機床或裝備了數(shù)控裝置的機床。數(shù)控機床較好地解決了復雜、 精密、小批、多變的零件加工問題,是一種靈活的、高效的自動化機床。為滿足制 造業(yè)不斷追求優(yōu)質、高效、低成本、及時、清潔衛(wèi)生的目標,作為現(xiàn)代制造業(yè)的主 流制造裝備的數(shù)控機床,在高速、高效、精密化、工序復合、功能化、柔性化和系 統(tǒng)化方面有了新的發(fā)展。數(shù)控機床已經(jīng)成為現(xiàn)代制造業(yè)的主流制造裝備。在全世界 現(xiàn)有的 1400 萬臺機床中,數(shù)控機床約占 100 萬
25、臺,機床擁有量數(shù)控率約 7%,數(shù)控 機床己成為我國制造業(yè)中的基礎制造裝備。工業(yè)部門對數(shù)控機床的要求,優(yōu)先考慮 3 數(shù)控機床的加工性能分析 11 的側重點略有不同。例如,汽車工業(yè)主要要求速度更快,實現(xiàn)高速高效加工;而航空 航天工業(yè)希望更多地實現(xiàn)零部件的完全加工,即能使工件在一次裝夾中完成全部或 大部分加工;中小型企業(yè)則更重視機床的柔性。 3.1.2 數(shù)控機床的主要技術發(fā)展趨勢數(shù)控機床的主要技術發(fā)展趨勢 1.高速化和高速高效加工 高速加工不但可以大幅度提高加工效率、縮短加工時間、降低加工成本,而且 可以使零件加工質量和加工精度達到更高水平。數(shù)控機床只有通過高速化,大幅度 縮短切削工時,才可能進一步
26、提高其生產(chǎn)率。數(shù)控機床的全面高速化,主要體現(xiàn)在 如下幾方面:高的主軸轉速、高的快速移動速度和進給速度,各坐標軸高的加減速度, 高的換刀速度(換刀時間或刀架轉位時間短),控制系統(tǒng)更高的數(shù)據(jù)處理速度。高速 加工的切削速度比傳統(tǒng)的高 5-6 倍,進給速度也相應提高,目前,高速加工中心大 部分采用高速電主軸。主軸最高轉速可達 40000 r/min -50r/min 。目前有資料介 紹主軸速度甚至可達每分鐘 20 萬轉,主軸功率一般為 40kw。 2.高精密和超精密加工 提高數(shù)控機床的加工精度,可通過減少數(shù)控系統(tǒng)的誤差和采用補償技術來實現(xiàn), 如提高數(shù)控系統(tǒng)的分辨率;使 CNC 控制單元精細化;提高位置
27、檢測精度(日本交流伺服 電動機有的己安裝每轉可產(chǎn)生 100 萬個脈沖的內藏位置檢測器,位置檢測精度能達 到 0.01 Inn/脈沖)。目前加工中心的定位精度就已由過去的士 5 fm 提高到士 1pn。 3.工序復合化和復合加工 銼銑類加工中心是工序復合化數(shù)控機床的典型代表,它把銑、鍵、鉆、鉸、攻 螺紋等工序復合在一臺機床上,粗、精加工兼容,減少了工件在其加工過程中的裝 夾次數(shù)和定位調整時間,提高了加工精度和效率。工序復合化在加工中心概念的帶 動下滲透到各類數(shù)控機床上,出現(xiàn)了車削中心、車銑中心、磨削中心、齒輪加工中 心及各種復合加工中心。車削中心具備 C 軸功能和動力刀架;車銑中心又增加了 Y
28、軸 和 13 軸功能,可使工件在一次裝夾后完成全部加工。復合加工的工藝范圍在不斷擴 大,如切削和磨削、切削與電加工,以及切削和激光加工復合在一起。對置式雙主 軸雙轉塔刀架的車削中心或車銑中心,解決了工件夾持端的加工問題,從而實現(xiàn)了 全部加工。 4.柔性化、系統(tǒng)化、智能化 3 數(shù)控機床的加工性能分析 12 由于計算機技術和信息技術的飛速發(fā)展,推動數(shù)控系統(tǒng)更快地更新?lián)Q代。世界 上許多 CNC 生產(chǎn)廠家利用 PC 機豐富的軟硬件資源,開發(fā)出開放式體系結構,使 CNC 有更好的通用性、柔性、適應性、可擴展性,并可適應向智能化、網(wǎng)絡化發(fā)展的需 要。開放式體系結構的新一代 CNC 系統(tǒng),由于其硬、軟件規(guī)范
