【溫馨提示】壓縮包內(nèi)含CAD圖有下方大圖片預(yù)覽,下拉即可直觀呈現(xiàn)眼前查看、盡收眼底縱觀。打包內(nèi)容里dwg后綴的文件為CAD圖,可編輯,無水印,高清圖,壓縮包內(nèi)文檔可直接點開預(yù)覽,需要原稿請自助充值下載,所見才能所得,請見壓縮包內(nèi)的文件及下方預(yù)覽,請細(xì)心查看有疑問可以咨詢QQ:11970985或197216396
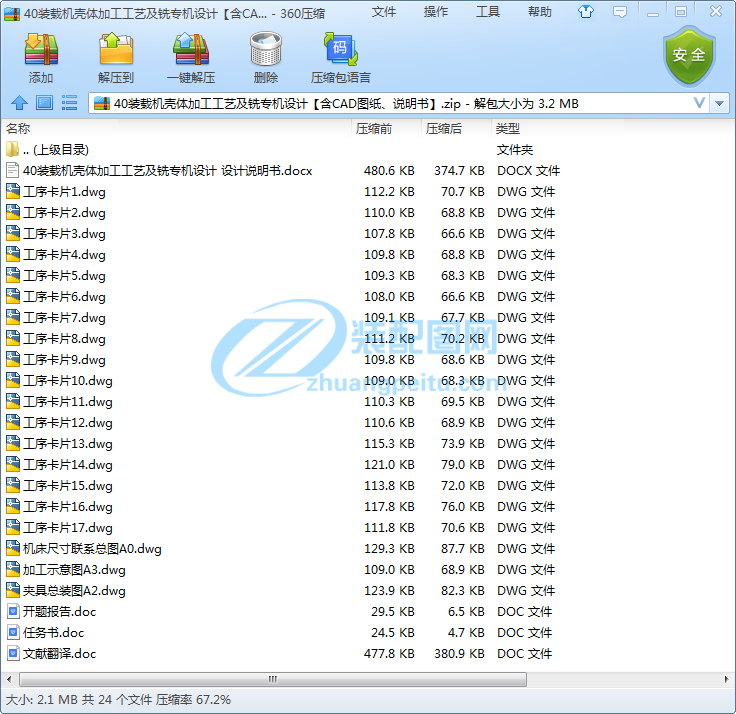
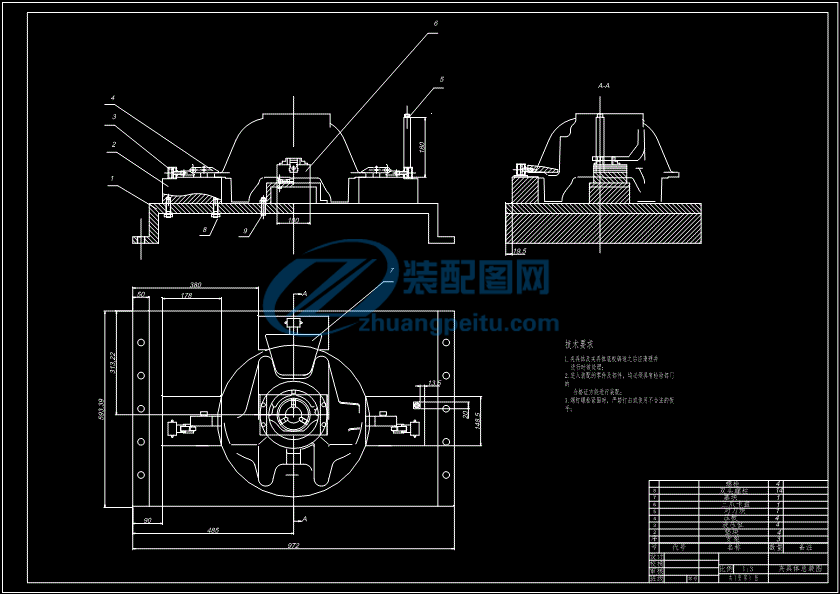
