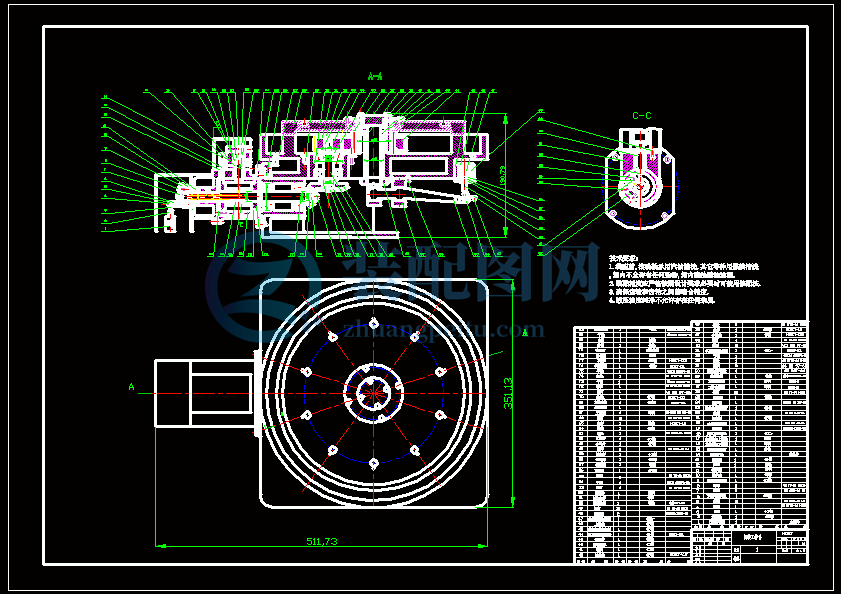
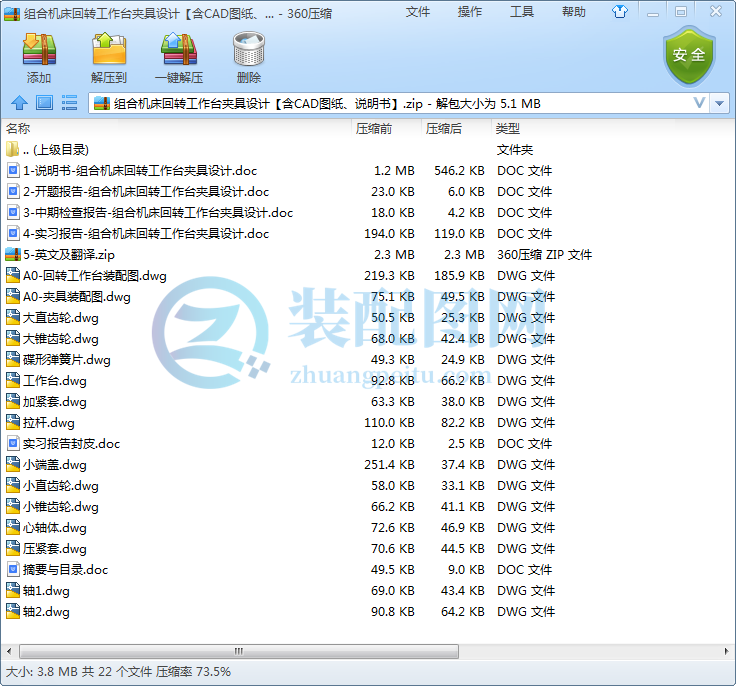


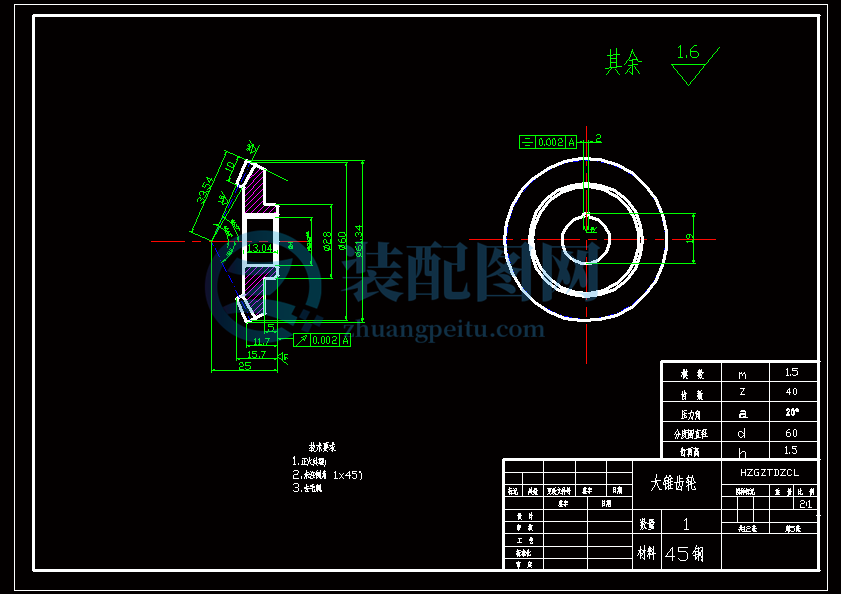
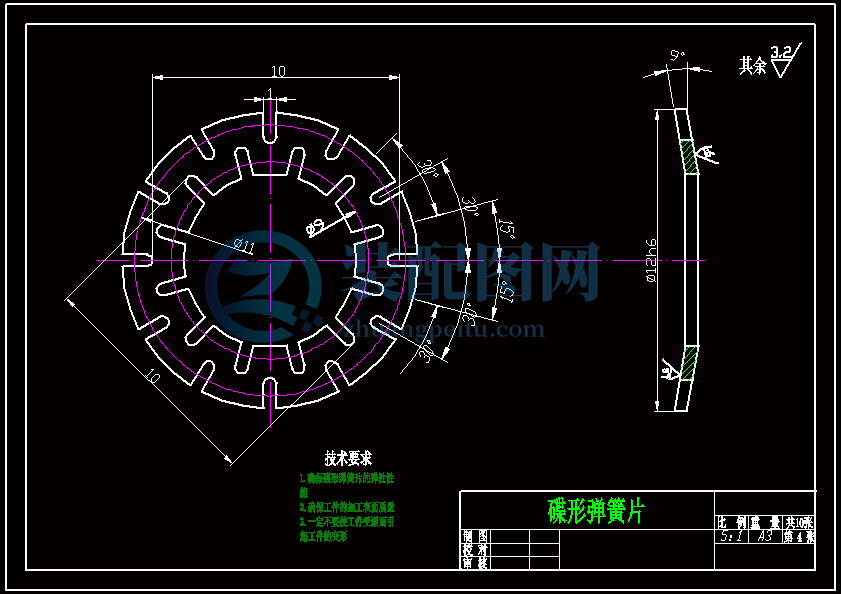
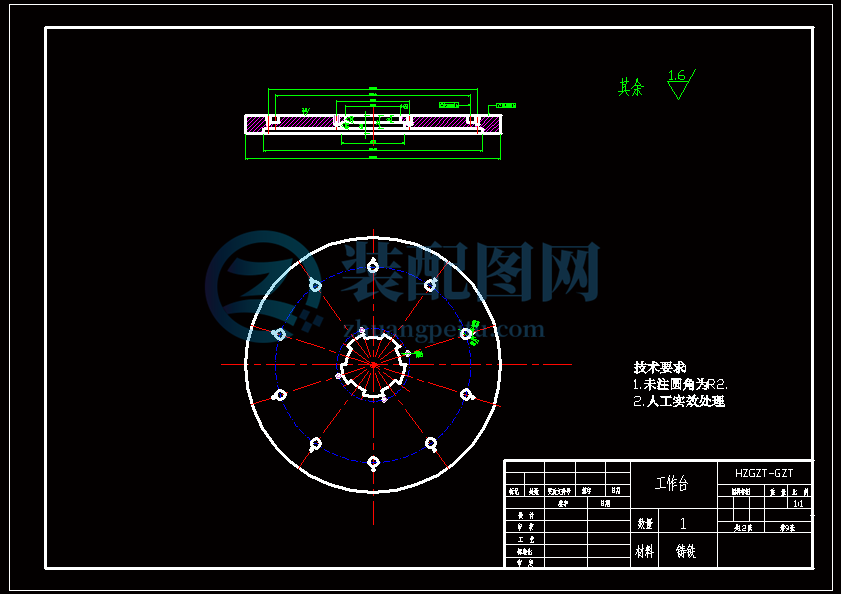

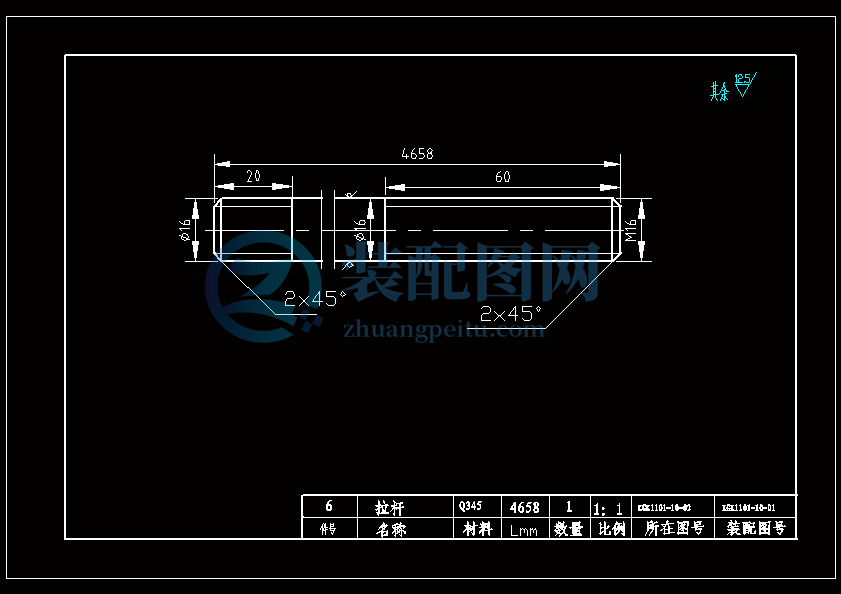
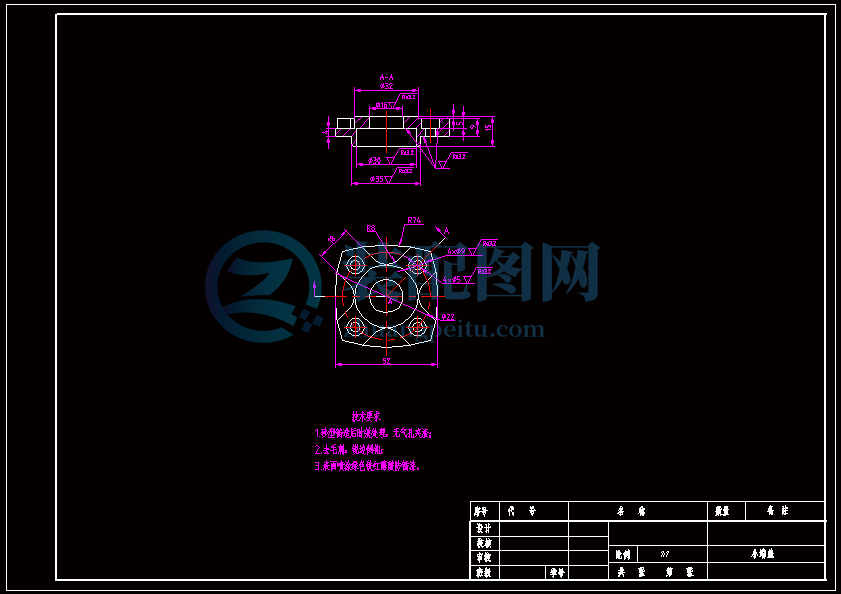
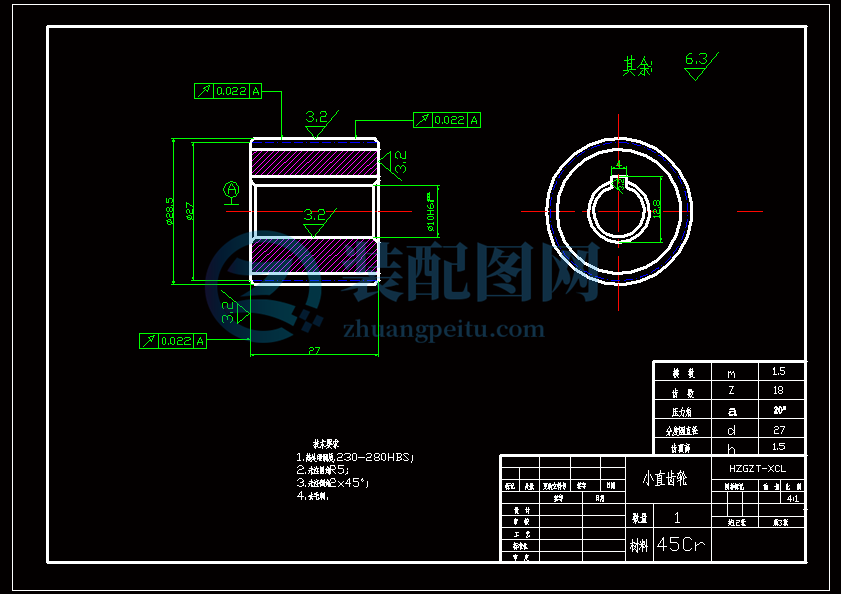
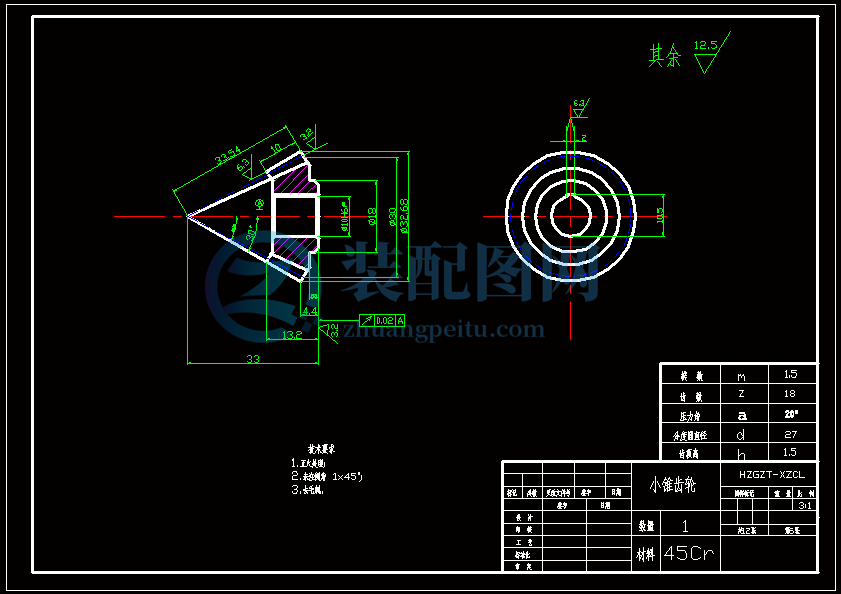
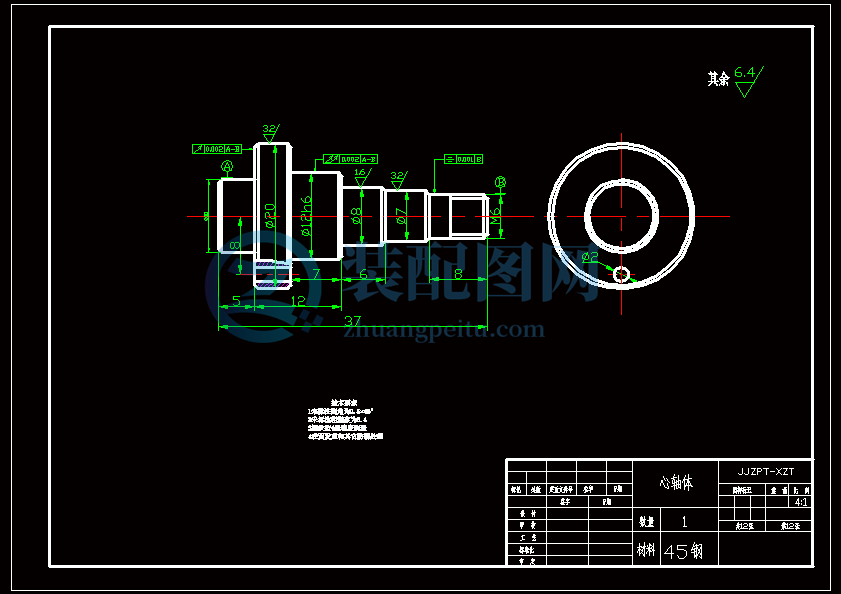
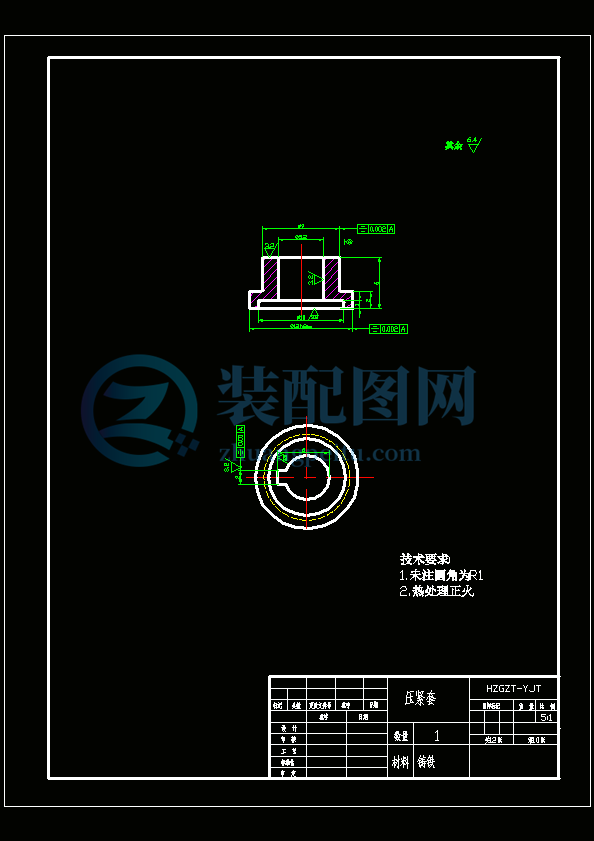
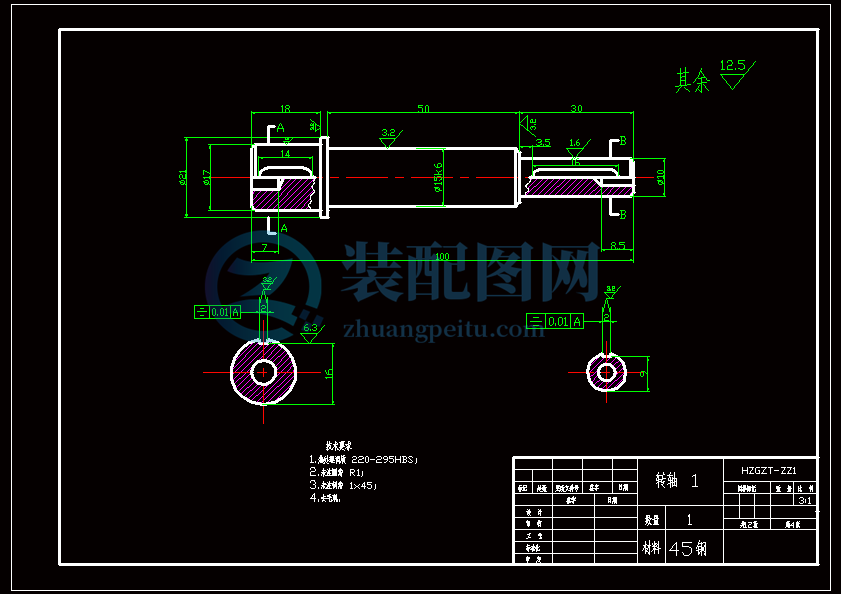
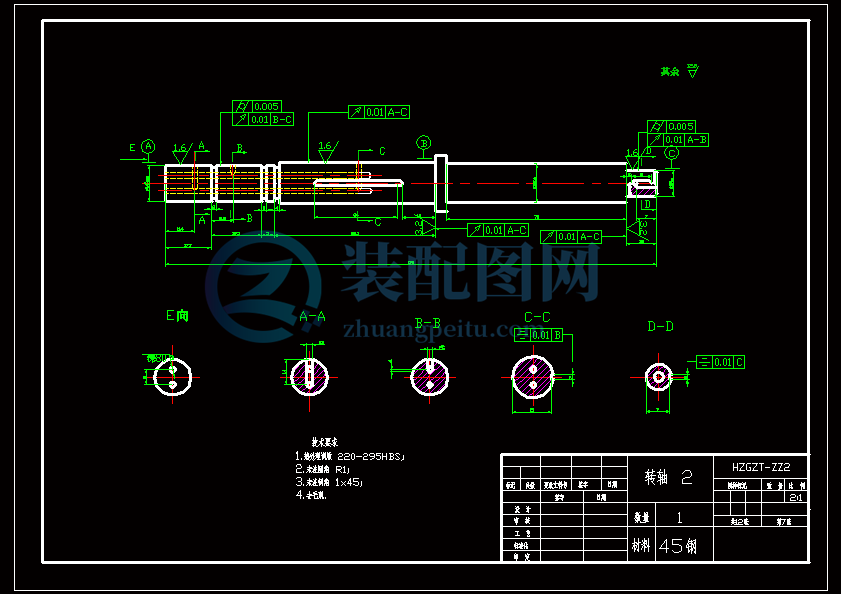
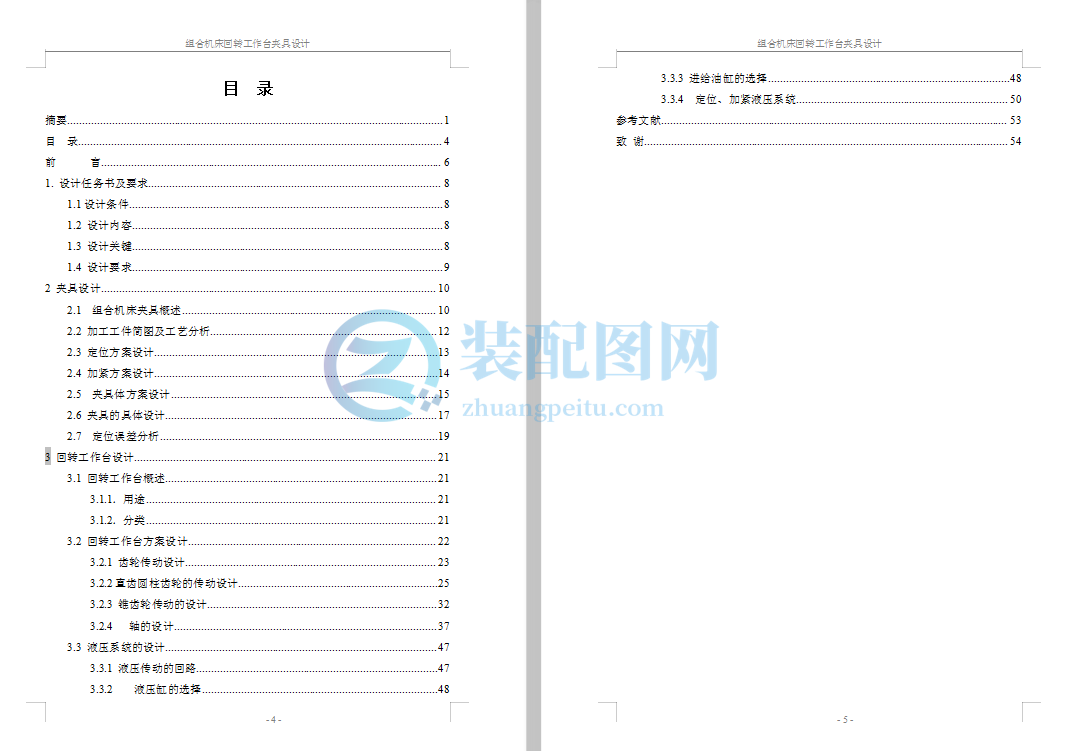
組合機床回轉(zhuǎn)工作臺夾具設計
摘 要
組合機床是隨著生產(chǎn)的發(fā)展由萬能機床和專用機床發(fā)展來的。組合機床是按照高度工序集中的原則設計的,即一臺機床上可以同時完成許多同一中工序或多種不同工序的加工。組合機床分大型組合機床和小型組合機床兩大類。按配置型式分為單工位和多工位機床兩大類。
