鍛件通用技術(shù)要求
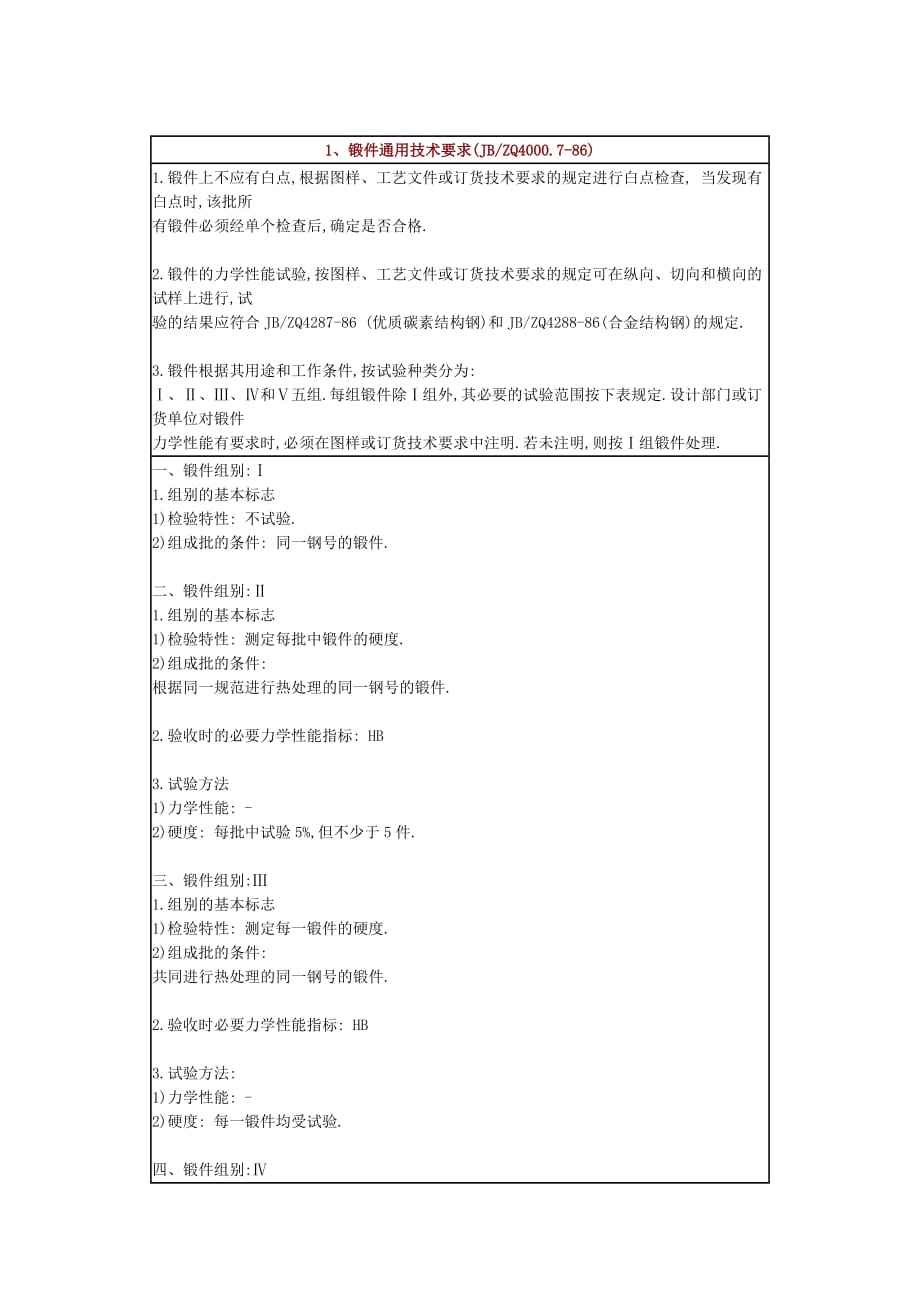


《鍛件通用技術(shù)要求》由會員分享,可在線閱讀,更多相關(guān)《鍛件通用技術(shù)要求(12頁珍藏版)》請在裝配圖網(wǎng)上搜索。
1、 1、鍛件通用技術(shù)要求(JB/ZQ4000.7-86) 1.鍛件上不應有白點,根據(jù)圖樣、工藝文件或訂貨技術(shù)要求的規(guī)定進行白點檢查, 當發(fā)現(xiàn)有白點時,該批所 有鍛件必須經(jīng)單個檢查后,確定是否合格. 2.鍛件的力學性能試驗,按圖樣、工藝文件或訂貨技術(shù)要求的規(guī)定可在縱向、切向和橫向的試樣上進行,試 驗的結(jié)果應符合JB/ZQ4287-86 (優(yōu)質(zhì)碳素結(jié)構(gòu)鋼)和JB/ZQ4288-86(合金結(jié)構(gòu)鋼)的規(guī)定. 3.鍛件根據(jù)其用途和工作條件,按試驗種類分為: Ⅰ、Ⅱ、Ⅲ、Ⅳ和Ⅴ五組.每組鍛件除Ⅰ組外,其必要的試驗范圍按下表規(guī)定.設(shè)計部門或訂貨單位對鍛件 力學性能有要求時,必須在圖樣或
2、訂貨技術(shù)要求中注明.若未注明,則按Ⅰ組鍛件處理. 一、鍛件組別:Ⅰ 1.組別的基本標志 1)檢驗特性: 不試驗. 2)組成批的條件: 同一鋼號的鍛件. 二、鍛件組別:Ⅱ 1.組別的基本標志 1)檢驗特性: 測定每批中鍛件的硬度. 2)組成批的條件: 根據(jù)同一規(guī)范進行熱處理的同一鋼號的鍛件. 2.驗收時的必要力學性能指標: HB 3.試驗方法 1)力學性能: - 2)硬度: 每批中試驗5%,但不少于5件. 三、鍛件組別:Ⅲ 1.組別的基本標志 1)檢驗特性: 測定每一鍛件的硬度. 2)組成批的條件: 共同進行熱處理的同一鋼號的鍛件. 2.
3、驗收時必要力學性能指標: HB 3.試驗方法: 1)力學性能: - 2)硬度: 每一鍛件均受試驗. 四、鍛件組別:Ⅳ 1.組別的基本標志 1)檢驗特性: 測定每一鍛件的硬度和每一批中的力學性能. 2)組成批的條件: 共同進行熱處理的同一爐號的鍛件. 2.驗收時的必要力學性能指標: σs或σb, δ5, ψ, αk 3.試驗方法 1)力學性能: 試驗數(shù)量. a.鍛件重量在10kg以下,每批在300件以下者,試驗2件;每批超過300件者,試驗0.5%,但不少于2件. b.鍛件重量超過10-20kg,每批在200件以下者,試驗2件:每批超過200件者,試
4、驗1%,但不得少于2件. c.鍛件重量超過20kg,每批超過150件以下者,試驗2件;每批超過150者,試驗1.5%,但不得少于3件. 2)硬度: 每一鍛件均受試驗,選擇具有極限的毛坯作力學性能試驗. 五、鍛件組別:Ⅴ 1.組別的基本標志 1)檢驗特性: 測定每一鍛件的力學性能. 2)組成批的條件: 每一鍛件均單個驗收. 2.驗收時的必要力學性能指標: σs或σb, δ5, ψ, αk 3.試驗方法 1)力學性能: 每一鍛件均受試驗. 2)硬度: 每一鍛件均受試驗. 注: 1.每批鍛件由同一圖號制造的鍛件組成, 允許在同一批鍛件中包括根據(jù)各種圖號制造的外