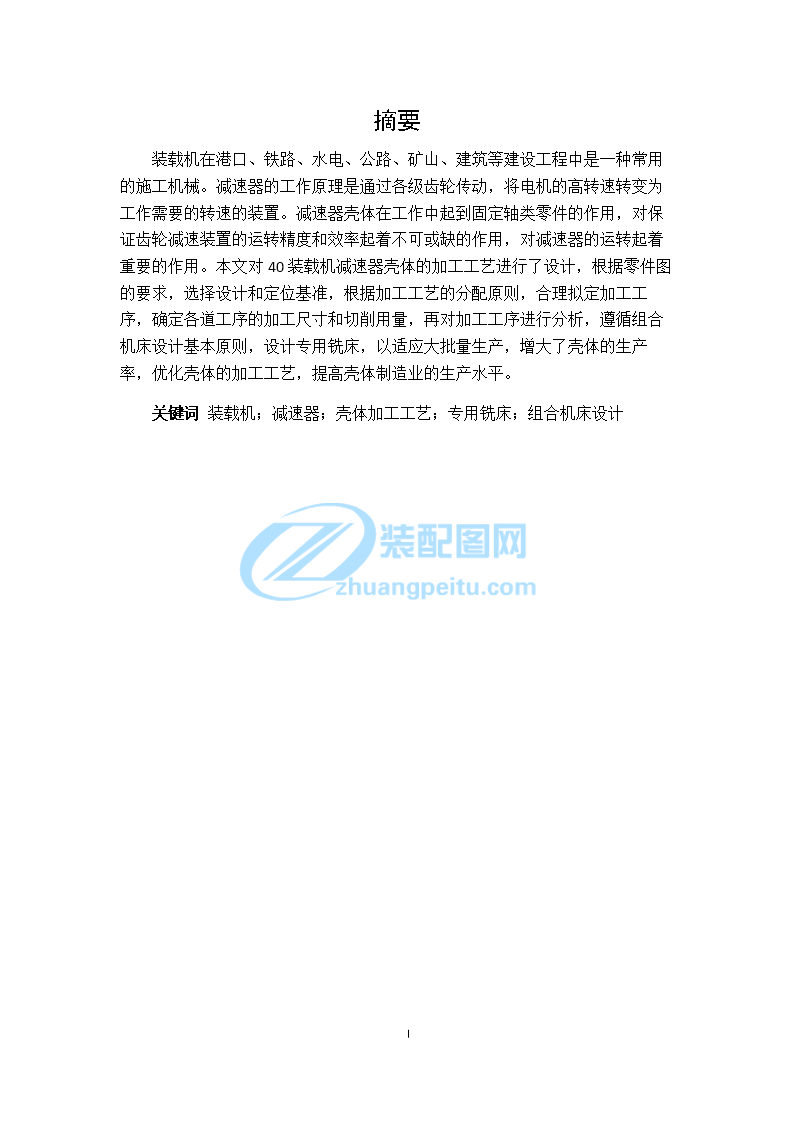

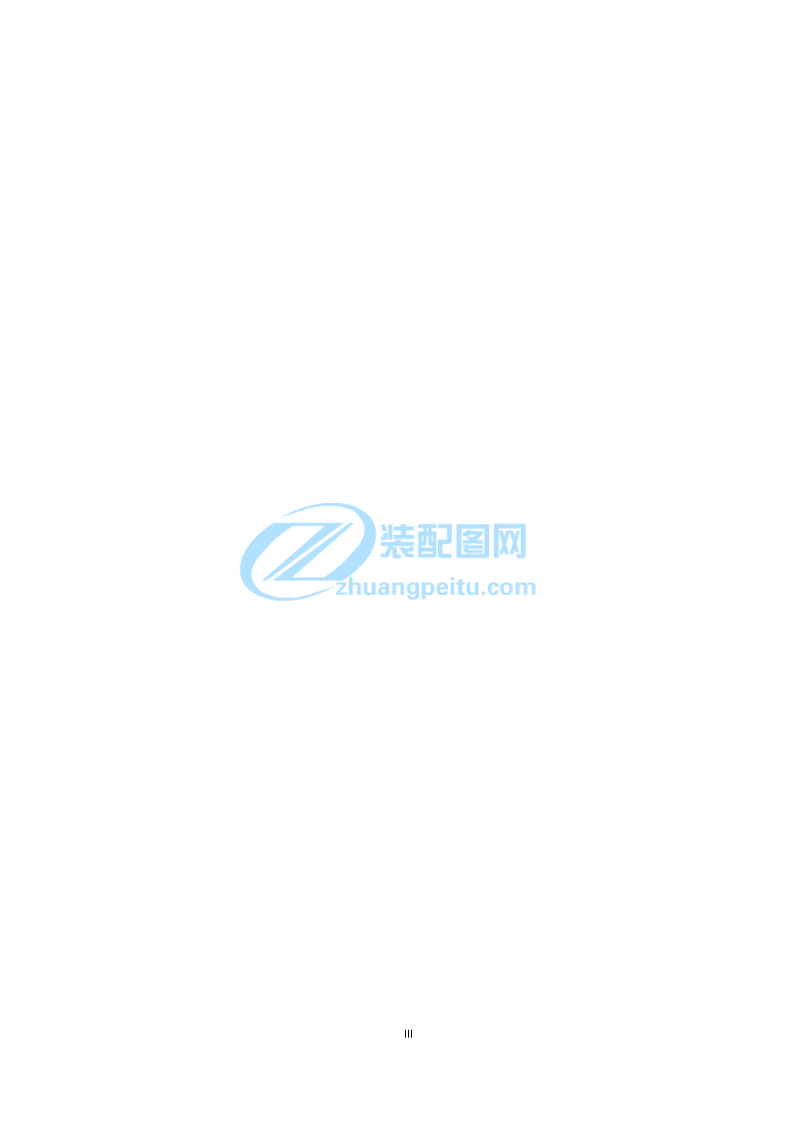
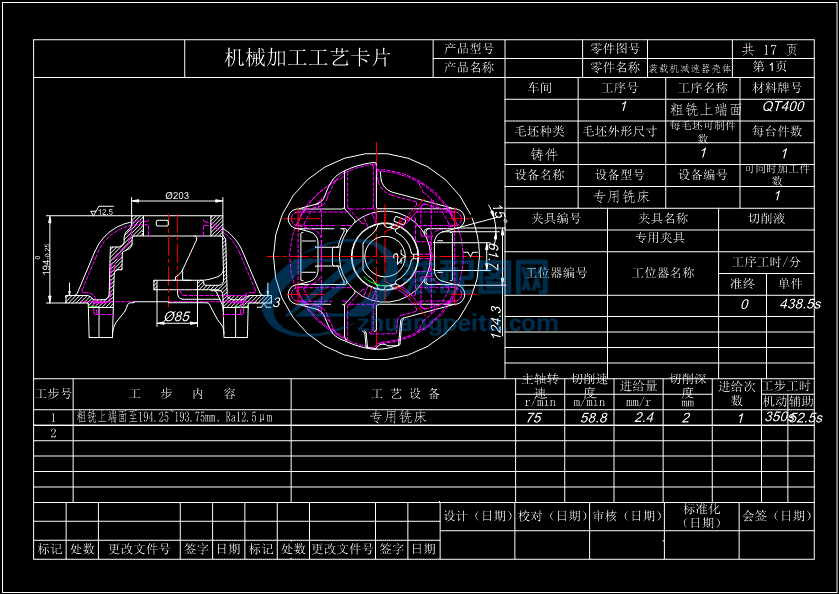