二十一世紀的制造業(yè)面臨著顧客需求驅(qū)動、不可預測、快速多變和來自全球不斷增加的市場競爭,而且競爭不斷加劇。市場的不斷變化要求制造系統(tǒng)加工的產(chǎn)品品種能夠快速變換以滿足市場需求。
組合機床是由大量的通用部件和少量的專用部件組成的工序集中的高效率機床。它具有生產(chǎn)效率高,加工精度穩(wěn)定等特點。
組合機床在汽車,拖拉機,柴油機,電機,儀器儀表,軍工及縫紉機、自行車等輕工業(yè)大批量生產(chǎn)中已獲得廣泛的應用;一些中小批量生產(chǎn)的企業(yè),如機床、機車、工程機械等制造業(yè)也已推廣應用。組合機床最適宜于加工各種大中型箱體類零件,如氣缸蓋、氣缸體、變速箱體、電機座及儀表殼等零件;也可用來完成軸套類、輪盤類、叉架類和蓋板類零件的部分或全部工序的加工。
本設計介紹了減振器活塞及支承座上雙面活塞八個大孔和八個小孔的多工位立式組合鉆床的設計過程。它包括組合鉆床的總體設計,主軸箱設計和夾具的設計三大部分。前者包括組合鉆床總體設計,切削用量的制定及刀具的選用。三圖一卡(被加工零件工序圖,加工示意圖,機床聯(lián)系尺寸圖,機床生產(chǎn)率計算卡)編制。中者包括主軸箱結(jié)構繪制,主軸箱設計原始依據(jù)圖,主軸結(jié)構形式的選擇及動力計算。傳動系統(tǒng)的設計與計算,主軸箱坐標計算以及主軸箱總圖設計,部分軸,齒輪,軸承的校核。后者包括工作臺的設計和夾具的布置,以及完成多工位的機械傳動部分。
關鍵詞: 組合機床 鉆床 總體設計 主軸箱設計 回轉(zhuǎn)工作臺 齒輪 夾具
- 56 -
Abstract
Combine the tool machine is develop by the all-powerful tool machine and the appropriation tool machine to come along with the development that produce.Combine the tool machine is according to principle design of the high work preface concentration of, namely one pedestal tool machine can complete many same medium work preface or various different work prefaceseseseses to process at the same time up.Combine the tool machine for cent large combination tool machine and the small scaled combination tool machine two major type.Press to install the pattern to is divided into the single work and many tool machine of works two major types.