29、都是對外開放的,這 就使 CNC 制造商和用戶進行系統(tǒng)集成都得到有利的支持,也為針一對用戶的二次開 發(fā)帶來極大方便,促進了 CNC 多檔次,多品種的開發(fā)和廣泛應用,通過擴展構成不 同類型數(shù)控機床的 CNC 系統(tǒng)。數(shù)控機床在控制性能上的發(fā)展趨勢是智能化。CNC 系 統(tǒng)引入了自適應控制,模糊控制和神經(jīng)網(wǎng)絡的控制機理,實現(xiàn)學習控制、工藝參數(shù) 自動生成,三維刀具補償、運動參數(shù)動態(tài)補償、前饋控制等功能。在運行故障診斷 中,專家系統(tǒng)使自診斷和故障監(jiān)控功能更趨完善。智能化伺服系統(tǒng)使主軸驅動和進 給系統(tǒng)能自動識別負載并自動優(yōu)化調整參數(shù)。智能型 CNC 使數(shù)控系統(tǒng)通過全閉環(huán)的 信息傳遞而具有自律控制能力,確保整
30、個加工過程以最優(yōu)性能指標穩(wěn)態(tài)運行。各種 自律控制器使智能型數(shù)控機床適應智能控制系統(tǒng)的要求。 5.先進制造系統(tǒng) 柔性制造單元(FMC-Flexible Manufacturing Cell)是一種幾乎不用人參與而能 連續(xù)地對同一類型零件中不同零件進行自動化加工的最小加工單元,它既可以做為 獨立使用的加工設備,又可以作為柔性制造系統(tǒng)或柔性自動線的基本組成模塊。柔 性制造系統(tǒng)(FMS-Flexible Manufacturing System)是由加工系統(tǒng)、物料自動儲運系 統(tǒng)和信息控制系統(tǒng)三者相結合并能自動運轉的制造系統(tǒng)。這種系統(tǒng)可按任意順序加 工一組不同工序與不同加工節(jié)拍的零件,工藝過程隨加工零件
31、的不同作適當調整, 能在設備的技術范圍內自動地適應加工零件和生廠規(guī)模的變化。計算機集成制造系 統(tǒng)(CIMS-Computer IntergratedManufacturing System)是 1974 年美國的約瑟 夫哈林頓博士首先提出的。CIMS 是一種企業(yè)經(jīng)營管理的哲理,它強調企業(yè)的生產(chǎn) 經(jīng)營是一個整體,必須用系統(tǒng)工程的觀點來研究解決生產(chǎn)經(jīng)營中出現(xiàn)的問題。集成 是核心,它不僅是設備的集成,更主要的是以信息為主導的技術集成和功能集成。 3.1.3 數(shù)控機床與普通機床的區(qū)別數(shù)控機床與普通機床的區(qū)別 數(shù)控車床與普通機床主要區(qū)別在以下幾個方面: 1. 高精度 數(shù)控車床控制系統(tǒng)的性能不斷提高,機械
32、結構不斷完善,機床精度日益提高。 2. 高效率. 隨著新刀具材料的應用和機床結構的完善,數(shù)控車床的加工效率、主軸轉速、 3 數(shù)控機床的加工性能分析 13 傳動功率不斷提高,使的新型數(shù)控車床的空轉動時間大為縮短。其加工效率比臥式 車床高(25)倍。加工零件越復雜,越體現(xiàn)出數(shù)控車床的高效率加工特點。 3. 高柔性 數(shù)控車床具有高柔性,適應 70以上的多品種、小批量零件的自動加工。 4. 高可靠性 隨著數(shù)控系統(tǒng)的性能提高,數(shù)控機床的無故障工作時間迅速提高。 5. 工藝能力強 數(shù)控車床既能用于粗加工又能用于精加工,可以在一次裝夾中完成零件全部或 大部分工序。 6. 模塊化設計 數(shù)控車床的設計多采用模塊
33、化原則設計。 現(xiàn)在,數(shù)控車床技術還在不斷向前發(fā)展著。數(shù)控車床發(fā)展趨勢如下:隨著數(shù)控 系統(tǒng)、機床結構和刀具材料的技術發(fā)展,數(shù)控車床將向高速化發(fā)展,進一步提高主 軸轉速、刀架快速移動以及轉位換刀速度:工藝和工序將更加復合化和集中化;數(shù) 控車床相多主軸、多刀架加工方向發(fā)展;為實現(xiàn)長時間無人化全自動操作,數(shù)控車 床向全自動化方向發(fā)展;機床的加工精度向更高方向發(fā)展。同時,數(shù)控車床也向簡 易型發(fā)展。 3.2 VDL-600A 型立式加工中心的性能分析型立式加工中心的性能分析 3.2.1 VDL-600A 型立式加工中心的特點型立式加工中心的特點 1.提高加工質量 工件一次裝夾,即可實現(xiàn)多工序集中加工,大大