5、形尺寸近似的鍛件. 2.經(jīng)訂貨單位同意, 允許把各種牌號鋼制成的Ⅰ組鍛件組成一批. 3.對Ⅳ、Ⅴ組鍛件驗收時的必要力學性能指標σs和σb的選擇,應在圖樣或訂貨技術(shù)要求中規(guī)定,如無 規(guī)定,由制造廠工藝部門決定. 4.鍛件的驗收規(guī)則和試驗方法按標準要求進行. 2、鑄件通用技術(shù)要求(JB/ZQ4000.5-86) 1.碳素鑄鋼應符合GB5678-85的規(guī)定; 合金鑄鋼應符合JB/ZQ4297-86的規(guī)定,耐熱鑄鋼應符合JB/ZQ4298的規(guī)定; 不銹鋼應符合JB/ZQ4299及JB/ZQ6009-84的規(guī)定. 2.灰鑄鐵應符合GB5675-85的規(guī)定; 球墨鑄鐵
6、應符合JB/ZQ4302-86的規(guī)定,耐熱鑄鐵應符合JB/ZQ4303-86的規(guī)定; 耐磨鑄鐵應符合JB/ZQ4303-86的規(guī)定. 3.鑄件尺寸公差等級分16級,見1-175 鑄件尺寸公差.plb, 單件小批生產(chǎn)一般按1-176 小批單件 毛坯尺寸公差.plb選用.公差帶應對稱于毛坯鑄件基本尺寸配置,即公差的一半位于正側(cè),另一半 位于負側(cè). 有特殊要求時,公差帶也可非對稱配置,但應在圖樣上標注. 4.鑄件內(nèi)、外圓角公差用1-175鑄件尺寸公差.plb中公差值作為上限,使其下限為零;壁厚公差可比 其它尺寸的一般公差降一級選用, 如圖樣上標明一般公差為CT10 級的話,則壁
7、厚公差選用CT11級. 5.特殊要求的公差, 應直接標注毛坯件基本尺寸的后面,如951.1. 特殊要求的公差可比一般公差 高或低.一般情況下不能低于1-176 小批單件毛坯尺寸公差.plb規(guī)定的公差等級范圍,當要求的 公差超過該庫規(guī)定的范圍時, 則經(jīng)有關(guān)方面協(xié)商后從1-175鑄件尺寸公差.plb中選取. 6.碳素鋼和低合金鋼(包括高錳鋼)鑄鋼件缺陷的補焊按JB/ZQ4000.6-86(鑄鋼件補焊通用技術(shù)條件) 規(guī)定執(zhí)行. 7.當鑄件補焊處的焊縫深度超過壁厚20%或25mm時,補焊后均應進行適當?shù)南龖崽幚? 補焊大型缺陷時,焊縫金屬量大,有必要時可在焊接到坡口的1
8、/3-1/處時進行一次中間退火, 消除 應力后再繼續(xù)焊滿坡口, 最后再做一次消除應力熱處理.補焊大型或碳當量(碳當量的計算見本標 準附錄A)超過0.4%的鑄鋼件的缺陷時, 在補焊后應立即入爐進行消除應力的熱處理. 8.設(shè)計人員根據(jù)鑄件的技術(shù)要求填寫下表,并將此表貼在鑄件圖樣的右上部. (鑄件技術(shù)要求) : 通用技術(shù)要求 JB/ZQ4000.5 鑄件尺寸公差要求 CT 密封試驗 是/否 耐壓試驗 是/否 注:表中空格中可補充其它技術(shù)要求. 3、焊接件通用技術(shù)要求(JB/ZQ400.3-86) 1.焊接結(jié)構(gòu)件的長度尺寸公差見1-245c 尺寸和形位公差數(shù)值.p