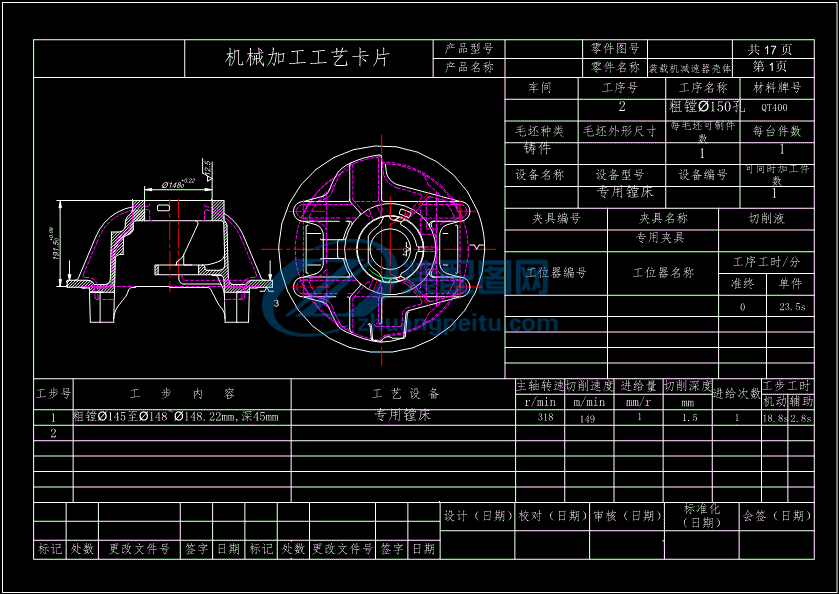
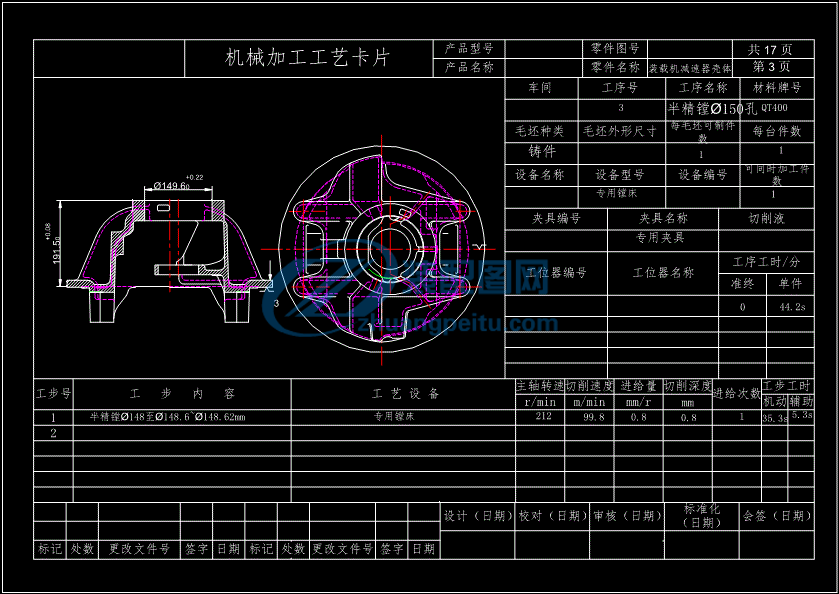
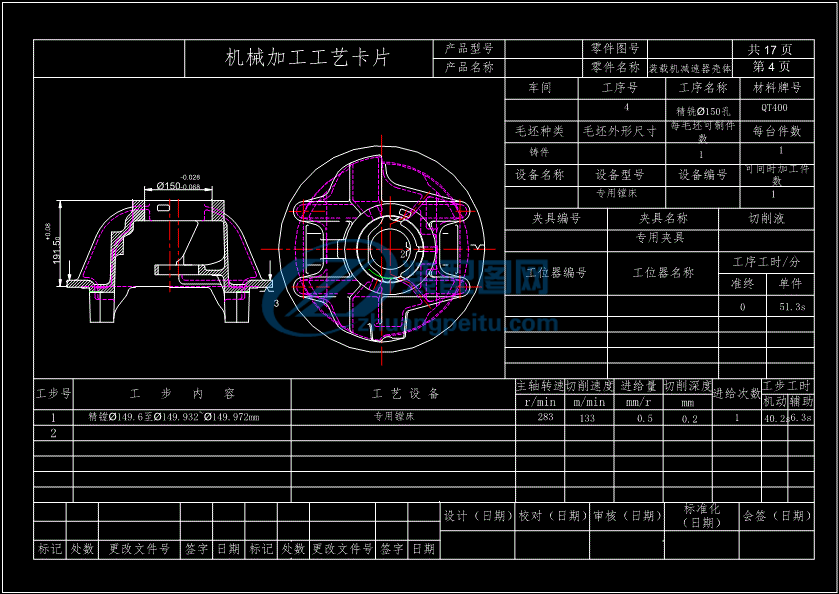
