離合器齒輪零件的機(jī)械加工工藝規(guī)程
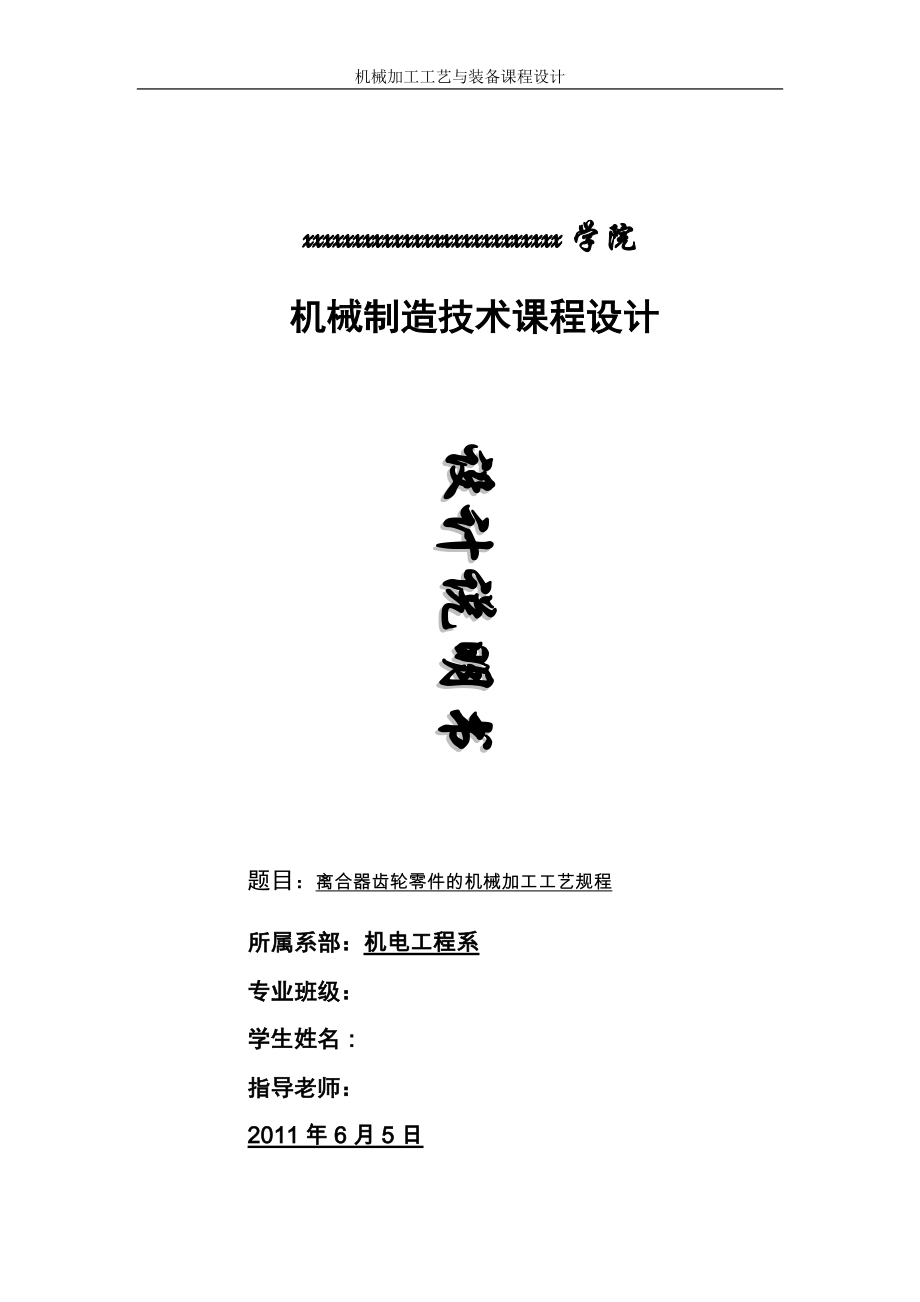


《離合器齒輪零件的機(jī)械加工工藝規(guī)程》由會(huì)員分享,可在線閱讀,更多相關(guān)《離合器齒輪零件的機(jī)械加工工藝規(guī)程(18頁珍藏版)》請(qǐng)?jiān)谘b配圖網(wǎng)上搜索。
1、機(jī)械加工工藝與裝備課程設(shè)計(jì) xxxxxxxxxxxxxxxxxxxxxxxxxx學(xué)院 機(jī)械制造技術(shù)課程設(shè)計(jì) 設(shè)計(jì)說明書 題目:離合器齒輪零件的機(jī)械加工工藝規(guī)程 所屬系部:機(jī)電工程系 專業(yè)班級(jí): 學(xué)生姓名: 指導(dǎo)老師: 2011年6月5日 17 目 錄 1 前言 1 2 零件的工藝分析及生產(chǎn)類型的確定 1 2.1 零件的作用 1 2.2 零件的工藝性分析 1 2.3 零件的生產(chǎn)類型 2 3 選擇毛坯,確定毛坯尺寸,設(shè)計(jì)毛坯-零件合圖 2 3.1 選擇毛坯 2 3.2 確定機(jī)械加工余量、毛坯尺寸和公差 2 3.3 確定機(jī)械加工
2、余量 3 3.4 確定毛坯尺寸 3 3.5 確定毛坯尺寸公差 3 3.6 繪制毛坯圖 4 4 選擇加工方法,制定工藝路線 5 4.1 定位基準(zhǔn)的選擇 5 4.2 零件表面加工方法的選擇 5 4.3 制訂工藝路線 5 5 工序設(shè)計(jì) 6 5.1 選擇加工設(shè)備與工藝裝備 6 5.2 確定工序尺寸 7 6 確定切削用量及基本時(shí)間 8 6.1 工序Ⅰ切削用量及基本時(shí)間的確定 8 6.2 工序第Ⅰ、第Ⅱ、第Ⅵ、第Ⅷ切削用量及基本時(shí)間的確定 13 7 夾具設(shè)計(jì) 13 7.1 夾具的定位方案 13 7.2 夾緊機(jī)構(gòu) 13 7.3 誤差分析 13
3、7.4 夾緊力的計(jì)算 15 8 小結(jié) 16 9 參考文獻(xiàn) 16 1 前言 機(jī)械加工工藝與裝備課程設(shè)計(jì)是我學(xué)完了大學(xué)的全部基礎(chǔ)課、專業(yè)技術(shù)基礎(chǔ)課以及大部分專業(yè)課之后進(jìn)行的。這是我在進(jìn)行畢業(yè)設(shè)計(jì)之前對(duì)所學(xué)各課程的一次深入的綜合性的總復(fù)習(xí),也是一次理論聯(lián)系實(shí)際的訓(xùn)練。因此,它在我的大學(xué)生活中占有重要的地位。 就我個(gè)人而言,我希望能通過這次課程設(shè)計(jì)對(duì)自己未來將從事的工作進(jìn)行一次適應(yīng)性訓(xùn)練,從中鍛煉自己分析問題、解決問題的能力,為今后參加工作打下一個(gè)良好的基礎(chǔ)。 由于能力所限,設(shè)計(jì)尚有許多不足之處,懇請(qǐng)各位老師給予指導(dǎo)。 2 零件的工藝分析及生產(chǎn)類型的確定 2.1 零件的作
4、用 題目所給定的零件是車床主軸箱中運(yùn)動(dòng)輸入軸Ⅰ軸上的一個(gè)離合器齒輪。它用于接通或斷開主軸的反轉(zhuǎn)傳動(dòng)路線,與其他零件一起組成摩擦片正反轉(zhuǎn)離合器,如圖7-2(M1右側(cè))所示。主運(yùn)動(dòng)傳動(dòng)鏈由電機(jī)經(jīng)過帶輪傳動(dòng)副φ130mm/φ230mm傳至主軸箱中的軸Ⅰ。在軸Ⅰ上裝有雙向多片摩擦離合器M1,使主軸正轉(zhuǎn)、反轉(zhuǎn)或停止。當(dāng)壓緊離合器左部的摩擦片時(shí),軸Ⅰ的運(yùn)動(dòng)經(jīng)齒輪副56/38或51/43傳給軸Ⅱ,使軸Ⅱ獲得2種轉(zhuǎn)速。壓緊右部摩擦片時(shí),經(jīng)齒輪50、軸Ⅶ上的空套齒輪34傳給軸Ⅱ上的固定齒輪30。這時(shí)軸Ⅰ至軸Ⅱ間多一個(gè)中間齒輪34,故軸Ⅱ的轉(zhuǎn)向相反,反轉(zhuǎn)轉(zhuǎn)速只有1種。當(dāng)離合器處于中間位置時(shí),左、右摩擦片都沒有被