21 centuries of manufacturing industry faces the customer need to drive, inscrutability, change and come from the market that world continuously increase the competition quickly and much, and compete to turn worse continuously.Market continuously change to request to make the product species that system process can quickly transformation with satisfy the market need.
Combine the tool machine is high-efficiency tool machine of the work preface concentration that be constitute by the in great quantities in general use parts and the appropriation parts of the jot.It has the efficiency of production high, process the accuracy stability etc. characteristics.
Combine the tool machine in the automobile, tractor, diesel engine, electrical engineering, the instrument appearance, the soldier work and sewing machines, bicycle etc. the light industry large quantity quantity produce in have already acquired the extensive application;Some business enterprises that wins the small batch quantity to produce, have already also expanded the application such as the manufacturing industries, such as tool machine, motorcycle and the engineering machine...etc..Combine the tool machine the most suitable and proper in process various body spare parts, if the air cylinder cover, air cylinder body, become soon spare partses such as a body, the electrical engineering and the appearance hull etc.;Also can use to process to part of or all work prefaces of complete stalk set, a dish, the fork and the cover plank spare partses.
This design introduces to reduce to flap the machine piston and pay the design process that a sign type of many works combination of accept the up two-sided piston eight big bores of and eight eyelets drills the bed.It include the combination to drill the bed total design, the principal axis box designs to design the three greatest parts with tongs.The former includes the combination to drill the total design of bed, slicing the establishment and knifes of pare the dosages to have of choose to use.Three one card( was process the spare parts work preface diagram, process the sketch map, the tool machine contact size diagram, the tool machine rate of production calculation card) establishment of figureses.The medium includes a structure of principal axis to draw, a design of principal axis originality according to the diagram, the choice and the motive calculation of the principal axis structure form.Spread the design and calculations of move the systems, the principal axis box sits the mark calculation and a total diagram of principal axis designs, parts of stalk, wheel gear, the pit in the school of the bearings.The latter includes the design and tongses of the work pedestal to arrange, and complete the machine of many works to spread to move the part.
Keyword: Combine the tool machine drills the bed A design Turn round the work set Wheel gear Tongs
目 錄
摘要 1
目 錄 4
前 言 6
1. 設計任務書及要求 8
1.1設計條件 8
1.2 設計內(nèi)容 8
1.3 設計關鍵 8
1.4 設計要求 9
2 夾具設計 10
2.1 組合機床夾具概述 10
2.2 加工工件簡圖及工藝分析 12
2.3 定位方案設計 13
2.4 加緊方案設計 14
2.5 夾具體方案設計 15
2.6 夾具的具體設計 17
2.7 定位誤差分析 19
3 回轉(zhuǎn)工作臺設計 21
3.1 回轉(zhuǎn)工作臺概述 21
3.1.1.用途 21
3.1.2.分類 21
3.2 回轉(zhuǎn)工作臺方案設計 22
3.2.1 齒輪傳動設計 23
3.2.2直齒圓柱齒輪的傳動設計 25
3.2.3 錐齒輪傳動的設計 32
3.2.4 軸的設計 37
3.3 液壓系統(tǒng)的設計 47
3.3.1 液壓傳動的回路 47
3.3.2 液壓缸的選擇 48
3.3.3 進給油缸的選擇 48
3.3.4 定位、加緊液壓系統(tǒng) 50
參考文獻 53
致??謝 54
前 言
畢業(yè)設計是對大學期間所學知識的一次總的檢驗和鞏固,是一次很好的理論聯(lián)系實際的鍛煉,相比以前的幾次課程設計,畢業(yè)設計對所學基礎知識和專業(yè)知識的涉及面更加廣泛,是知識與實踐的有機結(jié)合。做好本次畢業(yè)設計可以為以后的工作打下堅實的基礎和積累豐富的經(jīng)驗,因此本次畢業(yè)設計具有很重要的意義。
本次畢業(yè)設計的主要任務是設計用于減振器活塞及支承座上雙面活塞孔的加工組合機床.。因此《畢業(yè)設計說明書》對雙面活塞孔的加工組合機床做了系統(tǒng)的的設計與介紹。雙面活塞孔的加工組合機床主要部分是主軸箱、工件夾具和工作臺液壓傳動系統(tǒng),它在機床加工過程中起著關鍵部位和有著非常重要的作用,應用范圍相當廣泛。設計雙面活塞孔的加工組合機床計時,在保證得到所要求孔在加工的同時,其安全性、精確性和機床的效率也是至為重要。在這次設計中,我查閱了大量的參考資料,在畢業(yè)實習中對多家工廠進行了參觀學習,并請教老師和現(xiàn)場的技術工人,積累了一些雙面活塞孔的加工組合機床設計方面的知識,并在此基礎上盡量做到優(yōu)化設計。
組合機床的設計,目前基本上有兩種情況:其一,根據(jù)具體加工對象的具體情況進行專門設計,這是當前最普遍的一種,其二,隨著組合機床在我國機械行業(yè)的廣泛應用,一些工人根據(jù)自己生產(chǎn)和使用組合機床的經(jīng)驗,發(fā)明了具有通用部件的組合機床,叫做“專能組合機床”。這次的雙面活塞孔的加工組合機床就是屬于前一種。
畢業(yè)設計的基本要求是:
1) 既要完成任務,又要培養(yǎng)學生獨立動手的操作能力,而且把對學生的培養(yǎng)放在第一位。在指導老師的指導下,根據(jù)所選定的設計課題,通過實習,結(jié)合工程實際,獨立完成設計工作,受到一次機械工程師應該如何解決工程實際問題的一次初步訓練。
2) 通過畢業(yè)設計,使學生受到綜合運用知識,解決實際問題的能力,提高自身技術水平,運算能力及運用計算機識圖、制圖和查閱手冊,使用國家標準和信息資料的能力,文字表達能力和一般組織管理能力。
3) 培養(yǎng)自己獨立工作的能力,鞏固和擴大專業(yè)知識面,有較強的自學能力及工作適應能力,提高運用科研成果和新技術的能力及對現(xiàn)有設備和生產(chǎn)過程進行技術改造的能力。
4) 培養(yǎng)學生嚴謹求實,理論聯(lián)系實際的工作作風和嚴肅認真、一絲不茍的科學態(tài)度,使學生樹立正確的生產(chǎn)觀點和技術經(jīng)濟觀點。在設計過程中,多次經(jīng)焦鋒老師耐心指導,在此表示深深的謝意!
由于本人水平有限,時間倉促,設計中難免有不少缺點和錯誤,懇切的希望焦老師和讀者提出寶貴意見,給予批評指正!