9、lb,適用于焊接零件和焊接組件的長度尺寸. 焊接件 的直線度.平面度和平行度公差見 1-245c 尺寸和形位公差數(shù).plb,焊接結(jié)構(gòu)件的尺寸公差與形位公差等級選用見 1-245b 尺寸和形位公差等級.plb 2.標注和未標注角度的偏差見1-246a 角度偏差.plb,角度偏差的公稱尺寸以短邊為基準邊, 其長度從圖樣標明的基 準點算起. 3.噴丸處理的焊接件,為了防止鋼丸鉆入焊縫, 必須焊接內(nèi)焊縫,并盡量避免內(nèi)室和內(nèi)腔.如果結(jié)構(gòu)上必須有內(nèi)室和內(nèi)腔, 則必須進行酸洗,以便達到表面除銹質(zhì)量等級Be(見JB/ZQ4000.10-86附錄A). 對此圖樣需作標注. 4.由平爐鋼
10、制造的低碳鋼結(jié)構(gòu)件, 可在任何溫度下進行焊接.但為了避免焊接過程產(chǎn)生裂紋及脆性斷裂, 厚度較大的焊 接件,焊削必須根據(jù)工藝要求,進行預熱和緩冷. 板厚超過30mm的重要焊接結(jié)構(gòu),焊后應立即消除內(nèi)應力,消除內(nèi)應力 采用550-600℃ 回火,或200℃局部低溫回火. 5.普通低合金結(jié)構(gòu)鋼制造的焊接件,必須按照焊接零件的碳當量和合金元素含量、零件的厚度、 鋼結(jié)構(gòu)件的用途和要求 進行焊前預熱和焊后處理,見表1 . 表1: 鋼號 厚度mm 焊前預熱℃ 焊后熱處理溫度 ℃ 09Mn2 不預熱 不處理 09Mn2Si 不預熱 不處理 09MnV 不預熱
11、不處理 12Mn 不預熱 不處理 16Mn ≤40 不處理或600-650回火 16MnRE >40 ≥ 100 不處理或600-650回火 14MnNb >40 ≥ 100 不處理或600-650回火 15MnV ≤32 不預熱 不處理或560-590,630-650回火 15MnTi >32 ≥ 100 不處理或560-590,630-650回火 14MnMoNb >32 ≥ 100 不處理或560-590,630-650回火 15MnVN ≤32 15MnVTiRE >32 >100 18MnMoVN
12、b ≥ 150 600-650回火 14MnMoV ≥ 150 600-650回火 4MnMoVB ≥ 150 在氣溫較低、 焊接件厚度較大的情況下焊接的普通低合金結(jié)構(gòu),應按表2的規(guī)定預熱. 表2 : 鋼板厚度 mm 焊接氣溫 ℃ 預熱溫度 ℃ ≤16 -10以下 100-150 16-24 -5以下 100-150 24-40 0以下 任何溫度 >40 0以下 任何溫度 6.有密閉內(nèi)腔的焊接件,在熱處理之前,應在中間隔板上適當?shù)奈恢眉庸う?0mm孔,使其空腔與外界相通.需在外壁上鉆孔的, 在熱處理后要重新堵上.
13、 7.焊縫射線探傷應符合GB3323-82的規(guī)定.要進行力學性能試驗的焊接,應在圖樣或訂貨技術(shù)要求中注明.焊縫的力學性能試 驗種類、試樣尺寸按GB2649-81-GB2656-81的規(guī)定,試樣板焊后與工件經(jīng)過相同的熱處理,并事選經(jīng)過外觀無損探傷檢查. 8.焊件要進行密封性檢驗和耐壓試驗時,應按本標準要求進行.對耐壓試驗有要求時, 應在圖樣或訂貨要求中注明試驗壓力 和試壓時間. 4、涂裝通用技術(shù)條件(JB/ZQ4000.10-88) 1.涂裝前對物體的表面要求應符合本標準的規(guī)定. 2.除銹后的金屬表面與涂底漆的間隔時間不得大于 6h,酸洗處理表面與第一次涂底漆時間