5、壓緊,軸Ⅰ運(yùn)動(dòng)不能傳至軸Ⅱ,主軸停轉(zhuǎn)。此零件借助兩個(gè)滾動(dòng)軸承空套在Ⅰ軸上,只有當(dāng)裝在Ⅰ軸上的內(nèi)摩擦片和裝在該齒輪上的外摩擦片壓緊時(shí),Ⅰ軸才能帶動(dòng)該齒輪轉(zhuǎn)動(dòng)。該零件φ68K7mm的孔與兩個(gè)滾動(dòng)軸承的外圈相配合,φ71mm溝槽為彈簧擋圈卡槽,φ94mm的孔容納內(nèi)、外摩擦片,4~16mm槽口與外摩擦片的翅片相配合使其和該齒輪一起轉(zhuǎn)動(dòng),61.5mm溝槽和4φ5mm的孔用于通入冷卻潤(rùn)滑油。 2.2 零件的工藝性分析 1、左端 φ68K7 外圓表面精度等級(jí)為IT7,表面粗糙度為Ra0.8。并且槽相對(duì)φ68K7 孔的軸線成90度均勻分布。 2、16 mm寬槽口相對(duì)φ68K7孔的軸線成90均勻分布,其
6、徑向設(shè)計(jì)基準(zhǔn)是φ68K7 mm孔的軸線,軸向設(shè)計(jì)基準(zhǔn)是φ106.5 mm外圓柱的左端平面。 3、4φ5 mm孔在61.5 mm溝槽內(nèi),孔中心線距溝槽一側(cè)面的距離為3 mm,圓錐角度為90度。4個(gè)φ5 mm孔分別與16mm槽寬錯(cuò)開45度均勻分布。 4、由于加工時(shí)不能選用溝槽的側(cè)面為定位基準(zhǔn),故要精確地保證上述要求比較困難,但這些小孔為油孔,位置要求不高,只要鉆到溝槽之內(nèi)接通油路就可,加工不難。 5、Φ90外圓表面精度等級(jí)為IT14,表面粗糙度為Ra3.2。 6、左端外圓表面φ106.5 精度等級(jí)為IT12,表面粗糙度為Ra6.3。 7、φ94外圓表面精度等級(jí)為IT14,表面粗糙度為Ra
7、6.3。 8、φ71內(nèi)孔槽內(nèi)圓表面精度等級(jí)為IT14,表面粗糙度為Ra6.3。 9、φ117h11齡輪外圓表面 IT11 Ra3.2,齒面Ra1.6。 10、右端面Ra3.2,左端面Ra6.3。 11、倒(圓)角。 2.3 零件的生產(chǎn)類型 根據(jù)設(shè)計(jì)題目可知:Q=2000臺(tái)/年,n=1件/臺(tái);結(jié)合生產(chǎn)實(shí)際,備品率a和廢品率b分別取為5%和2%。代入公式(4-1)得該零件的生產(chǎn)綱領(lǐng): N=20001(1+5%)(1+2%)=2142件/年 零件是機(jī)床上的齒輪,質(zhì)量為1.36kg,查表4-2可知其屬輕型零件,生產(chǎn)類型為中批量生產(chǎn)。 3 選擇毛坯,確定毛坯尺寸,設(shè)計(jì)毛坯-
8、零件合圖 3.1 選擇毛坯 該零件材料為45鋼,而且屬于薄壁的圓盤類中小型零件,考慮加工工序較多,會(huì)經(jīng)常承受交變載荷及沖擊載荷,因此應(yīng)該選用鍛件,可得到連續(xù)和均勻的金屬纖維組織,保證零件工作可靠。又由于零件年產(chǎn)量為2142件,屬中批量生產(chǎn),而且零件的輪廓尺寸不大,故可采用模鍛成形,可獲得較好的尺寸精度和較高的生產(chǎn)率。 3.2 確定機(jī)械加工余量、毛坯尺寸和公差 查《金屬機(jī)械加工工藝人員手冊(cè)》,可知鋼質(zhì)模鍛的公差及機(jī)械加工余量按GB/T12362—2003確定。要確定毛坯的尺寸公差及機(jī)械加工余量,先確定如下參數(shù)。 (1)鍛件公差等級(jí)。由該零件的功用和技術(shù)要求,確定其鍛件公差等級(jí)為普通