34、減少多次裝夾所帶來的誤差。 另外,由于是數(shù)控加工,較少依賴操作者的技術水平,可得到相當高的穩(wěn)定精度。 2.縮短加工準備時間 加工中心既然可以頂替多臺通用機床,那么加工一個零件所需準備時間,是每 臺加工單元所損耗的準備時間之和。從這個意義上說,加工中心的準備時間顯然短 得多。另外,由于是數(shù)控加工,不必準備專用鉆模等工藝裝備,可以大大節(jié)省準備 時間。 3.減少在制品 以往的加工方法是工件流動于多臺通用機床之間,這就要有相當數(shù)量的在制品, 而在加工中心上加工,可發(fā)揮其“多工序集中”的優(yōu)勢,在一臺機床上完成多個工 序,大大減少在制品數(shù)量。 3 數(shù)控機床的加工性能分析 14 4.減少刀具費 把分散設置各
35、個通用機床上的刀具,集中在加工中心刀庫上,有可能用最少量 的刀具,實現(xiàn)公共有效利用。這樣既提高刀具利用率,又減少了刀具數(shù)量。 5.最少的直接勞務費 由 NC 裝置實現(xiàn)多工序加工的信息集約化和一人多臺管理,以及用工作臺自動托 盤交換裝置(Automatic Pallet Changer 簡稱 APC)等輔助裝置,實現(xiàn)夜間無人運 轉。這些都可縮減直接勞務費。 6.最少的間接勞務費 由于工序集中,搬運和質量檢查工作量大為減少,這就使間接勞務費最少。 7.設備利用率高 加工中心設備利用率為通用機床的幾倍。另外,由于工序集中,容易適應多品 種、中小批量生產(chǎn)。 3.2.2 VDL-600A 型立式加工中心
36、的主要參數(shù)型立式加工中心的主要參數(shù) 見下表 1 所示: 表 1 立式加工中心主要技術參數(shù) 工作臺規(guī)格(長寬)mm800 x420 工作臺最大載重kg500 X 坐標行程mm600 Y 坐標行程mm420 Z 坐標行程mm520 主軸中心線到立柱導軌面距離mm511 主軸端面至工作臺上平面距離mm150670 X、Y、Z 切削速度mm010000 X、Y、Z 快速進給速度mm24/24/20 主軸轉速范圍r/min608000 (10000) 主軸錐孔No.40 (7:24 ) 主軸功率kW (FANUC 0i-MC:8/8000:71/47.4 Nm) X/Y/Z 伺服電機功率kW3/3/3
37、(FANUC 0i-MC) 表 1 (續(xù)) 立式加工中心主要技術參數(shù) 刀庫容量(24 把刀臂式可選)(斗笠式) 刀柄BT40 刀具最大重量kg7 刀具最大直徑mm 100/130(刀臂式 77/110) 換刀時間(刀對刀)mm6-8 (刀臂式 2.5s) 工作臺 T 型槽(槽數(shù)槽寬槽距)mm318125 定位精度 X、Z:mm0.020Y:0.016(國標)0.005(JIS) 重復定位精度 X、Z:mm0.008Y:0.006(國標)0.003(JIS) 數(shù)控系統(tǒng)FANUC 0i MC 氣源壓力MPa0.4-0.6 3 數(shù)控機床的加工性能分析 15 機床輪廓尺(LWH)mm231020402
38、337 機床重量kg4800 3.3 JCK6146 型數(shù)控車床的加工性能分析型數(shù)控車床的加工性能分析 3.3.1 JCK6146 型數(shù)控車床的特點型數(shù)控車床的特點 CK/CJK6146 選用帝特馬公司 DTM-5T 控制系統(tǒng) 該系列數(shù)控車床其機械部分是采用引進的日本 YAMAZAK 公司的技術,選用優(yōu)質 材料加工而成。其數(shù)控系統(tǒng)選用北京帝特馬公司的 DTM5T 系統(tǒng)。所選用的數(shù)控系 統(tǒng)功能齊全,可靠性高。 該數(shù)控機床在結構上突出了精度、精度保持性、可靠性、可擴展性、安全性、 易操作和可維修性等;主軸傳動采用日本 NSK 軸承。適用于對回轉體、軸噘和盤類 零件進行直線、圓弧、曲面、螺紋、溝槽、