14、不少 于 48h,但無論間隔時間多少,涂漆前表面不得有銹蝕或污染. 3.鉚接件相互接觸的表面, 在聯(lián)接前必須涂厚度30-40μm防銹漆.由于加工或焊接損壞的底漆, 要重新涂裝. 4.不封閉的箱形結(jié)構(gòu)內(nèi)表面, 在組焊前必須涂厚度60-80μm防銹漆, 封閉的箱體結(jié)構(gòu)件內(nèi)表面 不涂漆 . 5.溜槽、漏斗、裙板內(nèi)表面、平衡的重箱內(nèi)表面、安全罩內(nèi)表面、封閉箱且在運輸過程中是敞開 的內(nèi)表面等,必須涂厚度60-80μm防銹漆. 6.涂層的檢查項目及方法應符合本標準的規(guī)定. 5、切削加工件通用技術(shù)要求(JB/ZQ4000.2-86) 1.鑄鋼件加工后,如發(fā)現(xiàn)有砂眼
15、、縮孔、夾渣、裂縫等缺陷時,在不降低零件強度和使用性能的情況下, 按照鑄鋼件 補焊通用技術(shù)條件(JB/ZQ4000.6-86)的規(guī)定補焊,并經(jīng)檢驗合格. 2.長度尺寸、圓角半徑和倒角高度的未注公差見下表: 長度尺寸未注公差 mm 公稱尺寸 加工方法 切削加工 冷作成形 0.5-3(≤) 0.1 0.15 3-6 0.1 0.2 6-30 0.2 0.5 30-120 0.3 0.8 120-400 0.5 1.2 400-1000 0.8 2 1000-2000 1.2 3 2000-4000 2 4 4000-8000 3
16、 5 8000-12000 4 6 12000-16000 5 7 16000-20000 6 8 圓角半徑、倒角高度未注公差 mm 公稱尺寸 加工方法 切削加工 冷作成形 0.5-3(≤) 0.2 0.2 3-6 0.5 1 6-30 1 2 30-120 2 4 120-400 4 8 角度未注公差 mm 短邊公稱尺寸 加 工 方 法 切削加工 正切值 冷作成形 正切值 10(≤) 1 0.0175 130′ 0.0262 10-50 30′ 0.0087 50′ 0.0145 50-120
17、20′ 0.0058 25′ 0.0073 120-400 10′ 0.0029 15′ 0.0044 >400 5′ 0.0015 10′ 0.0029 3.未注形狀公差應符合(GB1184-80)的要求,其中直線度,平面度不得低于該標準中規(guī)定的C級精度, 平行度未注公差 應符合(GB1184-80)中第5條規(guī)定,垂直度和傾斜度未注公差,不得大于上表規(guī)定的角度公差; 同軸度、對稱度不得 大于GB1184-80表2規(guī)定的C級; 徑向跳動和端面跳動應符合GB1184-80中第7條的規(guī)定. 6、裝配通用技術(shù)條件(JB/ZQ4000.9-86) 1.外
18、購材料與零部件應具有JB/ZQ4000.1-86<產(chǎn)品檢驗通用技術(shù)要求>中規(guī)定的檢驗報告與合格證. 2.用于緊固機架,機座和壓力容器壓緊法蘭的緊固件,在緊固后,螺釘或螺母的端面與被緊固零件間的傾斜不得大于1. 3.螺栓與螺母擰緊后,螺栓應露出螺母 2-4扣,不許露出過長或過短. 4.各種密封氈圈、氈墊、石棉繩、皮碗等密封件裝配前必須浸透油.鋼紙板用熱水泡軟,紫銅墊作退火處理(加熱至600-650℃ 后在水中冷卻). 5.d>4mm圓錐銷與孔應進行著色檢查,其接觸率不得低于 50%.帶螺尾圓錐銷打入后,大端須沉入相關(guān)件2-3扣. 6.鉤頭鍵與楔鍵裝配后,工作面上的