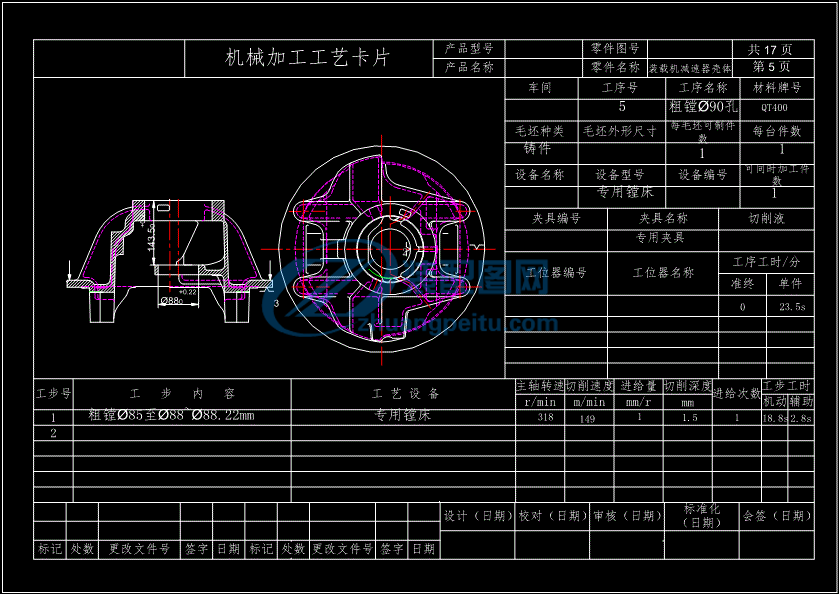
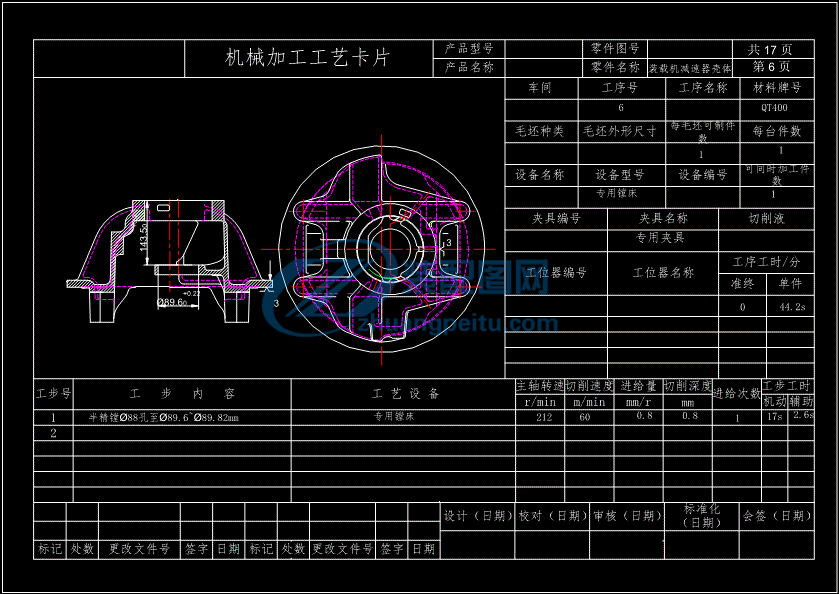
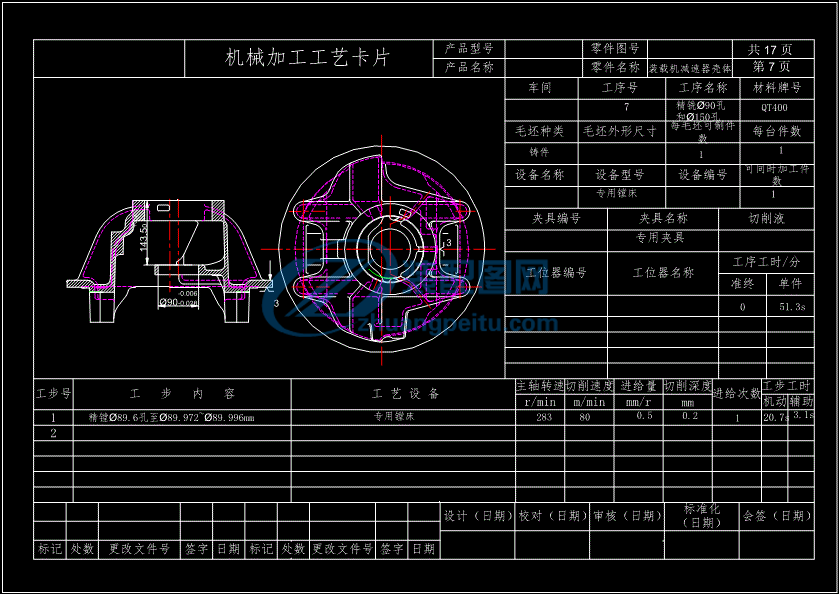