1. 設計任務書及要求
組合機床在我國得到廣泛的應用,在組合機床上可以完成鉆孔、鉸孔、攻絲、鏜孔、鏜孔車端面、車削和銑削等加工工序。因此組合機床近年來廣泛應用于各個生產(chǎn)部門中,在國民經(jīng)濟中占有較重要的地位。
1.1設計條件
1) 對減振器活塞支撐座的孔進行粗加工
2) 減振器活塞表面直徑40cm、加工孔厚度10cm、活塞總厚度22cm
3) 減振器活塞表面均勻分布8個大孔直徑3mm 均勻分布8個小孔直徑2.5mm
4) 加工工件材料:一級鑄鐵。
5) 所選電動機轉(zhuǎn)速約為910~1000r/min。
6) 批量條件:大批量生產(chǎn)。
7) 制造條件:一般制造條件,中型工廠生產(chǎn)。
1.2 設計內(nèi)容
1) 設計方案的選擇與計算。
2) 總體結(jié)構的設計,各個零件的計算與設計,成套圖紙及說明書。
1.3 設計關鍵
1) 選擇合適的主軸及主軸箱、合適的夾具和工作臺的液壓轉(zhuǎn)動裝置。
2) 設計適合中型工廠生產(chǎn)的零部件。
3) 必須保證產(chǎn)品的精度和經(jīng)濟性。
1.4 設計要求
1) 運轉(zhuǎn)定性
A. 軸承有一定的潤滑性。
B. 主要零部件不易損壞。
C. 對提升線速度有一定的要求。
D. 環(huán)境的機械傳動平穩(wěn),支撐零件具有足夠的剛度,無明顯的振動。
E. 有良好的傳動,
2) 無害性
A. 工作時噪聲低于標準規(guī)定的水平。
B. 軸承無漏油現(xiàn)象。
C. 盡量減少各種振動和沖擊。
3) 技術經(jīng)濟性
A. 結(jié)構簡單,減輕自重,減少制造成本,系列化。
B. 采用較高的傳動系統(tǒng)。
4) 結(jié)構工藝性
A. 無特殊加工的零部件。
B. 結(jié)構易于拆裝,運貨。
5) 造型藝術性
A. 外觀造型新穎。
B. 尺寸比例符合美觀和規(guī)律。
C. 外觀,結(jié)構,材料的選擇和表面處理要協(xié)調(diào)。
6) 設計規(guī)范性
A. 零部件盡量采用標準件。
B. 技術參數(shù)符合優(yōu)先數(shù)系。
2. 夾具設計
2.1 組合機床夾具概述
“工欲其善,必先利其器”這是我國勞動人民在生產(chǎn)斗爭中對工具重要性所作的結(jié)論。在現(xiàn)代化生產(chǎn)中,工具(工藝裝備)的作用也是如此。在機械制造工業(yè)中,為了達到保證產(chǎn)品質(zhì)量、改善勞動條件、提高勞動生產(chǎn)率及降低勞動成本的目的,在工藝過程中,除機床等設備外還大量使用著各種工藝裝備。它包括夾具、模具、刀具、輔助工具及其測量工具等。因此,廣義地說,夾具是一種保證產(chǎn)品質(zhì)量并便利和加速工藝過程的一種工藝裝備。不同的夾具,其結(jié)構形式、工作情況、設計原則都不同,但就其數(shù)量和生產(chǎn)中所占的地位來說,應該以機床夾具為首。
機床夾具設計是工藝準備工作的重要內(nèi)容之一。夾具設計的質(zhì)量對生產(chǎn)率、加工成本以及生產(chǎn)安全等都有直接的影響,為此設計夾具時應考慮以下幾個方面的基本原則和要求。
1) 能保證工件的加工要求。保證加工質(zhì)量是設計時首要考慮的要求,即必須穩(wěn)定地達到工序圖上所規(guī)定的加工精度和表面粗糙度。這主要有所設計的定位裝置(有時要結(jié)合夾緊一起考慮)來保證。
2) 能提高加工效率。所設計的夾具結(jié)構在與生產(chǎn)批量相適應的條件下,應盡量采用夾緊可靠、快速高效的夾緊機構與傳動方式以縮短輔助時間提高勞動生產(chǎn)率。
3) 有利于降低成本。在保證加工質(zhì)量和效率的前提下,夾具結(jié)構應力求簡單。盡量采用標準元件和組合元件,專用零件的結(jié)構工藝性要好,制造容易,可縮短夾具制造周期、降低工件的生產(chǎn)成本。
4) 夾具操作要安全方便。夾具結(jié)構中必要時要考慮安全防護裝置(含防屑、防塵、防油及噪音污染等);良好的排屑措施、滑潤方式以及操作維護方便等要求。
5) 考慮夾具的適應性。在滿足所要求的加工質(zhì)量條件下,有時應考慮產(chǎn)品近期的發(fā)展,品種增多的要求,適當擴大夾具的適應能力,使夾具具有一定的通用性、也是夾具設計經(jīng)常需要主意的問題之一
夾具是組合機床的重要組成部件,是根據(jù)機床的工藝和結(jié)構方案的具體要求而專門設計的。它是用于現(xiàn)實被加工零件的準確定位,夾壓,刀具的導向,以及裝卸工件時的限位等作用的。
組合機床夾具和一般的夾具所起的作用看起來好像很接近,但其結(jié)構和設計要求卻有著顯著的區(qū)別。組合機床夾具的結(jié)構和性能,對組合機床的配置方案的選擇,有很大的影響。下面介紹一下組合機床夾具的一些主要特點。
(a) 一般的機床夾具是作為機床的輔助機構設計的,而組合機床機床夾具是機床的主要組成部分,其設計工作是整個組合機床設計的重要部分之一。
(b) 組合機床夾具和機床其它部分有極其密切的聯(lián)系:如回轉(zhuǎn)或移動工作臺,回轉(zhuǎn)鼓輪,主軸箱,刀具和輔具,鉆模板和托架,以及支撐部件等等。正確地解決它們之間的關系,是保證組合機床的工作可靠和使用性能良好的重要條件之一。而且夾具的結(jié)構也要按這些部件的具體要求來確定。如在液壓驅(qū)動的立式回轉(zhuǎn)工作臺機床上的夾具,其夾壓系統(tǒng)就可以采用液壓作為動力;而在臥式鼓輪機床上的夾具,則多采用電氣——機械的加緊方式。
(c) 由于組合機床常是多刀,多面和多工序同時加工,會產(chǎn)生很大的切削力和振動。因此組合機床夾具必須具有很好的剛性和足夠的加壓力,以保證在整個加工過程中工作不產(chǎn)生任何位移。同時,也不應使工件產(chǎn)生不容許的變形。
(d) 組合機床夾具是保證加工精度(尺寸精度、幾何精度和位置精度等)的關鍵部件,其設計、制造和調(diào)整都必須有嚴格的要求,使其能持久地保持精度。
(e) 組合機床夾具應便于實現(xiàn)定位和夾壓的自動化,并有動作完成得檢驗信號;保證切削從加工空間自動排除;便于觀察和檢查,以及在不從機床上拆下夾具的情況下,能夠跟換易損件和維護調(diào)整。
此外,組合機床夾具和一般的組合夾具不同,組合夾具是在萬能機床上為了完成某一道工序的加工,用一些標準的和通用的元件組裝成的定位夾壓裝置。用完后,可用這些元件重新組裝成新的夾壓裝置。而組合機床夾具則是以部分的通用元件加上專用件組成的專用夾具,它不便于改裝。
按結(jié)構特點,組合機床夾具分為單工位和多工位夾具兩大類。單工位夾具是指工件在一個工位上完成加工工序的機床夾具。按被加工零件的結(jié)構和加工要求,單工位夾具有固定的,帶滾動和浮動滾道的,帶水盆和小車(或拖板)等形式。多工位組合機床夾具是指工件在幾個工位上順序或平行—順序加工的機床夾具。按移位方式它又分為:固定是多位夾具、回轉(zhuǎn)夾具、移動工作臺夾具、回轉(zhuǎn)工作臺夾具和回轉(zhuǎn)鼓輪夾具等。
2.2 加工工件簡圖及工藝分析
夾具的設計依據(jù)的是工件的加工步驟和具體要求,對工件工藝的具體了解是設計夾具的前提也是重要的依據(jù),因此在設計夾具前應首先分析零件的作用、結(jié)構特點、材料及毛坯制造精度及零件的技術要求,深入分析設計任務書和工序簡圖上所提出的加工要求和設計要求,該工序在整個工藝過程中與前后工序的關系,所采用的切削用量,分析所規(guī)定要求的合理性現(xiàn)將工件的加工過程分析如下:
零件圖如下所示:
圖2—1,加工零件圖
本次所設計機床的目的是為了加工本工件上的16個小孔,其中8個大孔的直徑為φ3mm,8個小孔直徑為φ2.5mm。加工孔的工序應排在中心孔的精加工之后,而且加工精度不要求過高。由于加工孔的精度不高,所以只采用鉆孔的方式即可,而不必采用鉆、擴、絞相結(jié)合的方式,這樣就大大降低了設計機床的難度,然而由于孔的間距較小,不可能采用多頭鉆的方式,因此在某種程度上來說又增加了所設計機床的難度,為了達到設計的目的和要求,我們小組幾人在一起研究決定將機床設計為多工位回轉(zhuǎn)式組合機床的形式。根據(jù)孔的加工大小的不同和位置的限制,采用2個動力頭,每個動力頭上都裝有跨5個工位的主軸箱,每個工件都要經(jīng)過10個工位才能完成全部孔的加工,這樣就避免了孔間距過小的限制,在回轉(zhuǎn)工作臺上裝有10個手動夾具,工件以其中心孔和一端面定位。
2.3 定位方案設計
在組合機床上加工時,必須使被加工零件對刀具及其導向保持正確的相對位置,這是靠夾具的定位支撐系統(tǒng)來實現(xiàn)。定位支撐系統(tǒng)除用以確定被加工零件的位置外,還要承受被加工零件所受的力.