19、接觸率應在70%以上 ,其不接觸部分不得集中于一段. 裝配后外露尺寸應為斜面長度的 10-15%(不包括鉤頭). 7.花鍵或齒形離合器的裝配, 單齒分度加工的矩形花鍵或齒形離合器的工作面研合后,同時接觸的齒數(shù)不得少于 2/3;接觸 率在齒長和齒高方向上均不得低于50%,研合時可用0.05mm的塞尺檢查齒側(cè)隙,塞尺不得插入全齒長. 8.錐軸伸與軸孔配合表面接觸應均勻, 著色研合檢驗時其接觸率不得低于70%. 9.各類聯(lián)軸器技術(shù)要求及軸向(△X)、徑向(△Y)與角向(△α)的許用補償量,應符合有關(guān)聯(lián)軸器標準的規(guī)定. 10.軸承外圈與開式箱體或軸承座的各半圓孔間不準有"夾
20、幫"現(xiàn)象,各半圓孔的"修幫"尺寸,不準超過下表規(guī)定的最大值. 滾動軸承裝配修幫尺寸 mm 軸承外徑D bmax hmax ≤120 0.10 10 120-260 0.15 15 260-400 0.20 20 >400 0.25 30 11.采用潤滑脂的軸承,裝配后在軸承空腔內(nèi)注入相當空腔容積65-80%的清潔潤滑脂. 12.軸承裝在軸上后應靠緊軸肩,軸承內(nèi)圈在常溫狀態(tài)經(jīng)打擊沒有串動現(xiàn)象的情況下,圓錐滾子軸承和向心推力球軸承 與軸肩的間隙不得大于0.05mm.其它軸承不得大于0.10mm. 13.裝配滾動軸承允許采用機油加熱進行熱裝,油的溫度不
21、得超過100℃. 14.在軸兩端采用了徑向間隙不可調(diào)的向心軸承(或滾針軸承、螺旋滾子軸承等), 而且軸的軸向位移又是以兩端端蓋限 定時,必須留出間隙 C.如果沒規(guī)定C的數(shù)值,通常可按 C=0.2-0.4mm規(guī)定,當溫差 變化較大或兩軸承中心距較大時,間隙 C的數(shù)值可按下式 計算: C=Lα△t+0.15 式中:C─ 軸承外座圈與端蓋間的間隙,mm. L─ 兩軸承中心距,mm. α─ 軸材料的線膨脹系數(shù)(取α=1210^(-6) △t─ 軸工作時溫度與環(huán)境溫度之差,℃ . 0.15─ 軸膨脹后剩余的間隙 ,mm. 15.單列圓錐滾子軸承、向心推力球軸承、雙向推力球軸
22、承向游隙按(表1)調(diào)整.雙列和四列圓錐滾子軸承在裝配時 均應檢查其軸向游隙,并應符合(表2)的要求. 表1 : mm 軸承內(nèi)徑 向心推力球軸承向游隙 單列圓錐滾子軸承向游隙 雙列推力球軸承向游隙 輕系列 中及重系列 輕系列 輕寬.中及中寬系列 輕系列 中及重系列 ≤30 0.02-0.06 0.03-0.09 0.03-0.10 0.04-0.11 0.03-0.08 0.05-0.11 30-50 0.03-0.09 0.04-0.10 0.04-0.11 0.05-0.13 0.04-0.10 0.06-0.12 50-80 0.04