9、級(jí)。 (2)鍛件質(zhì)量m。根據(jù)零件成品質(zhì)量1.36kg,估算為mf=2.5kg。 由于該零件為圓形,假設(shè)其最大直徑為φ121mm,長(zhǎng)為68mm,則由圓形鍛件計(jì)算質(zhì)量公式mN= ( 為鋼材密度,7.85g/cm3)可知:鍛件外廓包容體質(zhì)量 mN= 121268 7.8510?6=6.135kg。 所以, S=mf/mN=2.5/6.135=0.407。 由于0.407介于0.32和0.63之間,故該零件的形狀復(fù)雜系數(shù)S屬S2級(jí)。 (4)零件表面粗糙度。由零件圖知,除φ68K7mm孔為Ra0.8以外,其余各加工表面為Ra≥1.6。 3.3 確定機(jī)械加工余量 根據(jù)鍛件質(zhì)量、零件表面
10、粗糙度、形狀復(fù)雜系數(shù)查《金屬機(jī)械加工工藝人員手冊(cè)》中鍛件內(nèi)外表面加工余量表,查得單邊余量在厚度方向?yàn)?.7~2.2mm,水平方向?yàn)?.7~2.2mm。鍛件中心兩孔的單面余量按手冊(cè)中鍛件內(nèi)孔直徑的單面機(jī)械加工余量表,可查得為2.5mm。 3.4 確定毛坯尺寸 根據(jù)查得的加工余量適當(dāng)選擇稍大點(diǎn)即可,只有φ68K7mm孔,因?yàn)楸砻娲植诙纫筮_(dá)到Ra0.8,考慮磨削孔前的余量要大,可確定精鏜孔單面余量為0.5mm。其他槽、孔隨所在平面鍛造成實(shí)體。具體加工余量的選擇大小如表7-1所示。 3.5 確定毛坯尺寸公差 毛坯尺寸公差根據(jù)鍛件質(zhì)量、材質(zhì)系數(shù)、形狀復(fù)雜系數(shù)從手冊(cè)中查鍛件的長(zhǎng)度、寬度、高度
11、、厚度公差表可得。具體如表7-1所示。 表7-1 零件尺寸 單面加工余量 鍛件尺寸 偏差 117H11 2 121 106.5 1.75 110 94 2 89 90 2 94 68K7 3 62 64 2 68 94孔深31mm 1.8 29.2 20 1 21 12 1.8 13.8 3.6 繪制毛坯圖 根據(jù)確定的毛坯尺寸和加工余量,可繪制毛坯-零件合圖,外圓角半徑為R6,內(nèi)圓角半徑為R3;內(nèi)、外模鍛斜度分別為7、5。如圖3所示。
12、 4 選擇加工方法,制定工藝路線 4.1 定位基準(zhǔn)的選擇 本零件是帶圓盤狀齒輪,孔是其設(shè)計(jì)基準(zhǔn)(亦是裝配基準(zhǔn)和測(cè)量基準(zhǔn)),為避免由于基準(zhǔn)不重合而產(chǎn)生的誤差,應(yīng)選孔為定位基準(zhǔn),即遵循“基準(zhǔn)重合”的原則,即精基準(zhǔn)選φ68K7mm的孔及其端面。 由于離合器齒輪所有表面都要加工,而孔作為精基準(zhǔn)應(yīng)先進(jìn)行加工,因此應(yīng)選φ94外圓及其端面為粗基準(zhǔn)。但因?yàn)橥鈭Aφ121mm上有分模面,表面不平整,有飛邊等缺陷,定位不可靠,故不能選為粗基準(zhǔn)。 4.2 零件表面加工方法的選擇 該零件的主要加工表面有外圓、內(nèi)孔、端面、齒面、槽及孔,其加工方法選擇如表2所示。 表2 位