通過對工件的分析,8個小孔的中心所在的圓和8個大孔的中心所在的圓為同心圓,而且鉆孔的加工排在中心孔的精加工之后,為了使工件能夠很好的定位而且保證所有的孔的具體位置符合設計要求,并保證工件的定位原則,結(jié)合工件的特點采用一面一孔的定位方案來限制工件的5個自由度,具體分析如圖所示:
圖2-2
采用一面一孔的定位方式消除了工件的5個自由度,確保了工件的具體位置,但如何保證夾具和孔的配合,以及工件的裝卸問題,基于自己的總結(jié)和查閱的一些資料,比較了所有的中心定位夾具,最后決定采用碟形彈簧片來夾緊心軸,碟形彈簧片如圖所示:
碟形彈簧片由于它的特殊結(jié)構,當它承受到一定力的時候便會徑向脹開而將工件定心并加緊,從而確保了工件的加工精度,并且方便工件的裝卸實現(xiàn)了機床的高效率從而達到了設計的要求。
2.4 加緊方案設計
在組合機床上加工時,工件依靠夾具上的定位支撐系統(tǒng),獲得刀具及其導向的正確相對位置,還要依靠夾具上的加緊機構,來消除工件因受切削力和工件自重的作用而產(chǎn)生的位移或震動,使工件在加工過程中能繼續(xù)保持定位所得到的正確位置。
加緊機構通常由三個部分組成:加緊動力部分、中間傳動機構和加緊元件。這三部分起著不同的作用:加緊力部分用于產(chǎn)生力源,并將作用力傳給中間傳動機構;中間傳動機構能夠改變作用力的方向和大小,即作為增力機構,同時能產(chǎn)生自鎖作用,以保證在加工過程中,當力源消失時,工件在切削力或震動作用下仍能可靠加緊;加緊元件則用以承受由中間傳動機構傳遞的加緊力,并與工件直接接觸而執(zhí)行加緊動作。
但是,并非全部加緊機構都具備上述三部分,有時可能缺少其中的某一部分,例如手動機構往往就很簡單。
組合機床夾具的加緊機構,就其加緊特性而言,可以分為直接加緊機構和自鎖加緊機構兩大類。如果按加緊動力的來源區(qū)分,可以分為手動加緊機構和自動加緊機構,在自動加緊中,又有氣動加緊、液壓加緊、自動扳手加緊和彈簧加緊等機構。
設計夾具機構時,應滿足的要求如下:
(1) 保證加工精度 加緊機構應能保證工件可靠地接觸相應的定位基面,加緊后不破壞工件的正確位置。加緊后工件在加工切削過程中,不應由于切削力的作用而產(chǎn)生位移和晃動。為此,必須保證加緊機構能產(chǎn)生足夠的加緊力,同時還要求具有較高的剛性。由于組合機床通常都是多面多刀同時加工的,夾具往往在較大的切削力作用下工作,提高加緊機構的剛性,是十分重要的。加緊工件時,不應破壞工件的以加工表面,也不應引起工件過大的變形,加緊機構應力求使工件加緊穩(wěn)定和變形較小,為此,應當正確的選擇加緊部位和設置輔助支撐等。
(2) 保證生產(chǎn)率 加緊機構應當具有適當?shù)淖詣踊潭龋泳o動作要力求迅速。
(3) 保證工作可靠——具有自鎖功能 加緊機構除了應當能產(chǎn)生足夠的加緊力外,通常還要求具有自鎖性能,以保證它的工作可靠性。
(4) 結(jié)構緊湊簡單 在保證加工精度、滿足生產(chǎn)率要求和工作可靠性的原則下,加緊力應越小越好,這樣可以避免使用龐大而復雜的加緊加緊機構和減小加壓變形。
(5) 操作方便,使用安全 由于組合機床生產(chǎn)率高,操作比較頻繁,因此加緊機構應當操作方便省力,采用手動加緊機構時操作力通常不應超過8~10公斤。
鑒于以上設計加緊機構的要求,考慮到所夾工件太小,不適合自動加緊,因此采用手動加緊的方式。
2.5 夾具體方案設計
夾具體是夾具的基礎件,它既要包夾具的各種元件、機構、裝置連接成一個整體,而且,還要考慮工件裝卸方便以及夾具與機床的連接方式。因此,夾具體的形狀和尺寸,主要取決于夾具各組成件的分布位置,工件的外形輪廓尺寸以及加工的條件等。在設計夾具時應滿足以下一些基本要求:
(1) 應有足夠的剛度和強度。加工工件時,為了防止在切削力、夾緊力等外力的作用下,夾具產(chǎn)生不允許的變形和振動,夾具體應具有足夠的壁厚,剛性不足處可適當增加加強筋。
(2) 力求結(jié)構簡單、重量輕。夾具體的外形一般尺寸較大,結(jié)構比較復雜,而且各表面間的相互位置精度要求高,應特別注意其結(jié)構工藝性。
(3) 應便于排除切屑。加工過程中為了防止切屑聚積,影響工件的正確定位和夾具的正常操作,因此在設計夾具體時應考慮切屑的排除問題。
(4) 在機床上的安裝應穩(wěn)定可靠。對于固定在機床上的夾具,應該使重心盡量低;對于不固定在機床上的夾具,則重心和切削力作用點應落在夾具體的作用范圍之內(nèi),重心越高夾具支承面積越大。為了使夾具安裝穩(wěn)定可靠,夾具體底面中部通常挖空。對于翻轉(zhuǎn)或移動式夾具體,應在夾具體上設置手柄或手扶部件,以便于操作。對于大型夾具,在夾具體上應設置吊環(huán)螺栓或者起重孔,以便于吊運。
(5) 應具有良好的結(jié)構工藝性和經(jīng)濟性。夾具體上有三個重要的表面,直接影響夾具的裝配精度,即夾具體底面,固定定位元件和引導裝置的表面,以及夾具安裝時的校正基面。在加工這些表面時,通常是以夾具底面作為定位基準,因此在考慮夾具體的結(jié)構時,應便于達到這些表面的加工要求。在夾具體上供安裝各種元件的表面,一般應鑄出3~5mm的凸臺,以便于減少加工面積。
綜合以上考慮和分析,結(jié)合鉆孔的要求,具體夾具設計如下所示: 由夾具草圖分析,要使工件易于裝卸工件和夾具的定位部分應當采用間隙配合的原則,當卸工件時只要將旋轉(zhuǎn)螺母便可減少碟形彈簧片的變形,從而撤銷對工件的定位,就可以很容易的將工件取下,當裝工件時由于工件和定位系統(tǒng)采用的是間隙配合,很容易將工件裝到夾具上,這是旋轉(zhuǎn)螺母使壓緊套壓緊碟形彈簧片,使彈簧片徑向脹開從而將工件定心并加緊。
2.6 夾具的具體設計
通過對工件的具體分析和夾具加緊的要求,工件在加工時要承受刀具旋轉(zhuǎn)所帶來的扭矩的作用,為了實現(xiàn)對工件的加緊,必須施加一定的軸向力的作用,通過以上的分析可知,工件所受到的扭矩的大小為M=4192N·mm,為了傳遞這樣大的扭矩,根據(jù)碟形彈簧片的計算公式得需要施加的軸向力Q為:
式中 M——所需傳遞的轉(zhuǎn)矩(N);
D——工件定位基面的直徑(mm);
μ——裝夾表面的摩擦因數(shù);
β——碟形彈簧片錐面半角(°);
K——安全系數(shù);
現(xiàn)取安全系數(shù)K=1.5。
裝夾表面的摩擦系數(shù)μ=0.3
工件定位基面的直徑D=12mm。
則根據(jù)公式計算得:
根據(jù)以上計算初選碟形彈簧片的數(shù)量和尺寸如下表所示:
形式和
序號
d
(mm)
D
(mm)
d1
(mm)
D1
(mm)
β
t
(mm)
A
(mm)
B
(mm)
a
(mm)
α
1
8
12
7
11
9°
0.5
10
10
1
30°
根據(jù)尺寸可畫出彈簧片的具體圖如下所示:
通過對夾具受力的分析根據(jù)力的大小現(xiàn)計算夾具的最小直徑:
選擇夾具材料為45鋼。根據(jù)查表可知45鋼的許用應力大小為[δ]=216MP
根據(jù)公式δ=N/A[δ]得A
現(xiàn)根據(jù)工件所承受的轉(zhuǎn)矩進行計算:
已知工件的許用剪切力為[τ]=128
根據(jù)公式求
根據(jù)公式可知所要求的夾具的最小直徑相當小在這里為了適應工藝的要求并考慮到實際的情況,我們選擇工件最小的直徑為6mm。
現(xiàn)對工件的具體設計如下:
心軸體:
壓緊套:
2.7 定位誤差分析
在批量生產(chǎn)中是采用調(diào)整法加工,在不考慮磨損、多次換刀誤差及工藝系統(tǒng)受力變形和熱變形的情況下,可以認為加工表面的位置是不變的。因此,定位誤差實際上是由于工序基準的位置變化引起的,即定位誤差是工序基準在加工尺寸方向上的位置變動量()。
定位誤差太小,說明定位精度高,加工要求容易保證,但會提高定位基準和定位元件的制造精度,并會增加組裝困難,所以定位誤差應合理。一般情況下,定位誤差與相應尺寸應滿足下面不等式:
因為所加工工件是在板狀工件上加工均布的8個大孔φ3和8個小孔φ2.5,工件以底平面及定心和定位孔為定位基準。