23、-0.10 0.05-0.12 0.05-0.13 0.06-0.15 0.05-0.12 0.07-0.14 80-120 0.05-0.12 0.06-0.15 0.06-0.15 0.07-0.18 0.06-0.15 0.10-0.18 120-150 0.06-0.15 0.07-0.18 0.07-0.18 0.08-0.20 - - 150-180 0.07-0.18 0.08-0.20 0.09-0.20 0.10-0.22 - - 180-200 0.09-0.20 0.10-0.22 0.12-0.22 0.14
24、-0.24 - - >200-250 - - 0.18-0.30 0.18-0.30 - - 表2: 雙列、四列圓錐滾子軸承的軸向游隙 mm 雙列圓錐滾子軸承內(nèi)徑 軸 向 游 隙 一般情況 內(nèi)圈比外圈溫度高 25-30℃ ≤80 0.10-0.20 0.30-0.40 80-180 0.15-0.25 0.40-0.50 180-225 0.20-0.30 0.50-0.60 225-315 0.30-0.40 0.70-0.80 315-560 0.40-0.50 0.90-1.00 四列圓錐滾子 軸 承 內(nèi) 徑 軸向游隙
25、 120-180 0.15-0.25 180-315 0.20-0.30 315-400 0.25-0.35 400-500 0.30-0.40 500-630 0.30-0.40 630-800 0.35-0.45 800-1000 0.35-0.45 1000-1250 0.40-0.50 16.滑動軸承上、下軸瓦的接合面要接觸良好,無螺釘把緊的軸瓦接合面,用0.05mm和塞尺從外側(cè)檢查,在各處的塞入深度, 都不得大于接合面的1/3. 17.上、下軸瓦裝配后其外圓應與相關(guān)軸承孔良好接觸,如果圖樣或相關(guān)設(shè)計文件對接觸率未作具體規(guī)定時,應按下表的規(guī)
26、 定執(zhí)行. 上下軸瓦外圓與相關(guān)軸承孔的接觸要求 項目 接觸要求 上瓦 下瓦 接觸角α:稀油潤滑 130 150 接觸角α:油脂潤滑 120 140 α角內(nèi)接觸率 60% 70% 瓦側(cè)間隙 b,mm D≤200時,0.05mm塞尺不準塞入 D>200時,0.10mm塞尺不準塞入 18.軸瓦內(nèi)孔刮研后,應與相關(guān)軸頸接觸良好, 如圖樣或相關(guān)設(shè)計文件未作具體規(guī)定時,則按下表的規(guī)定執(zhí)行. 上下軸瓦內(nèi)孔與相關(guān)軸頸的接觸要求 接觸角α α角范圍內(nèi)接觸點,點數(shù)/2525mm^2 稀油潤滑 油脂潤滑 軸轉(zhuǎn)速r/min 軸瓦內(nèi)徑,mm ≤180 180
27、-360 360-500 ≤300 4 3 2 300-500 5 4 3 120 90 500-1000 6 5 4 >1000 8 6 5 注:受力較小的軸瓦、接觸點可在2525mm^2的面積上,按表中數(shù)值降低1個接觸點. 19.上、下軸瓦接觸角α以外的部分均需刮出油楔(如下表所示C1),楔形從瓦口開始由最大逐步過渡到零,楔形最大值按下 表中規(guī)定. 上、下軸瓦經(jīng)刮研達要求并組裝后,軸瓦內(nèi)徑與軸頂部處的間隙值C應達到圖樣配合公差的中間值或接近上 限值. 上下軸瓦油楔尺寸:(油楔最大值C1) 稀油潤滑 C1≈C 油脂潤滑 距瓦兩端面10