13、置 公差等級(jí) 粗糙度(Ra/um) 加工方法 90 IT14 3.2 粗車—半精車 117h11 IT11 3.2 粗車—半精車 106.5 IT12 6.3 粗車—半精車 68K7 IT7 0.8 粗鏜—半精鏜—精鏜 94 IT14 6.3 粗鏜 端面 IT14 6.3 粗車 齒面 IT11 3.2 粗車—半精車 槽 IT13 3.2 粗銑—半精銑 5小孔 IT14 鉆 4.3 制訂工藝路線 齒輪的加工工藝路線一般是先進(jìn)行齒坯的加工,再進(jìn)行齒面加工。齒坯加工包括各圓柱表面及端面的加工。按照先基準(zhǔn)及先粗后精
14、的原則,該零件加工工藝路線如表3所示。 表3 序號(hào) 工序內(nèi)容 設(shè)備 1 粗車右端φ117和φ90外圓及其端面,粗鏜右端φ68孔內(nèi)表面和φ71圓槽內(nèi)表面。 C620-1型臥式車床 2 掉頭粗車左端φ106.5及端面,粗鏜左端φ94內(nèi)孔表面 C620-1型臥式車床 3 半精車右端φ117和φ90外圓及其端面,半精鏜右端φ68內(nèi)孔表面和φ71圓槽內(nèi)表面。倒右端的角(圓角)。 C620-1型臥式車床 4 掉頭半精車左端φ106.5及臺(tái)階面,半精鏜左端φ94內(nèi)孔表面,倒左端的角(圓角)。 C620-1型臥式車床 5 滾齒輪。 Y3150型滾齒機(jī) 6 鉆φ5孔,锪
15、沉頭孔。 Z525型立式鉆床 7 精鏜φ68內(nèi)孔表面 C620-1型臥式車床 8 銑槽 X62W臥式銑床 9 鉗工去毛刺 10 終檢 5 工序設(shè)計(jì) 5.1 選擇加工設(shè)備與工藝裝備 根據(jù)不同的工序選擇機(jī)床、刀具、檢驗(yàn)量具,如下表所示。 工步 設(shè)備選擇 刀具選擇 量具選擇 粗車 C620-1車床 YT15 游標(biāo)卡尺 半精車 C620-1車床 YT30 游標(biāo)卡尺 粗鏜 C620-1車床 YT15 內(nèi)徑千分尺 半精鏜 C620-1車床 YT30 內(nèi)徑千分尺 滾齒 Y3150滾齒機(jī) A級(jí)單頭滾刀 公法線千分尺
16、銑槽 X62W臥式銑床 160mm三面刃銑刀 游標(biāo)卡尺 鉆孔 Z525立式鉆床 復(fù)合鉆 機(jī)床的選擇 工序3、4、6、7,粗車和半精車又或者粗鏜和半精鏜。 各工序的加工步數(shù)不多,且不要求很高的生產(chǎn)率,精度要求不高,選用C620-1型臥式車床 滾齒 先用Y3150型滾齒機(jī)較合適 三面刃銑刀粗銑及精銑槽。用專用夾具加工,選用X62W臥式銑床 鉆5小孔 采用專用分度夾具在立式鉆床上加工 選用Z525型立式鉆床 刀具的選擇 加工鋼質(zhì)零件采用YT類硬質(zhì)后金。粗加工用YT15,精加工用YT30。選用轉(zhuǎn)位車刀。切槽刀宜用高速鋼。 滾齒采用A級(jí)單頭滾刀達(dá)8級(jí)精度,選模
17、數(shù)為2.25mm. 銑刀選用三面刃銑刀,銑刀直徑為160mm。 鉆小孔用復(fù)合鉆一次鉆出。 量具的選擇 外圓表面的測(cè)量中,除117的尺寸公差為0.22最小要用到外徑千分尺外,其它均可用游標(biāo)卡尺 68K7 內(nèi)徑百分表 精鏜67K7孔時(shí),用三牙鎖緊式圓柱塞規(guī) 軸向游標(biāo)卡尺 5.2 確定工序尺寸 (1)確定圓柱面的工序尺寸。圓柱表面多次加工的工序尺寸只與加工余量有關(guān)。前面已確定各圓柱面的總加工余量(毛坯余量),應(yīng)將毛坯余量分為各工序加工余量,然后由后往前計(jì)算工序尺寸。中間工序尺寸的公差按加工方法的經(jīng)濟(jì)精度確定。 該零件各圓柱表面的工序加工余量、工序尺寸及公差、表面