39、和維面等高效、精密、自動車削加工。 3.3.2 JCK6146 型數(shù)控車床的主要參數(shù)型數(shù)控車床的主要參數(shù) 見下表 2 所示 表 2 JCK6146 型數(shù)控車床的主要參數(shù) 床身上最大回轉直徑mm460 滑板上最大回轉直徑mm200 頂尖距mm1000 主軸頭規(guī)格/主軸通孔直徑mmA2-8/直徑 80(MK 主軸) 主軸錐孔 ASA350(MK 主軸) 主軸轉速范圍 齒輪傳動rpm25-1800 主電機類型三相異步變頻電機 主電機功率kw7.5 4 工藝規(guī)程設計 16 4 工藝規(guī)程設計工藝規(guī)程設計 4.1 確定毛坯的制造形式確定毛坯的制造形式 零件為 ADC12 鋁合金材料。它的強度不高,不能熱處
40、理強化,在退火狀態(tài)下 有高的塑性,而蝕性好,焊接性好,切削加工性不良。用于制造要求高可塑性和良 好焊接性、在液體或氣體介質中工作的低載荷零件,如缸體、油箱、油管、液體容 器等。 4.2 基準的選擇基準的選擇 定位基準對于機械加工來說就相當于基礎,要選擇好基準才能夠加工出高精度 的產(chǎn)品。在這次畢業(yè)設計當中我通過采用大端面和壓板實現(xiàn)了設計基準和工藝基準 重合的目的,在一定程度上提高了產(chǎn)品的生產(chǎn)效率和產(chǎn)品質量。 4.2.1 定位基準的選擇定位基準的選擇 1.基準的概念及分類 零件上用以確定其它點、線、面的位置所依據(jù)的那些點、線、面稱為基準。根 據(jù)其功用的不同,可分為設計基準、工藝基準兩大類。 設計基
41、準 在零件圖上用以確定其它點、線、面的基準,稱為設計基準。 工藝基準 零件在加工、測量、裝配等工藝過程中使用的基準統(tǒng)稱工藝基準。 工藝基準又可分為: 1) 裝配基準 在零件或部件裝配時用以確定它在機器中相對位置的基準。 2) 測量基準 用以測量工件已加工表面所依據(jù)的基準。例如以內孔定位用百 (千)分表測量外圓表面的徑向跳動,則內孔就是測量外圓表面徑向跳動的測量基 準。 3) 工序基準 在工序圖中用以確定被加工表面位置所依據(jù)的基準。所標注的 加工面的位置尺寸稱工序尺寸。工序基準也可以看作工序圖中的設計基準。 4) 定位基準 用以確定工件在機床上或夾具中正確位置所依據(jù)的基準。如軸 類零件的中心孔就
42、是車、磨工序的定位基準。 作為基準的點、線、面有時在工件上并不一定實際存在(如孔和軸的軸線、 某兩面之間的對稱中心面等),在定位時是通過有關具體表面起定位作用的,這些 表面稱定位基面。例如在車床上用頂尖撥盤安裝一根長軸,實際的定位表面(基面) 是頂尖的錐面,但它體現(xiàn)的定位基準是這根長軸的軸線。因此,選擇定位基準,實 際上既選擇恰當?shù)亩ㄎ换妗?4 工藝規(guī)程設計 17 2. 定位基準的選擇原則 根據(jù)定位基面表面狀態(tài),定位基準又可分為粗基準和精基準。凡是以未經(jīng)過 機械加工的毛坯表面作定位基準的,稱為粗基準,粗基準往往在第一道工序第一次 裝夾中使用。如果定位基準是經(jīng)過機械加工的,稱為精基準。精基準和
43、粗基準的選 擇原則是不同的。 粗基準的選擇 粗基準的選擇,主要考慮如何保證加工表面與不加工表面之間的位置和尺寸 要求,保證加工表面的加工余量均勻和足夠,以及減少裝夾次數(shù)等。具體原則有以 下幾方面: 1) 如果零件上有一個不需加工的表面,在該表面能夠被利用的情況下,應盡量 選擇該表面作粗基準。 2) 如果零件上有幾個不需要加工的表面,應選擇其中與加工表面有較高位置精 度要求的不加工表面作第一次裝夾的粗基準。 3) 如果零件上所有表面都需機械加工,則應選擇加工余量最小的毛坯表面作粗 基準。 4) 同一尺寸方向上,粗基準只能用一次。 5) 粗基準要選擇平整、面積大的表面。 精基準的選擇 選擇精基準時
44、,主要應考慮如何保證加工表面之間的位置精度、尺寸精度和裝 夾方便,其主要原則是: 1) 基準重合原則 即選設計基準作本道加工工序的定位基準,也就是說應盡量 使定位基準與設計基準相重合。這樣可避免因基準不重合而引起的定位誤差。 2) 基準統(tǒng)一原則 在零件加工的整個工藝過程中或者有關的某幾道工序中盡可 能采用同一個(或一組)定位基準來定位,稱為基準統(tǒng)一原則。 3) 互為基準原則 若兩表面間的相互位置精度要求很高,而表面自身的尺寸和 形狀精度又很高時,可以采用互為基準、反復加工的方法。 4) 自為基準原則 如果只要求從加工表面上均勻地去掉一層很薄的余量時,可 采用以加工表面本身作定位基準。 4 工藝