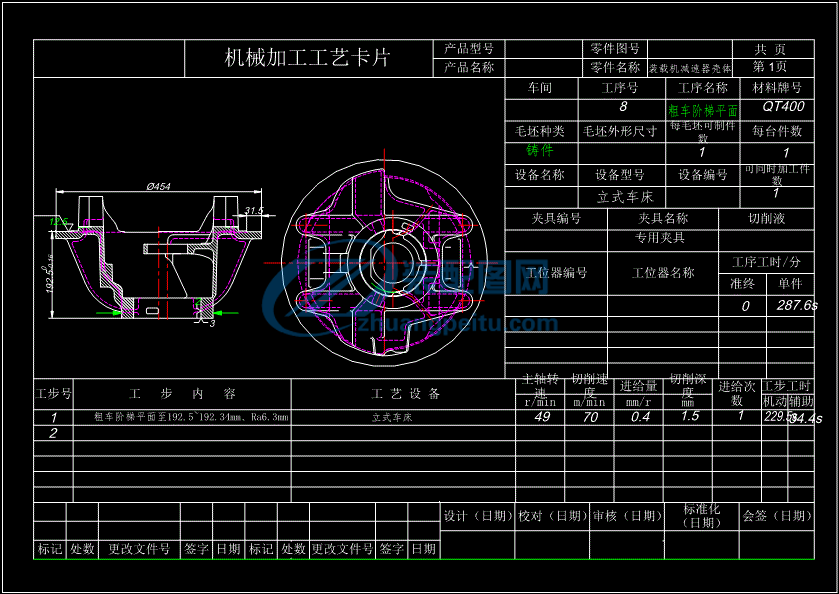
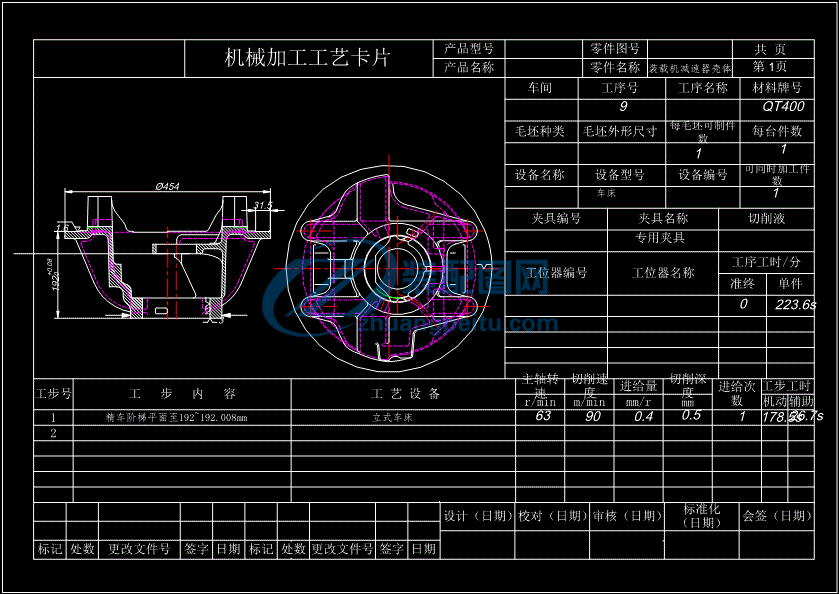
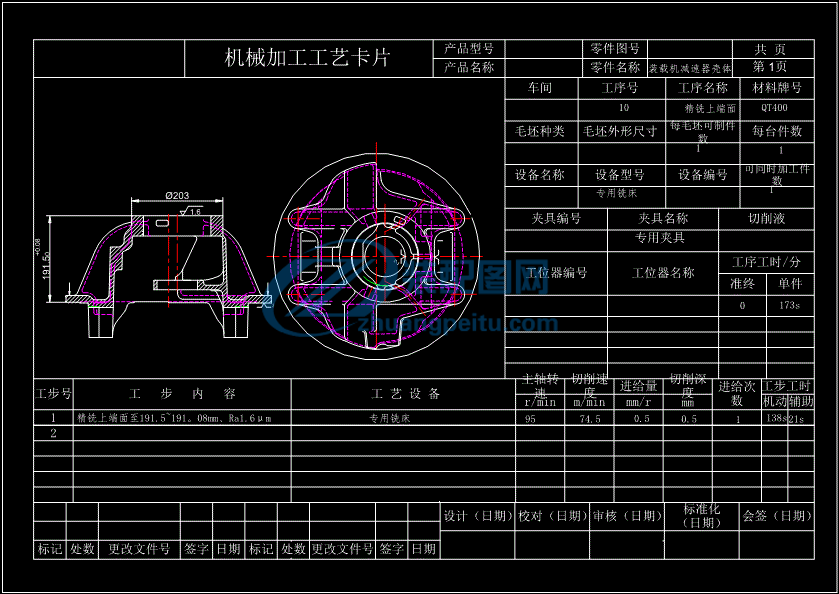
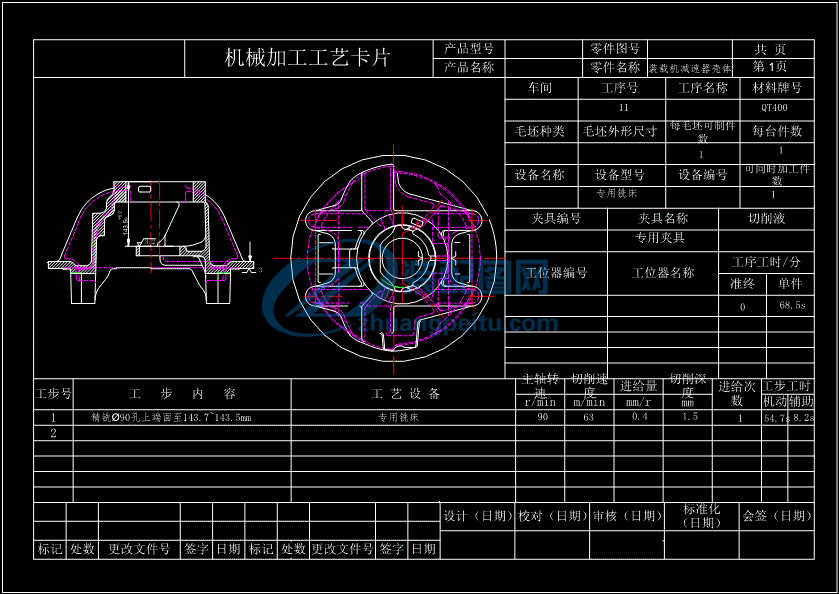