18、粗糙度如 書中表7-5所示。 加工面 工序 余量 精度等級(jí) 工序尺寸 工序尺寸公差 117H11齒面 粗車 2.5 IT11 118.5 0 -0.220 半精車 1.5 IT9 117 0 -0.087 106.5外圓 粗車 3.5 IT11 108 0 -0.220 半精車 1.5 IT9 106.5 0 -0.087 90外圓 粗車 2.5 IT11 91.5 0 -0.220 半精車 1.5 IT9 90 0 -0.087 94孔 粗鏜 2.5 IT11 94 68K7孔
19、 粗鏜 3 IT11 70 +0.190 0 半精鏜 2 IT9 69 +0.074 0 精鏜 1 IT7 68 +0.030 0 6 確定切削用量及基本時(shí)間 切削用量包括背吃刀量ap、進(jìn)給量f、和切削速度Vc。確定順序是先確定ap、f再確定Vc。 6.1 工序Ⅰ切削用量及基本時(shí)間的確定 本工序?yàn)榇周嚕ㄜ嚩嗣?、外圓及鏜孔)。已知加工材料為45鋼,鍛件,有外皮;機(jī)床為CA6140臥式車床,工件裝卡在三爪自定心卡盤中。 切削用量包括背吃刀量a進(jìn)給量f和切削速度v。 1、 工序Ⅰ切削用量及基本時(shí)間的確定 ⑴切削用量 本工序?yàn)榇周嚕ㄜ嚩?/p>
20、面、外圓及鏜孔)。己知加工材料為45鋼。 1) 確定粗車外圓Ф118.5的切削用量。選用刀的刀杠尺寸BH=16mm25mm, ①確定背吃刀量a,粗些車雙邊余量為2.5mm,顯然a為單邊余量:a==1.25mm ②確定進(jìn)給量f ,根據(jù)背吃力量a<=3mm, 工件的直徑為100-400mm時(shí),查表書本附表1得:f=0.60mm/r ③確定切削速度v。粗車速度取n=130r/min,根據(jù)公式 得=45.5m/min 45號(hào)鋼為 優(yōu)質(zhì)碳素結(jié)構(gòu)用鋼,根據(jù)GB/T699-1999標(biāo)準(zhǔn)規(guī)定45鋼抗拉強(qiáng)度為600MPa,當(dāng)加工600-700Mpa鋼料、a<=3mm、f<=0.75mm/r時(shí),切削速
21、度v=109m/min。 確定的切削用量為:a=1.25mm,f=0.60mm/r,n=130r/min,v=45.5m/min。 車削時(shí)間: =25s L為車削路程33mm. 2)確定粗車外圓Ф91.5mm 、端面及臺(tái)階面的切削用量。采用車外圓Ф118.5的刀具加工這些表面。車外圓車外圓Ф91.5mm的a=1.25mm,端面及臺(tái)階面的a=1.3mm.車外圓Ф91.5mm的f=0.60mm/r,車端面及臺(tái)階面的f=0.52mm/r。主軸轉(zhuǎn)速與車外圓Ф118.5mm相同。 切削速度: =37.35m/min =0.623m/s 粗車φ91.5時(shí)間: =15.4s 3
22、)確定粗鏜Ф65mm孔的切削用量。所用刀具為YT5硬質(zhì)合金、直徑為20mm的圓形鏜刀。 ①.確定背吃力量a,雙邊余量為3mm,顯然a為單邊余量: a==1.5mm ②.確定進(jìn)給量f 根據(jù)表得,當(dāng)粗鏜料、鏜刀直徑為20mm、a<=2mm、鏜刀出長(zhǎng)度為100mm時(shí),f=0.15-0.3mm/r按C620-1車床的進(jìn)給量,選擇 f=0.2mm/r ③確定切削速度v,根據(jù)公式:V= 查表得系數(shù)為:=291,m=2,=0.15,=0.2T=60min,=0.90.80.65=0.568, 所以V= 經(jīng)查C620-1車床的轉(zhuǎn)速,選擇=370r/min。 確定粗鏜孔的基本時(shí)間,選鏜