孔的孔是由刀具尺寸保證的,加工的工序基準是工件孔的軸線,因為是用定心與工件中心孔配合實現(xiàn)在和方向上的定位,定心也是定位基準。盡管工序基準與定位基準重合,但因中心孔和定心的直徑都有制造誤差,所以工序基準在和方向的位置仍然是變化的,其起最大變動量即為工件的定位誤差,即
所以工件定位良好
3. 回轉(zhuǎn)工作臺設計
3.1 回轉(zhuǎn)工作臺概述
3.1.1.用途
分度回轉(zhuǎn)工作臺是多工位組合機床的一種輸送部件,它將被加工工件從一個工位轉(zhuǎn)換到另一個工位。通常一個工位用作裝夾工件,其他幾個工位同時對工件進行加工,因此,機床的生產(chǎn)率較高,一臺組合機床相當于一條圓形自動線,而且占地面積較小,其結(jié)構比自動線簡單。因此,回轉(zhuǎn)臺式多工位組合機床在組合機床中占有相當大的比重。
近年來國外發(fā)展了行星傳動分度回轉(zhuǎn)工作臺。被加工工件在一個工位上裝加后,工件可繞著工作臺軸線作圓周方向輸送,輸送到各工位后,根據(jù)工藝要求,在工作臺分度轉(zhuǎn)位的過程中,使工件繞夾具軸線回轉(zhuǎn),被加工工件的各面可以依次朝外接受各工位上的動力部件加工。這樣的一臺多工位組合機床,除了可以從被加工工件的頂面和朝向動力部件面進行加工外,還可對多達五個面進行加工,擴大了組合機床的應用范圍。目前這種回轉(zhuǎn)工作臺在我國尚未形成通用部件。
3.1.2.分類
(1) 按傳動方式可分為:機械傳動,液壓傳動,氣壓傳動,氣、液聯(lián)合傳動和行星傳動的回轉(zhuǎn)工作臺。
(2) 按定位方式可分為:圓柱銷或菱形銷定位,圓錐銷定位,反靠定位,齒盤定位和鋼球定位等幾種。
不同的定位方式其結(jié)構不同,能達到的定位精度也不同。定位精度是分度回轉(zhuǎn)工作臺的主要技術性能指標。設計組合機床時,應根據(jù)被加工工件的精度要求,按經(jīng)濟合理的原則選擇分度回轉(zhuǎn)工作臺的定位方式。
分度定位精度高,定位剛性好,分度所需時間短,精度保持時間長,工作安全可靠是對回轉(zhuǎn)工作臺的要求。在上述定位方式中,鋼球定位的回轉(zhuǎn)工作臺,具有分度精度高,定位剛度好等優(yōu)點,目前我國尚未形成通用部件。我國現(xiàn)在回轉(zhuǎn)工作臺通用部件中,以齒盤定位回轉(zhuǎn)工作臺技術性能最優(yōu)。
3.2 回轉(zhuǎn)工作臺方案設計
由于回轉(zhuǎn)工作臺的形式多種多樣,綜合考慮到所設計的任務和要求,通過自己實習所總結(jié)的經(jīng)驗,和自己所掌握的一些資料,結(jié)合所加工零件的實際情況,決定使用液壓傳動方式。
設計回轉(zhuǎn)工作臺首先應當考慮到回轉(zhuǎn)工作臺夾具?,F(xiàn)對回轉(zhuǎn)工作臺夾具做些簡單的介紹,回轉(zhuǎn)工作臺夾具是工件繞垂直軸作回轉(zhuǎn)運動的多工位機床夾具。這類夾具多用于中小工件的多面多工序加工,在每一個工位上可安裝一個或幾個工件。同時在夾具上還設有專門的裝卸工位,使裝卸時間與機動時間相重合,提高機床生產(chǎn)率。
這種夾具通常是由回轉(zhuǎn)工作臺和專用的小夾具組成。小夾具在上面以做了詳細的論述,現(xiàn)對回轉(zhuǎn)工作臺作詳細論述,首先考慮到回轉(zhuǎn)工作臺的分度和定位?;剞D(zhuǎn)工作臺的分度和定位有液壓和機械兩種傳動方式,大型回轉(zhuǎn)工作臺的轉(zhuǎn)盤直徑有800、900、1000、1120、1250、1400毫米六種規(guī)格,工位數(shù)為2、3、4、5、6、8、10、12八種,小型回轉(zhuǎn)工作臺的轉(zhuǎn)盤直徑有500、600、700、800毫米四種規(guī)格,工位數(shù)為3、4、5、6、8、9、10、12八種。根據(jù)所加工零件的特點,選擇回轉(zhuǎn)工作臺的轉(zhuǎn)盤直徑為500mm,工位數(shù)為10。
設計時應正確選用回轉(zhuǎn)工作臺夾具的方案設置,除此之外對于如何布置小夾具應當注意下列問題。
(a) 合理布置小夾具,力求選用較小直徑的轉(zhuǎn)盤,也就是選用小規(guī)格的工作臺。
(b) 小夾具在轉(zhuǎn)盤上一般采用圓柱銷定位,轉(zhuǎn)盤上的圓柱銷孔應在坐標鏜床上加工,以便于機床總裝和檢查精度。安排小夾具時應考慮與工作臺定位機構的關系,力求使精加工工位放在工作臺定位機構的附件,這樣有利于提高機床加工精度。
(c) 相鄰小夾具間的距離不宜太小,以免妨礙切削和冷卻液的排除。
(d) 需要時小夾具的局部可超出工作臺面,但要檢查與其它部件的尺寸關系,以免發(fā)生碰撞。當小夾具的回轉(zhuǎn)中心與回轉(zhuǎn)工作臺的回轉(zhuǎn)中心不同時,更要注意回轉(zhuǎn)時的碰撞問題。
(e) 在設計臥室機床的回轉(zhuǎn)工作臺夾具時,應盡量減少切向和不通過回轉(zhuǎn)工作臺中心的切削力,以免加工時產(chǎn)生振動。
以上是對回轉(zhuǎn)工作臺夾具掌握的一些情況為了滿足上述要求,現(xiàn)對回轉(zhuǎn)工作臺作詳細的方案設計:
結(jié)合加工工件的特點和所掌握的一些情況決定工作臺選用帶回轉(zhuǎn)式油缸分度機構的環(huán)形工作臺,為了實現(xiàn)精確的分度,本工作臺采用齒輪分度的方式,由于回轉(zhuǎn)工作臺有10個工位,因此回轉(zhuǎn)工作臺每次旋轉(zhuǎn)36度,而油缸每次旋轉(zhuǎn)180度,中間采用齒輪傳動的傳動方式,所以傳動比為根據(jù)所設計的特點和傳動比的大小,采用二級傳動的傳動方式,初設傳動比。第一級采用直齒輪傳動的傳動方式,第二級采用直齒錐齒輪的傳動方式,具體傳動方式如圖所示:
圖3-1傳動圖
3.2.1 齒輪傳動設計
齒輪傳動是機械傳動中最重要的傳動之一,型式很多,應用廣泛,傳遞的功率可達近十萬千萬,圓周速度可達200m/s。
齒輪傳動的主要特點有:
1) 效率高 在常用的機械傳動中,以齒輪傳動的效率為高。如一級圓柱齒輪傳動的效率可達99%。這對大功率傳動十分重要,因為即使效率只提高1%,也有很大的經(jīng)濟意義。
2)結(jié)構緊湊 在同樣的使用條件下,齒輪傳動所需要的空間尺寸一般較小。
3)工作可靠、壽命長 設計制造正確合理、使用維護良好的齒輪傳動,工作十分可靠,壽命可達一、二十年,這也是其它機械傳動所不能比擬的。這對車輛及在礦井內(nèi)工作的機器尤為重要。
4)傳動比穩(wěn)定 傳動比穩(wěn)定往往是對傳動性能的基本要求。齒輪傳動獲得廣泛應用,也就是由于具有這一點。
但是齒輪傳動的制造及安裝精度要求高,價格較貴,且不宜用于傳動距離過大的場合。
齒輪傳動可做成開式、半開式及閉式。如在農(nóng)業(yè)機械、建筑機械以及簡易的機械設備中,有一些齒輪傳動沒有防塵罩或機殼,齒輪完全暴露在外邊,這叫開式齒輪傳動。這種傳動不僅外界雜物極易侵入,而且潤滑不良,因此工作條件不好,輪齒也容易磨損,故只易于低速轉(zhuǎn)動。當齒輪傳動裝有簡單的防護罩,有時還把大齒輪部分的侵入油池中,則稱為半開式齒輪傳動。,它的條件雖有改善,但仍不能做到嚴密防止外界雜物侵入。潤滑條件也不算最好。而汽車、機床、航空發(fā)動機等所用的齒輪傳動,都是裝在經(jīng)過精確加工而且封閉嚴密的箱體內(nèi),這稱為閉式齒輪傳動。它與開式或半開式的相比,潤滑及防護等條件最好,多用于重要的場合
齒輪的主要失效形式有:
1) 輪齒折斷 輪齒折斷有多種形式,在正常工況下,主要是齒根彎曲疲勞折斷,因為在輪齒受載時,齒根處產(chǎn)生的彎曲應力最大,再加上齒根過度部分的截面圖編輯加工刀痕等引起的應力集中作用,當輪齒重復受載后,齒根處就會產(chǎn)生疲勞裂紋并逐步擴展致使輪齒疲勞折斷。
2) 齒面磨損 在齒輪傳動中,齒面隨著工作條件的不同會出現(xiàn)多種不同的磨損形式。這種磨損稱為磨粒磨損。它是開式齒輪傳動的主要失效形式之一。改用閉式齒輪傳動是避免齒面磨粒磨損最有效的辦法。