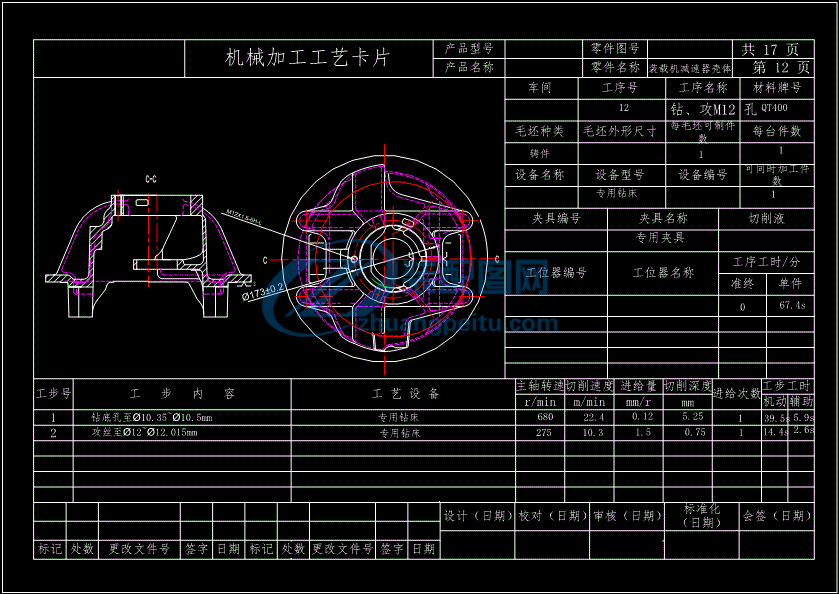
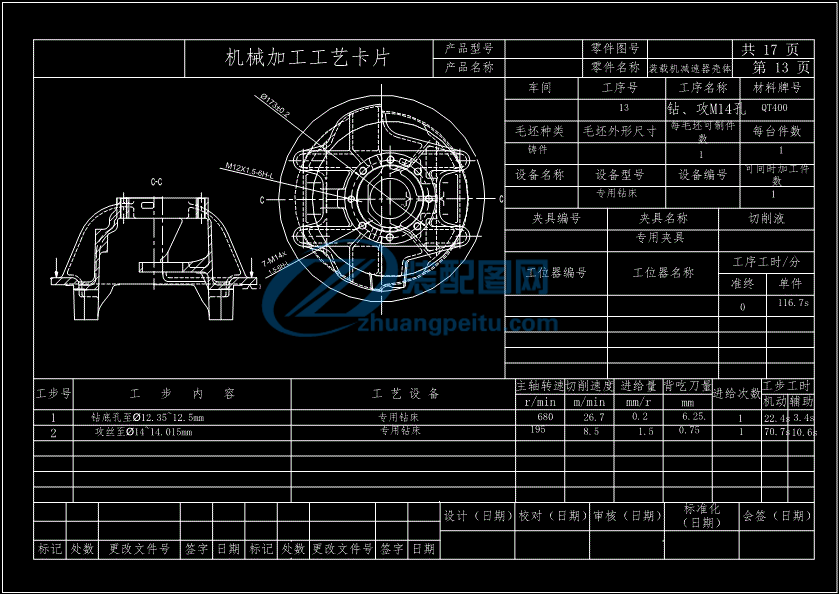
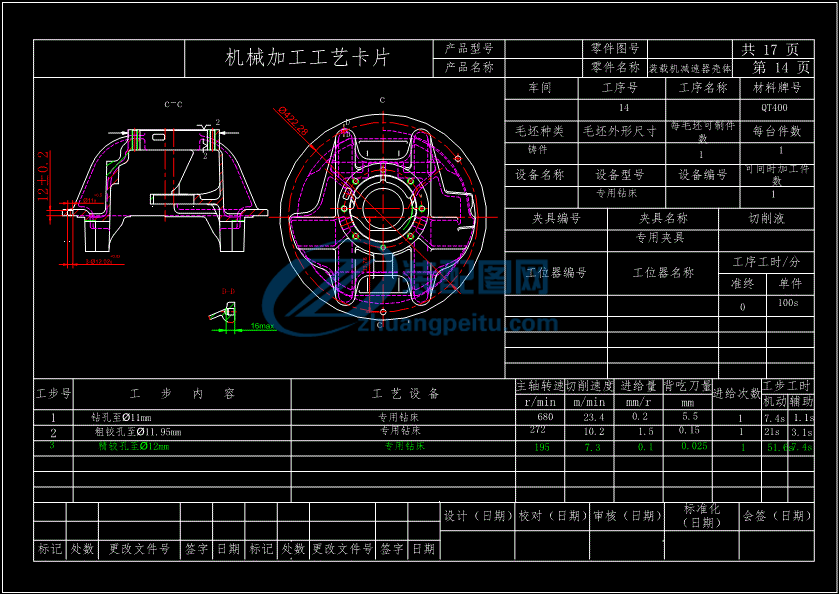