23、刀的主偏角。 其中,,,,,,,。所以: 確定粗車端面的基本時(shí)間: 式中,,,,,,,, 所以: 4)確定粗車臺(tái)階面的基本時(shí)間: ,其中d=121mm,,,,,f=0.52mm/r,n=2r/s,i=1 所以: 確定工序的時(shí)間: 各工序參數(shù)見下表 2、工序Ⅱ切削用量及基本時(shí)間的確定 本工序還是為粗車(車端面、外圓、臺(tái)階面、鏜孔和車溝槽),己知與工序Ⅰ相同。 采用工序Ⅰ確定切削用量和切削時(shí)間的方法,得本工序的切削用量及基本時(shí)間見下表: 3、工序Ⅵ切削用量及基本時(shí)間的確定 (1)切削用量 本工序?yàn)殂@孔,刀具選用高速鋼復(fù)合鉆頭,直
24、徑d=5mm;鉆4個(gè)通孔;使用切削液。 ①確定進(jìn)給量f。由于孔徑和深度均很小,宜采用手動(dòng)進(jìn)給。 ②選擇鉆頭磨鈍標(biāo)準(zhǔn)及耐用度。根據(jù)表5-130,鉆頭后刀面最大磨損量為0.8mm;耐用度T=15min。 ③確定切削速度V。由表5-132,=670MPa的45鋼加工性屬5類。根據(jù)表5-127,暫定進(jìn)給量f=0.16mm/r。由表5-131,可查得V=17m/min,n=18r/s。 (2)基本時(shí)間 鉆4個(gè)直徑為5mm深12mm的通孔,基本時(shí)間約為20s。 4、工序Ⅷ切削用量及基本時(shí)間的確定 ⑴切削用量 本工序?yàn)殂姴郏x刀具為高速鋼三面刃銑刀。機(jī)床選用X62型臥式機(jī)
25、床。共銑4個(gè)槽。 ①確定切削速度和工作臺(tái)每分鐘進(jìn)給量f.查表得公式: v= 查表得:(=56;;;;;;m=0.2;=13mm;=0.08mm/z ; =13mm;z=20;d=125mm;=1.0) v==39.84m/min n= =10.15r/s 根據(jù)銑床工作臺(tái)進(jìn)給量表,選擇=0.063mm/s,=75mm/min 基本時(shí)間,根據(jù)表 T= 式中:l=7.5mm;=+(1~3);=13mm;d=125mm;=45mm;=4mm;i=4 T==166s 6.2 工序第Ⅰ、第Ⅱ、第Ⅵ、第Ⅷ切削用量及基本時(shí)間的確定 將前面進(jìn)行的工作所得的結(jié)果,填入工藝文件。
26、(見附表) 7 夾具設(shè)計(jì) 本夾具是工序Ⅵ用三面刃銑刀縱向進(jìn)給粗銑16mm槽口的專用夾具,在X62W臥式銑床上加工離合器齒輪一個(gè)端面上的兩條互成90的十字槽。 7.1 夾具的定位方案 以端面及Ф68K7mm 孔為定位基準(zhǔn),采用平面在定位盤的短圓柱面及臺(tái)階面上定位。中間圓柱用夾緊工件,圓柱于臺(tái)階面上方處沿夾具45開孔用于固定工件孔與x、y軸方向45偏差。其中臺(tái)階平面限制3個(gè)自由度,短圓柱臺(tái)限制2個(gè)自由度。 7.2 夾緊機(jī)構(gòu) 旋緊上部螺母,運(yùn)用手動(dòng)夾緊可以滿足。采用螺母壓緊壓板夾緊工件,壓板夾緊主要防止工件在銑銷力下產(chǎn)生傾覆和振動(dòng),手動(dòng)螺旋夾緊可。 7.3 誤差分析 1.定位
27、盤的直徑與內(nèi)孔Ф68配合間隙誤差分析。 ①:間隙計(jì)算 定位盤加工直徑尺寸為Ф68f7,則其與孔的配合為Ф68。內(nèi)孔Ф68K7經(jīng)查表得Ф68,公差值為0.009-(-0.021)=0.03mm。定們盤Ф68f7經(jīng)查表得Ф68,公差值為0.03mm。 它們的最大間隙為:68.009-67.94=0.069mm。 最小間隙為:67.979-67.97=0.009mm。 其間隙范圍為:0.009-0.069mm。 (間隙是孔的尺寸減去相配合軸的尺寸之差為正,所以68為間隙配合) ②:誤差分析 該工件的定位基準(zhǔn)圓心將由于配合狀態(tài)的不同可能在最大范圍內(nèi)變動(dòng),如圖所示為Ф0.069是工件