45、規(guī)程設計 18 4.3 制定工藝路線制定工藝路線 4.3.1 工序順序的安排工序順序的安排 工序順序的安排原則: 1. 先加工基準面,再加工其它表面 2. 一般情況下,先加工平面,后加工孔 3. 先加工主要表面,后加工次要表面 4. 先安排粗加工工序,后安排精加工工序 4.3.2 加工階段的劃分加工階段的劃分 當零件的精度要求比較高時,若將加工面從毛坯面開始到最終的精加工或精密 加工都集中在一個工序中連續(xù)完成,則難以保證零件的精度要求,或浪費人力、物 力資源。 由于是大批量生產(chǎn),大量采用專用機床和專用夾具,使工序盡量集中提高生產(chǎn) 率,除此之外還能降低成本。 壓縮機前缸蓋的工藝路線: 1) 粗車
46、大端 2) 精車大端 3) 精車小端 4) 銑貫穿孔端面 5) 鉆定位銷孔 6)加工線夾部位 7) 鉆螺栓聯(lián)接孔 8) 銑貫穿孔 9) 擠光 10) 清洗烘干 11)浸滲 12)工件清理 13)終檢入庫 4.3.3 工藝方案的分析工藝方案的分析 壓縮機前缸蓋工藝方案的分析 此工藝方案的特點在于:先加工大端面,再以大端面作為定位基準,分別進行 螺紋,柱塞孔,貫穿面加工等。 4 工藝規(guī)程設計 19 根據(jù)實際情況考慮到從粗加工到精加工,根據(jù)先面后孔,螺紋底孔中心線應與 110mm 端面相垂直,垂直度公差為 0.05mm,位置度公差為 0.3mm,由此可見, 因為螺紋底孔的中心線要求與 110mm 大
47、端面保持垂直且保證一定的位置度,因此, 加工及測量螺紋底孔時應以大端面為基準。這樣做,能保證設計基準與工藝基準相 重合。 以上工藝過程詳見機械加工工藝卡片。 4.4 機械加工余量,工序尺寸及毛坯尺寸的確定機械加工余量,工序尺寸及毛坯尺寸的確定 4.4.1 加工余量加工余量 毛坯尺寸與零件設計尺寸之差稱為加工總余量 4.4.2 工序余量的影響因素工序余量的影響因素 1.上工序的尺寸公差 a T 2.上道工序產(chǎn)生的表面粗糙度(表面輪廓最大高度)和表面缺陷層深度 Ha y R 在本道工序加工時,應將它們切除掉。 3.上工序留下的需要單獨考慮的空間誤差,用符號 ea 表示。 4.本工序的裝夾誤差綜上所
48、述, 1)對于單邊余量 2)對于雙邊余量 4.4.3 加工余量的確定加工余量的確定 1.計算法 1) 鏜孔、鉸孔、拉孔 2) 磨外圓 3) 光整加工 2.查表法 3.經(jīng)驗法 4.4.4 工序尺寸與公差的確定工序尺寸與公差的確定 生產(chǎn)上絕大部分加工面都是在基準重合的情況下進行加工。所以,掌握基準重合情 況下工序尺寸與公差的確定過程非常重要。 4.4.5 工藝尺寸鏈工藝尺寸鏈 1. 直線尺寸鏈的基本計算公式 1) 極值法計算公式 (1) 封閉環(huán)的基本尺寸等于各組成環(huán)基本尺寸的代數(shù)和 4 工藝規(guī)程設計 20 (2) 封閉環(huán)的公差等于各組成環(huán)的公差之和 (3) 封閉環(huán)的上偏差等于所有增環(huán)的上偏差之和減
49、去所有減環(huán)的下偏差之和 (4) 封閉環(huán)的下偏差等于所有增環(huán)的下偏差之和減去所有減環(huán)的上偏差 2) 概率法計算公式 (1) 將極限尺寸換算成平均尺寸 (2) 將極限偏差換算成中間偏差 (3) 封閉環(huán)中間偏差的平方等于各組成環(huán)中間偏差平方之和。 2. 直線尺寸鏈在工藝過程中的應用 1) 工藝基準和設計基準不重合時工藝尺寸的計算 (1) 測量基準和設計基準不重合 (2) 定位基準和設計基準不重合 2) 一次加工滿足多個設計尺寸要求的工藝尺寸計算 3. 表面淬火、滲碳層深度及鍍層、涂層厚度工藝尺寸鏈 對那些要求淬火或滲碳處理,加工精度要求又比較高的表面,常常在淬火或滲 碳處理之后安排磨削加工,為了保證
50、磨后有一定厚度的淬火層或滲碳層,需要進行 有關的工藝尺寸計算。 4. 余量校核 校核加工余量,對加工余量進行必要的調整是指定工藝規(guī)程時不可少的工藝工 作。 4.4.6 時間定額和提高生產(chǎn)率的工藝途徑時間定額和提高生產(chǎn)率的工藝途徑 1. 時間定額 1) 時間定額的概念 時間定額是指在一定生產(chǎn)條件下,規(guī)定生產(chǎn)一件產(chǎn)品或完 成一道工序所消耗的時間。 2) 時間定額的組成 (1) 基本時間 t基 (2) 輔助時間 t輔 (3) 布置工作地時間 t布置 (4) 休息和生理需要時間 t休息 (5) 準備與終結時間 t準備 3) 單件時間和單件工時定額計算公式 (1) 單件生產(chǎn)時 單件時間的計算公式:T 單