28、-15mm范圍內(nèi),C1≈C 中間部位 C1≈2C. 注:C值為軸瓦的最大配合間隙. 20.軸瓦中裝固定銷用的通孔,應在瓦口面與相關(guān)軸承孔的開合面保持平齊的情況下, 與其配鉆鉸. 固定銷打入后,應與銷 孔緊密配合, 不得有松動現(xiàn)象,銷子的端面應低于軸瓦內(nèi)孔2-3mm. 21.過盈配合零件在裝配前必須對配合部位進行復檢, 并做好記錄.過盈量應符合圖樣或工藝文件的規(guī)定;與軸肩相靠的 相頭輪或環(huán)的端面,以及作為裝配基準的輪緣端面,與孔的垂直度偏差應在圖樣規(guī)定的范圍內(nèi). 22.壓裝的軸和套允許在引入端制作導錐, 導錐的長度不準超過配合部位長度的15%,錐度各工廠自定. 23
29、.采用壓力機壓裝時,應做好壓力變化的記錄,壓力變化應當平穩(wěn),出現(xiàn)異常時就進行分析,不準有壓壞零件配合表面的 現(xiàn)象. 圖樣有最大壓入力的要求時,應達到規(guī)定數(shù)值,不準過大或過小. 24.壓裝完成后,在軸肩處必須靠緊,間隙不得大于0.10mm. 25.熱裝薄環(huán)或輪緣時,在端面處應設(shè)置可靠的定位基準.熱裝后軸與環(huán)或輪轂與輪緣之間的中心不準出現(xiàn)互相偏斜現(xiàn)象. 26.除鑄鐵輪轂與鋼制輪緣在熱裝后可向輪轂內(nèi)壁均勻澆冷水外,其余熱裝零件均應自然冷卻,不準急冷. 27.零件熱裝時,必須靠緊軸肩或其它相關(guān)端面.零件經(jīng)過冷縮后, 零件與軸肩或其它相關(guān)端面的間隙在圖樣未做規(guī)定時, 不得大于
30、配合長度尺寸的1/1000. 28.主動鏈輪和被動鏈輪齒的中心線應當重合. 其偏移誤碼差不得大于兩鏈輪中心距2/1000. 29.鏈條非工作邊的下垂度,在圖樣沒有具體規(guī)定時,按兩鏈輪中心距的1-4.5%的規(guī)定. 30.相關(guān)的兩個平面需要互研時, 只能在兩個平面各自按平板或平尺刮研接近合格后,方準兩件互研.被刮研表面接觸點 在圖樣或相關(guān)設(shè)計文件無具體規(guī)定或以精磨代替刮研時,應符合下表規(guī)定. 一般情況下的平面刮研接觸點 滑動速度 接觸面積,m^2 ≤0.20 >0.20 m/s 點數(shù)/2525mm^2 ≤0.50 3 4 0.50-1.50 4 3
31、 31.下列回轉(zhuǎn)零件必須做靜平衡試驗: 1).圖樣已給出不平衡力矩限值的零件; 2).對于沒有注明靜平衡試驗的回轉(zhuǎn)零件,當Q.nmax>25時均需進行靜平衡試驗.式中Q為回轉(zhuǎn)零件的質(zhì)量,t;nmax為回 轉(zhuǎn)零件的最大轉(zhuǎn)速,r/min.當 nmax≤20r/min的以及鍛造的全加工、全對稱的回轉(zhuǎn)零件不作靜平衡試驗. 32.對于需要作平衡試驗,但未規(guī)定平衡精度時,按 JB/ZZ4-86<<剛體轉(zhuǎn)動件的平衡>>規(guī)定的平衡精度G18執(zhí)行. 33.所有鑄造液壓缸體等容器,如試壓工序是安排在粗加工后進行的,而在精加工后表面又出現(xiàn)了氣孔、裂紋、夾渣等缺陷 時,則必須重新進行試壓.