28、圓心的變動(dòng)范圍而形成了定位誤差。其理想定位基準(zhǔn)為O點(diǎn),則它們的間隙為0.009mm,由于安裝工件后,在工件套上壓力板,并鎖上螺母,這樣把工件裝在夾具上的傾斜度減得很小,幾乎為0。所以不需要考慮工件的傾斜度誤差。定位誤差是由于工件定位不準(zhǔn)或定位盤與工件配合有間隙。(間隙越大誤差值則越大) ③:誤差計(jì)算 對(duì)于間隙范圍尺寸0.009-0.069誤差計(jì)算: 在銑床上加工,其平均經(jīng)濟(jì)精度為9級(jí),查表得ω=0.05。 2.定位銷與工件角度誤差分析 ①:角度與間隙分析 在工件與夾具間套上一根定位銷,此時(shí)工件只沿定位銷直線串動(dòng),串動(dòng)范圍為Ф0.069mm,或在銷與工件孔的間隙變動(dòng),
29、而其它變動(dòng)范圍很小,大小主要由定位銷與工件配合間隙來定的。 ②:計(jì)算兩者的間隙配合的間隙誤差 為了它們的角度更準(zhǔn),在能加工與配合的情況下它們的間隙應(yīng)盡量的小,由表查得定位銷的尺寸為Ф5s6比較適合,Ф5g6為Ф5mm,公差為0.008mm,所以它們配合最大間隙D為0.012mm,最小間隙為0.004mm,間隙范圍為:0.004-0.012mm ③:角度計(jì)算 它們的偏移的最大角度為: arctan A==0.007 經(jīng)查表夾具上45角公差取Tα=0.5 (是定位誤差的一部分)。銑床平均加工經(jīng)濟(jì)精度10級(jí),查表得ω=0.08 所以角的定位誤差為: 3.減少誤差的方法:
30、 這些誤差影響差工件加工的精度,我們應(yīng)該盡量減少這些誤差。 若不能滿足加工精度要求時(shí),可采用下述方法解決: ①:減小銷子與孔的配合間隙,銷子直徑選Ф6g5或Ф6h6。 ②:采用活動(dòng)錐形定位銷,使孔與銷無間隙配合。 ③:底板的平面度精度要高。 ④:定位盤與工件孔Ф68配間隙應(yīng)盡量的小。 ⑤:定位盤與工件孔Ф68的同軸度允值應(yīng)最小。 7.4 夾緊力的計(jì)算 夾緊力的作用點(diǎn)位置和方向確定以后,還需要合理地確定夾緊力的大小,夾緊力不足便會(huì)使工件在切削過程中產(chǎn)生位移并容易引起振動(dòng),夾緊力過大又會(huì)造成工件或夾具不應(yīng)有的變型或表面損傷,因此,應(yīng)對(duì)所需的夾行計(jì)算。 理論上,夾緊力的大小
31、應(yīng)與作用在工緊力進(jìn)件上的其他力相平衡;實(shí)際上,夾緊力的大小還與工藝系統(tǒng)的剛度、夾緊機(jī)構(gòu)的傳遞效率等因素有關(guān)。 采用估算法確定夾緊力的大小,根據(jù)工件所受切銷力、夾緊力、摩擦力等作用的情況,實(shí)際夾緊力Fs等于計(jì)算出切銷力F乘以安會(huì)系數(shù)K: Fs=F*K 安全系數(shù)K的選擇應(yīng)根據(jù)切削的具體情況和所用夾緊機(jī)構(gòu)的特點(diǎn)來選取,一般粗加工或斷續(xù)力切削時(shí)取K=2.5~3;精加工和連續(xù)切削時(shí)取K=1.5~2;如果夾緊力的方向和切削力的方向相反,為了保證夾緊K值可取2.5~3。 計(jì)算切削力的指數(shù)公式: F=C a f a z d K 其中查表得: C=96.6; a=16mm; KF=0.88;