51、件= t+ t+ t+ t 基輔布置休息 4 工藝規(guī)程設計 21 (2) 成批生產(chǎn)時 單件工時定額的計算公式:T = T+ t /n 定額單件準備 (3) 大量生產(chǎn)時 單件工時定額的計算公式: T = T 定額單件 2. 提高生產(chǎn)率的工藝途徑 1) 縮短基本時間 提高切削用量縮短基本時間,提高切削用量的主要途徑是進行新型刀具材料的 研究與開發(fā)。 2) 采用復合工步縮短基本時間 (1) 多刀單件加工 (2) 單刀多件或多刀多件加工 (3) 將工件串聯(lián)裝夾或并聯(lián)裝夾進行多件加工,可有效地縮短基本時間。 3. 減少輔助時間和輔助時間與基本時間重疊 1) 減少輔助時間 (1) 采用先進夾具或自動上、下
52、料裝置減少裝、卸工件的時間。 (2) 提高機床操作的機械化與自動化水平,實現(xiàn)集中控制、自動調速與變速以 縮短開、停車床和改變切削用量的時間。 2) 使輔助時間與基本時間重疊 (1) 采用可換夾具或可換工作臺,在機床外裝夾工件,可使裝夾工件的時間與 基本時間重疊。 (2) 采用轉位夾具或轉位工作臺,可在加工中完成工件的裝卸,使裝卸時間與 基本時間基本重疊。 (3) 采用回轉夾具或回轉工作臺進行連續(xù)加工 (4) 采用在線檢測的方法來控制加工過程中的尺寸,使測量時間與基本時間重 疊。 3) 減少布置工作地時間 減少布置工作地時間,可在減少更換刀具的時間方面采取措施。 4) 減少準備與終結時間 準備與
53、終結時間的多少,與工藝文件是否詳盡清楚、工藝裝備是否齊全、安裝、 調整是否方便有關。 4.5 工藝分析工藝分析 根據(jù)上述原始資料及加工工藝,分別確定各加工表面的機械加工余量,工序尺 寸及毛坯尺寸如下: 4 工藝規(guī)程設計 22 1.粗車大端外徑,由于采用模鑄,毛坯外形誤差較小,工序尺寸要求為 114mm, 查工藝手冊表 2.2-32.2-5,加工余量為 1mm,則毛胚尺寸為 116mm。 2.精車大端內徑,工序尺寸要求為 106mm,查工藝手冊表 2.2-32.2-5, 加工余量 2mm,毛胚尺寸為 108mm。 3.精車小端,包括外徑和內徑,工序尺寸要求分別為 30mm 和 23mm,查 工藝
54、手冊表 2.2-32.2-5,加工余量 2mm,毛胚尺寸分別為 32 和 26mm。 4.銑貫穿孔兩端面,工序尺寸要求為 83mm,查工藝手冊表 2.2-32.2-5, 加工余量為 2mm, 毛胚尺寸為 85mm。 5.鉆定位銷孔,工序尺寸要求為銷孔徑為 3.2mm, 查工藝手冊表 2.2- 32.2-5,加工余量為 0.6mm, 毛胚尺寸為 4.4mmm。 6.加工線夾部位,包括一個通孔和一個螺紋孔,工序尺寸要求分別為 6mm 和 M5-6H, 查工藝手冊表 2.2-32.2-5,加工余量為 0.6,毛胚尺寸為 7.2mm 和 6.2mm。 7.擴螺栓連接孔,工序尺寸為 9mm, 查工藝手冊
55、表 2.2-32.2-5,加工 余量為 2mm, 毛胚尺寸為 11mm。 8.銑貫穿孔,工序尺寸為 11mm, 查工藝手冊表 2.2-32.2-5,加工余量 為 2mm, 毛胚尺寸為 13mm。 9. 23 孔擠光,按工藝圖定位后順底孔擠光即可。 10. 清洗烘干。 11. 浸滲,按浸滲工藝執(zhí)行。 12工件清理。 13. 終檢入庫。 4.6 確立切削用量及基本工時確立切削用量及基本工時 工序一 粗車大端 1.加工條件 工件材料:鋁合金 加工要求:車大端直徑 機 床:JCK6146 刀 具:外圓車刀、切斷刀 2.切削用量 4 工藝規(guī)程設計 23 1)切削深度為:0.8mm p a 2)進給量為:
56、 =0.5mm/r , 根據(jù)機械工藝手冊P874 表 27-2 得 z f 3)確定切削速度:根據(jù)機械工藝手冊表 27-12、 27-11得: 262/3.1 1 0.8 =105.6m/min vv V Cv xy mp C Vk T af 4)確定主軸轉速: =305.7m/min s n C 1000V w d 5)計算基本工時 根據(jù)工藝手冊P666 表 12-3得: Tj =0.06min L i fn 123 L m LL f 工序二 精車大端 1.加工條件 工件材料:鋁合金 加工要求:車大端內徑 機 床:CKS6116 刀 具:外圓車刀、內孔車刀、端面車刀、外圓切槽刀 2.切削用量
57、 1)切削深度為:0.8mm p a 2)進給量為: =0.5mm/r , 根據(jù)機械工藝手冊P874 表 27-2 得 z f 3)確定切削速度:根據(jù)機械工藝手冊表 27-12、 27-11得: 262/3.1 1 0.8 =105.6m/min vv V Cv xy mp C Vk T af 4)確定主軸轉速: =305.7m/min s n C 1000V w d 5)計算基本工時 根據(jù)工藝手冊P666 表 12-3得: Tj =0.06min L i fn 123 L m LL f 4 工藝規(guī)程設計 24 工序三 精車小端 1.加工條件 工件材料:鋁合金 加工要求:軸承外徑mm,線圈直徑
58、mm,內徑mm, 0.01 0.03 30 0 0.04 64 0.01 0.05 23 外徑mm, 0.2 0.3 24 機 床:數(shù)控車床 刀 具:外圓車刀、內孔車刀、端面車刀、外圓切槽刀、內圓切槽刀 2.選擇切削用量 1)車削深度: 選擇=2mm, p a 2)進給量:查切削手冊表 2.7 得, f=0.18=0.09mm/r5 . 0 3)確定切削速度:根據(jù)切削手冊表 2.13 及表 2.14,按 5 類加工性考慮 得:v=26.25m/min =1286r/min s n C 1000V w d5 . 6 25.261000 按機床選取 n =1200r/min(按工藝手冊表 4.2-
59、2) w 所以實際切削速度 v=24.49 m/min 1000 w dn 1000 12005 . 6 4)計算基本工時 查機械制造工藝設計簡明手冊P196 表 6.2-5 L=12mm L =D-d1ctykr+(1-2)=1.58 L =(1-3)=2mm 12 取 f =f* n =0.16 2280=364.8mm/r mw T=3minj fn LLL w 21 41 . 0 136 410150 式中:L=150mm L =10mm L =4mm 12 工序四 銑貫穿孔兩端 1.加工條件 工件材料:鋁合金 加工要求:銑兩端的貫穿孔端面 機 床:立銑床 刀 具:雙面盤銑刀 4 工藝
60、規(guī)程設計 25 2.選擇切削用量 1)銑削深度: 選擇=2mm p a 2)進給量:查切削手冊表 2.7 得, f=0.18=0.09mm/r5 . 0 3)確定切削速度:根據(jù)切削手冊表 2.13 及表 2.14,按 5 類加工性考慮 得:v=26.25m/min =1286r/min s n C 1000V w d5 . 6 25.261000 按機床選取 n =1200r/min(按工藝手冊表 4.2-2) w 所以實際切削速度 v=24.49 m/min 1000 w dn 1000 12005 . 6 4)計算基本工時 查機械制造工藝設計簡明手冊 P196 表 6.2-5 L=12mm
61、 L =D-d1ctykr+(1-2)=1.58 L =(1-3)=2mm 12 取 f =fn =0.16 2280=364.8mm/r mw T=3minj fn LLL w 21 41 . 0 136 410150 式中:L=150mm L =10mm L =4mm 12 工序五 鉆定位銷孔 1.加工條件 工件材料:鋁合金 加工要求:銷孔孔徑為 3.2mm, 1 . 0 0 機 床:鉆床 刀 具:3.2mm 麻花鉆 2.選擇切削用量 1)鉆削深度: 選擇=2mm, p a 2)進給量:查機械加工技術手冊P1321 表 15-5.33 得, f=0.16-0.2 mm/r 取 f=0.16