3) 齒面點蝕 點蝕是齒面疲勞損傷的現(xiàn)象之一。在潤滑良好的閉式齒輪傳動中,常見的齒面失效形式多為點蝕。所謂點蝕就是齒面材料在變化著的接觸應力作用下,由于疲勞而產(chǎn)生的麻點狀損傷現(xiàn)象。齒面上最初出現(xiàn)的點蝕僅為針尖大小的麻點,最后形成了明顯的齒面損傷。
4) 齒面膠合 對于高速重載的齒輪傳動,齒面間的壓力大,瞬時溫度高,潤滑效果差,當瞬時溫度過高時,相嚙合的兩齒面就會發(fā)生粘在一起的現(xiàn)象,由于此時兩齒面又在作相對滑動,相粘結(jié)的部位即被撕破,于是在齒面上沿相對滑動的方向形成傷痕,稱為膠合。
5) 塑性變形 塑性變形屬于輪齒永久變形一大類的失效形式,它是由于在過大的應力作用下,輪齒材料處于屈服狀態(tài)而產(chǎn)生的齒面或齒體塑性流動所形成的。塑性變形一般發(fā)生在硬度低的齒輪上;但在重載作用下,硬度高的齒輪上也會出現(xiàn)。塑性變形又分為滾壓塑變和捶擊塑變。滾壓塑編是由于嚙合輪齒的相互滾壓和滑動而引起的材料塑性流動所形成的。
3.2.2直齒圓柱齒輪的傳動設計
1) 選定齒輪類型、精度等級、材料及齒數(shù)
A. 由于回轉(zhuǎn)工作臺所要求的精度不高故選用7級精度(GB10095—88)
B. 材料的選擇,由《機械設計》第七版,高等教育出版社(下同)表10—1選擇小齒輪材料為40Cr,調(diào)質(zhì)硬度為280HBS,大齒輪材料為45鋼,調(diào)質(zhì)硬度為240HBS,二者材料硬度差為40HBS。
C. 選小齒輪齒數(shù)為Z1=18,大齒輪齒數(shù)為。
2) 按齒面接觸強度設計
由《機械設計》第七版公式(10—9a)進行計算即:
1) 確定公式內(nèi)的各計算數(shù)值
A. 試選載荷系數(shù)為=1.3。
B. 計算小齒輪傳遞的扭矩根據(jù)同組人所算數(shù)據(jù)得
C. 由《機械設計》第七版表10—7選取齒寬系數(shù)=1。
D. 由《機械設計》第七版表10—6查得材料的彈性影響系數(shù)
E. 由《機械設計》第七版圖10—21d按齒面硬度查得小齒輪的接觸疲勞強度極限;大齒輪的接觸疲勞強度極限;
F. 計算應力循環(huán)次數(shù),由于機床回轉(zhuǎn)工作臺的旋轉(zhuǎn)速度較低,因此循環(huán)次數(shù)也較低。
G. 由《機械設計》第七版圖10—19查得接觸疲勞系數(shù),。
H. 計算接觸疲勞許用應力
取失效概率為1%,安全系數(shù)s=1由《機械設計》第七版式(10—12)得
MPa
3) 計算:
A. 試算小齒輪分度圓直徑 ,代入[ ]中較小的值
B. 計算齒寬b
C. 計算齒寬與齒高之比
模數(shù)
齒高
D. 計算載荷系數(shù)
根據(jù)υ和7級精度,由《機械設計》第七版圖10—8查得動載系數(shù)
直齒輪,假設.由《機械設計》第七版表10—3查得
由《機械設計》第七版表10—2查得使用系數(shù);
由《機械設計》第七版表表10—4查得7級精度、小齒輪相對支撐非對稱布置時,
將數(shù)據(jù)代入后得
由b/h=8.01,,查《機械設計》第七版圖10—13得;
故載荷系數(shù):
E. 按實際載荷系數(shù)校正所算得的分度圓直徑,由《機械設計》第七版式(10—10a)得:
F. 計算模數(shù)m
4) 按齒根彎曲強度設計
由《機械設計》第七版式(10—5)得彎曲強度的設計公式為
A. 確定公式內(nèi)的各計算數(shù)值
(1) 由 《機械設計》第七版 圖10—20c查得小齒輪的彎曲疲勞強度極限;大齒輪的彎曲疲勞強度極限 。
(2) 由《機械設計》第七版圖10 —18查得彎曲疲勞壽命系數(shù)為,。
(3)計算彎曲疲勞許用應力
取彎曲疲勞安全系數(shù)S=1.3,由 《機械設計》第七版式(10—12)得
(4)計算載荷系數(shù)K
(5)查取齒形系數(shù)
由《機械設計》第七版表10—5查得,,
(6) 查取應力校正系數(shù)
由《機械設計》第七版表10—5查得 ,。
(7) 計算大、小齒輪的并加以比較
可以看出大齒輪的數(shù)值大
B. 設計計算
對比計算結(jié)果,由齒面接觸疲勞強度計算的模數(shù)m大于由齒根彎曲疲勞強度計算的模數(shù),由于齒輪模數(shù)的大小主要取決于彎曲強度所決定的承載能力,而齒面接觸疲勞強度所決定的承載能力,僅與齒輪直徑(即模數(shù)與齒數(shù)的乘積)有關,為了符合設計要求,使精度更高,特選模數(shù)為m=1.5,小齒輪齒數(shù)為18,大齒輪齒數(shù)為45。
這樣設計的齒輪即滿足了齒面接觸疲勞強度和彎曲疲勞強度,又符合了設計要求確保了精度。
5) 幾何尺寸計算
A. 計算分度圓直徑
B. 計算中心距
C. 計算齒寬厚度
取B1=35mm,B2=27mm.
6) 驗算
合適
7) 結(jié)構設計及繪制齒輪零件圖:
名 稱
代號
備注(mm)
模 數(shù)
m
m=1.5
壓 力 角
分度圓直徑
d
齒 頂 高
齒 根 高
全 齒 高
h
齒頂圓直徑
齒根圓直徑
中 心 距
a
齒數(shù)比
圖3-2小直齒輪
圖3-3 大直齒輪
3.2.3 錐齒輪傳動的設計
1) 選定齒輪類型、精度等級、材料及齒數(shù)
A. 由于回轉(zhuǎn)工作臺所要求的精度不高故選用8級精度(GB10095—88)
材料的選擇,由《機械設計》第七版表10—1選擇校齒輪材料為40Cr,調(diào)質(zhì)硬度為280HBS,大齒輪材料為45鋼,調(diào)質(zhì)硬度為240HBS,二者材料硬度差為40HBS。
B. 選小齒輪齒數(shù)為Z1=20,大齒輪齒數(shù)為
2) 按齒面接觸疲勞強度確定傳動的主要參數(shù)和尺寸
根據(jù)《機械設計》(西北工大第七版高等教育出版社)式(10-26)計算小錐齒輪分度圓直徑
式中:
(1) 取減速傳動的齒數(shù)比;扭矩T=,為齒輪效率。
(2) 取齒寬系數(shù);
(3) 按《機械設計》(西北工大第七版)表10—2查得使用系數(shù) 根據(jù)圖10-8查得 查得所以 即
(4) 根據(jù)《機械設計》西北工大出版社第七版表10-6查得彈性影響系數(shù)
(5) 許用接觸疲勞應力
取s=1,由《機械設計》西工大第七版10-21d查得小齒輪的接觸疲勞強度極限,大齒輪的接觸疲勞強度極限為
(6) 計算應力循環(huán)次數(shù):
由《機械設計》西北工大第七版公式計算兩齒輪的接觸應力循環(huán)次數(shù),設齒輪的壽命為15000小時,由于齒輪的轉(zhuǎn)速較低取100r/min則
(7) 由《機械設計》西北工大第七版圖10-19查得接觸疲勞壽命系數(shù)
所以:
將上述數(shù)據(jù)代入公式得:
3) 計算
(1)錐距:
(2)分度圓直徑
(3)齒寬:
(4)計算分錐角
(5) 計算當量齒數(shù)
4) 校核齒根彎曲疲勞強度:
確定公式內(nèi)各參數(shù)值:
(1)由《機械設計》西北工大第七版圖10-20c查得小齒輪的彎曲疲勞強度極限,大齒輪的彎曲疲勞強度極限
(2)由圖10-18查得彎曲疲勞壽命系數(shù)
(3)計算彎曲疲勞許用應力:
取彎曲疲勞安全系數(shù)s=1.3,由《機械設計》西北工大第七版
(10-12)得:
(4)計算載荷系數(shù)
(5)查取齒行系數(shù)
,,
(6)由《機械設計》第七版表10—5查得
,。
(7)計算大小齒輪并加以比較
計算:
=
取標準值m=1.5
5) 確定錐齒輪的所有結(jié)構尺寸,和零件圖:
名稱
代號
小齒輪
大齒輪
齒數(shù)
齒數(shù)比
2
分錐角
當量圓柱齒輪齒數(shù)
大端模數(shù)
m
1.5
1.5
齒頂高
1.5
1.5
齒根高
1.8
1.8
分度圓直徑
d
齒頂圓直徑
齒根圓直徑
錐距
R
齒寬
b
10
10
齒寬系數(shù)
0.3
0.3
齒根角
齒頂角
頂錐角
根錐角
分度圓弧齒厚
s
圖3-4 小錐