32、 f=0.08mm/r; yF=0.75 a=12.5mm; z=6 ;d=16; qe=-0.87; 代入計(jì)算得:F=96.6160.0812.56160.88=985.95N 實(shí)際切削力為:Fs=985.952.5 =2464.875N (摩擦系數(shù)只在夾緊機(jī)構(gòu)有足夠剛性時(shí)才考慮) 參考文獻(xiàn)《金屬切削手冊(cè)》 8 小結(jié) 此刻我懷著輕松有點(diǎn)激動(dòng)的心情在這里寫小結(jié)。也許說的有些過分有些夸張但是我們總算可以松口氣啦!在還沒完成前一個(gè)字“忙”真的很難概括。 課程設(shè)計(jì)目:使學(xué)生在機(jī)械繪圖、機(jī)械制造工藝、夾具設(shè)計(jì)等方面進(jìn)行一次較為全面的
33、系統(tǒng)性訓(xùn)練,使學(xué)生掌握各種機(jī)床裝備應(yīng)用技能,加強(qiáng)對(duì)機(jī)械制造技術(shù)的認(rèn)識(shí),熟悉機(jī)械零件的從毛胚到成品的生產(chǎn)過程…… 內(nèi)容包括:編制零件繪制機(jī)械加工工序簡(jiǎn)圖、機(jī)械加工工藝規(guī)程、備選擇機(jī)床工藝裝、確定切削用量及工時(shí)定額、填寫機(jī)械加工工藝工序卡片、撰寫機(jī)械加工工藝及裝備課程設(shè)計(jì)說明書。雖然我們四個(gè)人一組,但是著巨大的工作量足以把我們每個(gè)人吞噬、毀滅。 在這期間我遇到很多困難:工時(shí)怎樣算、切削余量怎樣定、誤差怎樣去定……這是我們共同的問題共同提出來共同解決,還有組與組同學(xué)之間在一起討論、一起鉆研這是從沒有過的認(rèn)真。這是一個(gè)大家很好的交流平臺(tái),雖然有一天我們都將走出校園但相信我們每個(gè)人
34、都會(huì)記得這次難忘的課程設(shè)計(jì),不一樣的日子…… 這一周很快就過去了! 這暫且作為我們的一種感受和總結(jié)寫在這里吧!! 9 參考文獻(xiàn) [1]趙家奇.機(jī)械制造工藝學(xué)課程設(shè)計(jì)指導(dǎo)書(第2版)[M].北京:機(jī)械工業(yè)出版社,2000.10 [2]李 云.機(jī)械制造及設(shè)備指導(dǎo)手冊(cè)[M].北京:機(jī)械工業(yè)出版社,1997.8 [3]孟少農(nóng).機(jī)械加工工藝手冊(cè)[M].北京:機(jī)械工業(yè)出版社,1991.9 [4]徐圣群.簡(jiǎn)明加工工藝手冊(cè)[M].上海:科學(xué)技術(shù)出版社,1991.2 [5]徐圣群.簡(jiǎn)明加工工藝手冊(cè)(第2版)[M].北京:機(jī)械工業(yè)出版社,2003.1
- 溫馨提示:
1: 本站所有資源如無特殊說明,都需要本地電腦安裝OFFICE2007和PDF閱讀器。圖紙軟件為CAD,CAXA,PROE,UG,SolidWorks等.壓縮文件請(qǐng)下載最新的WinRAR軟件解壓。
2: 本站的文檔不包含任何第三方提供的附件圖紙等,如果需要附件,請(qǐng)聯(lián)系上傳者。文件的所有權(quán)益歸上傳用戶所有。
3.本站RAR壓縮包中若帶圖紙,網(wǎng)頁內(nèi)容里面會(huì)有圖紙預(yù)覽,若沒有圖紙預(yù)覽就沒有圖紙。
4. 未經(jīng)權(quán)益所有人同意不得將文件中的內(nèi)容挪作商業(yè)或盈利用途。
5. 裝配圖網(wǎng)僅提供信息存儲(chǔ)空間,僅對(duì)用戶上傳內(nèi)容的表現(xiàn)方式做保護(hù)處理,對(duì)用戶上傳分享的文檔內(nèi)容本身不做任何修改或編輯,并不能對(duì)任何下載內(nèi)容負(fù)責(zé)。
6. 下載文件中如有侵權(quán)或不適當(dāng)內(nèi)容,請(qǐng)與我們聯(lián)系,我們立即糾正。
7. 本站不保證下載資源的準(zhǔn)確性、安全性和完整性, 同時(shí)也不承擔(dān)用戶因使用這些下載資源對(duì)自己和他人造成任何形式的傷害或損失。