62、mm/r 3)計算切削速度 查機械加工技術手冊 P1324 表 15-37 得, v= 1.25-1.5m/s 取 V=75m/min 采用直徑為 d=7.5mm,則 4 工藝規(guī)程設計 26 n =3185r/min s d v 1000 5 . 7 751000 查機械制造工藝設計簡明手冊表 4.2-18 取 n =3180r/min w 故實際的切削速度為 v=75m/min 1000 w dn 1000 31805 . 7 4)計算基本工時 查機械制造工藝設計簡明手冊P196 表 6.2-5 L=12mm L = 1.58 L =(1-3)=2mm 12 取 f =f n =0.1631
63、80=508.8mm/r mw T=0.03minj m f LLL 21 8 . 508 58.15 工序六 加工線夾部位 1.加工條件 工件材料:鋁合金 加工要求:鉆 60.1mm 孔 機 床:鉆床 刀 具:6mm 麻花鉆 2.選擇切削用量 1)鉆削深度 選擇=2mm p a 2)每轉進給量 查機械加工技術手冊P1341 表 15-54 得, f=0.5-1.2mm/r 取 f=1 mm/r 3)計算切削速度 查機械加工技術手冊 P1341 表 15-55 得, v= 180-300m/min. 取 V=180m/min 采用麻花鉆的直徑為 d=6 mm,則 n =879r/min s d
64、 v 1000 5 . 30 1801000 查機械制造工藝設計簡明手冊表 4.2-39 取 4 工藝規(guī)程設計 27 n =880r/min w 故實際的切削速度為 v=84.277m/min 1000 w dn 1000 879 5 . 30 4)計算基本工時 查機械制造工藝設計簡明手冊P198 表 6.2-7 L=90mm L =0.5(D-)+(13)=10.4mm L =(1-3)=2mm 1 2 2 e aD 2 機械加工技術手冊表 15-49 ae=(0.4-0.8)d0=0.5d0=0.5125=62.5 取 f =f* n =490mm/r mw T=0.21minj m f LLL 21 490 4 . 102 工序七 擴螺紋連接孔 1.加工條件 工件材料:鋁合金 加工要求:內孔徑直徑為 22.5mm,深度為 13mm,擋圈槽槽寬為 06 . 0 0 3 . 0 1 . 0 1.3mm ,密封槽直徑 26.50.05mm 1 . 0 0 機 床:多軸鉆床 刀 具:9 麻花鉆 2.選擇切削用量 1) 切削深度 選擇=0.6mm p a 2)每轉進給量 查機械加工技術手冊P1341 表 15-54 得, f=0.3-0.4mm/r 取 f=0.3mm/r 3)確定切削速度:根據(jù)機械工藝
- 溫馨提示:
1: 本站所有資源如無特殊說明,都需要本地電腦安裝OFFICE2007和PDF閱讀器。圖紙軟件為CAD,CAXA,PROE,UG,SolidWorks等.壓縮文件請下載最新的WinRAR軟件解壓。
2: 本站的文檔不包含任何第三方提供的附件圖紙等,如果需要附件,請聯(lián)系上傳者。文件的所有權益歸上傳用戶所有。
3.本站RAR壓縮包中若帶圖紙,網(wǎng)頁內容里面會有圖紙預覽,若沒有圖紙預覽就沒有圖紙。
4. 未經(jīng)權益所有人同意不得將文件中的內容挪作商業(yè)或盈利用途。
5. 裝配圖網(wǎng)僅提供信息存儲空間,僅對用戶上傳內容的表現(xiàn)方式做保護處理,對用戶上傳分享的文檔內容本身不做任何修改或編輯,并不能對任何下載內容負責。
6. 下載文件中如有侵權或不適當內容,請與我們聯(lián)系,我們立即糾正。
7. 本站不保證下載資源的準確性、安全性和完整性, 同時也不承擔用戶因使用這些下載資源對自己和他人造成任何形式的傷害或損失。
最新文檔
- 6.煤礦安全生產(chǎn)科普知識競賽題含答案
- 2.煤礦爆破工技能鑒定試題含答案
- 3.爆破工培訓考試試題含答案
- 2.煤礦安全監(jiān)察人員模擬考試題庫試卷含答案
- 3.金屬非金屬礦山安全管理人員(地下礦山)安全生產(chǎn)模擬考試題庫試卷含答案
- 4.煤礦特種作業(yè)人員井下電鉗工模擬考試題庫試卷含答案
- 1 煤礦安全生產(chǎn)及管理知識測試題庫及答案
- 2 各種煤礦安全考試試題含答案
- 1 煤礦安全檢查考試題
- 1 井下放炮員練習題含答案
- 2煤礦安全監(jiān)測工種技術比武題庫含解析
- 1 礦山應急救援安全知識競賽試題
- 1 礦井泵工考試練習題含答案
- 2煤礦爆破工考試復習題含答案
- 1 各種煤礦安全考試試題含答案