32、 34.所有鋼板焊接的液壓罐等容器,焊后應進行試壓, 焊縫處經(jīng)過切削加工時,則要重新試壓. 35.鍛造或鍛焊結(jié)構(gòu)的液壓缸等,要采用外觀、超聲波探傷、液壓試驗等方法,對承壓的可靠性進行檢驗. 36.探傷表面粗糙度應達到Ra3.2μm. 37.承壓母體試壓與裝配后的密封試壓,如無特殊規(guī)定試驗壓力,一般為工作壓力的1.5倍. 38.零件母體承壓可靠性的試壓,保壓15min(允許補壓),母體各部不準有滲漏現(xiàn)象. 39.裝配件密封性試壓,保壓2min,不降壓,且各密封處不準有滲漏現(xiàn)象. 40.固定在機體上的管路,應按照JB/ZQ4000.8-86<<管道與容器焊接防銹通用技術(shù)要求>>的規(guī)定,進行清洗與防銹處理.
- 溫馨提示:
1: 本站所有資源如無特殊說明,都需要本地電腦安裝OFFICE2007和PDF閱讀器。圖紙軟件為CAD,CAXA,PROE,UG,SolidWorks等.壓縮文件請下載最新的WinRAR軟件解壓。
2: 本站的文檔不包含任何第三方提供的附件圖紙等,如果需要附件,請聯(lián)系上傳者。文件的所有權(quán)益歸上傳用戶所有。
3.本站RAR壓縮包中若帶圖紙,網(wǎng)頁內(nèi)容里面會有圖紙預覽,若沒有圖紙預覽就沒有圖紙。
4. 未經(jīng)權(quán)益所有人同意不得將文件中的內(nèi)容挪作商業(yè)或盈利用途。
5. 裝配圖網(wǎng)僅提供信息存儲空間,僅對用戶上傳內(nèi)容的表現(xiàn)方式做保護處理,對用戶上傳分享的文檔內(nèi)容本身不做任何修改或編輯,并不能對任何下載內(nèi)容負責。
6. 下載文件中如有侵權(quán)或不適當內(nèi)容,請與我們聯(lián)系,我們立即糾正。
7. 本站不保證下載資源的準確性、安全性和完整性, 同時也不承擔用戶因使用這些下載資源對自己和他人造成任何形式的傷害或損失。
最新文檔
- 2023年六年級數(shù)學下冊6整理和復習2圖形與幾何第7課時圖形的位置練習課件新人教版
- 2023年六年級數(shù)學下冊6整理和復習2圖形與幾何第1課時圖形的認識與測量1平面圖形的認識練習課件新人教版
- 2023年六年級數(shù)學下冊6整理和復習1數(shù)與代數(shù)第10課時比和比例2作業(yè)課件新人教版
- 2023年六年級數(shù)學下冊4比例1比例的意義和基本性質(zhì)第3課時解比例練習課件新人教版
- 2023年六年級數(shù)學下冊3圓柱與圓錐1圓柱第7課時圓柱的體積3作業(yè)課件新人教版
- 2023年六年級數(shù)學下冊3圓柱與圓錐1圓柱第1節(jié)圓柱的認識作業(yè)課件新人教版
- 2023年六年級數(shù)學下冊2百分數(shù)(二)第1節(jié)折扣和成數(shù)作業(yè)課件新人教版
- 2023年六年級數(shù)學下冊1負數(shù)第1課時負數(shù)的初步認識作業(yè)課件新人教版
- 2023年六年級數(shù)學上冊期末復習考前模擬期末模擬訓練二作業(yè)課件蘇教版
- 2023年六年級數(shù)學上冊期末豐收園作業(yè)課件蘇教版
- 2023年六年級數(shù)學上冊易錯清單十二課件新人教版
- 標準工時講義
- 2021年一年級語文上冊第六單元知識要點習題課件新人教版
- 2022春一年級語文下冊課文5識字測評習題課件新人教版
- 2023年六年級數(shù)學下冊6整理和復習4數(shù)學思考第1課時數(shù)學思考1練習課件新人教版