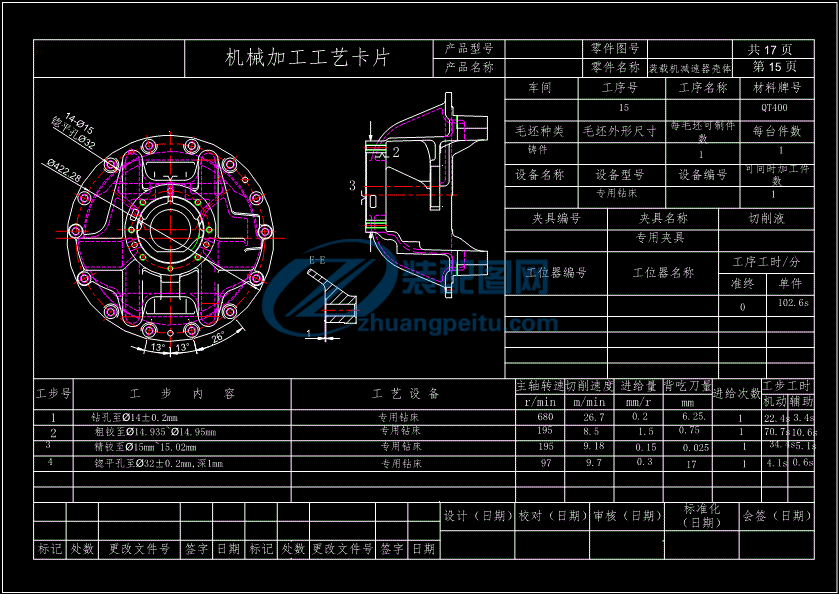
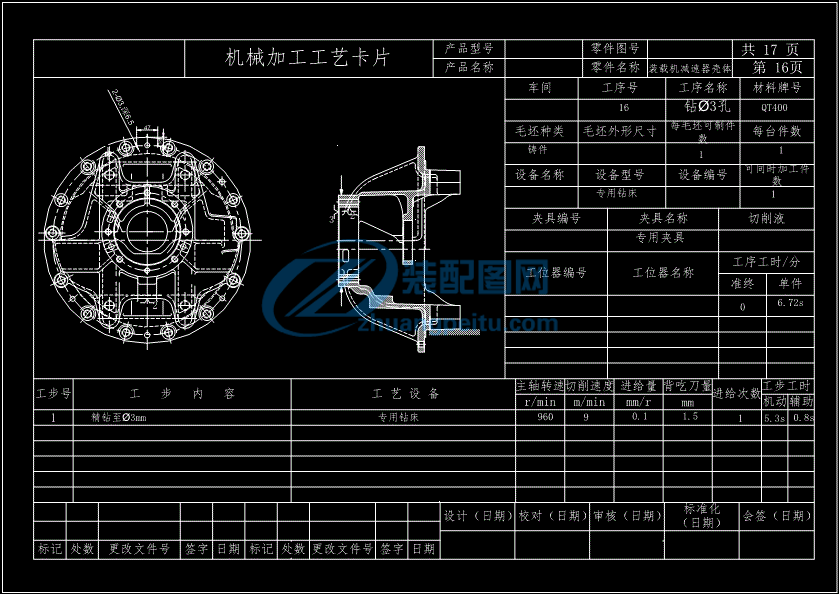

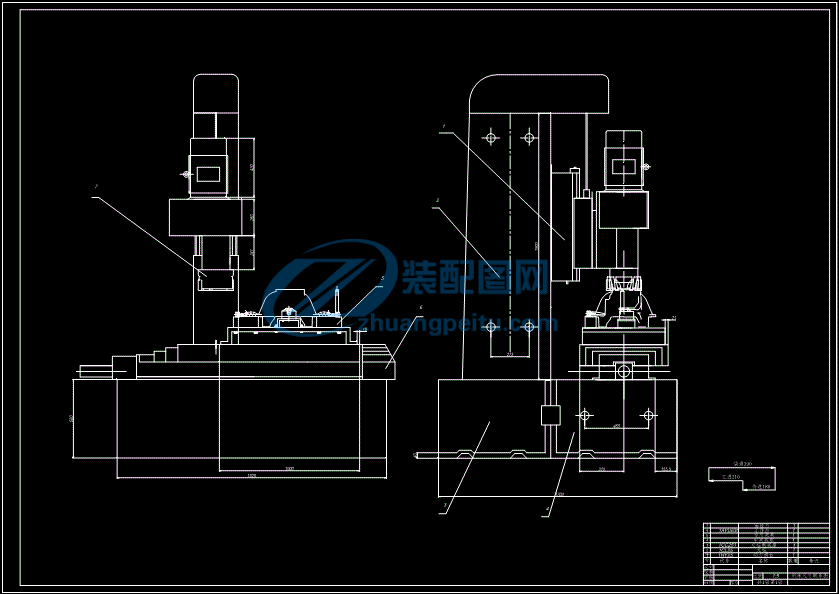
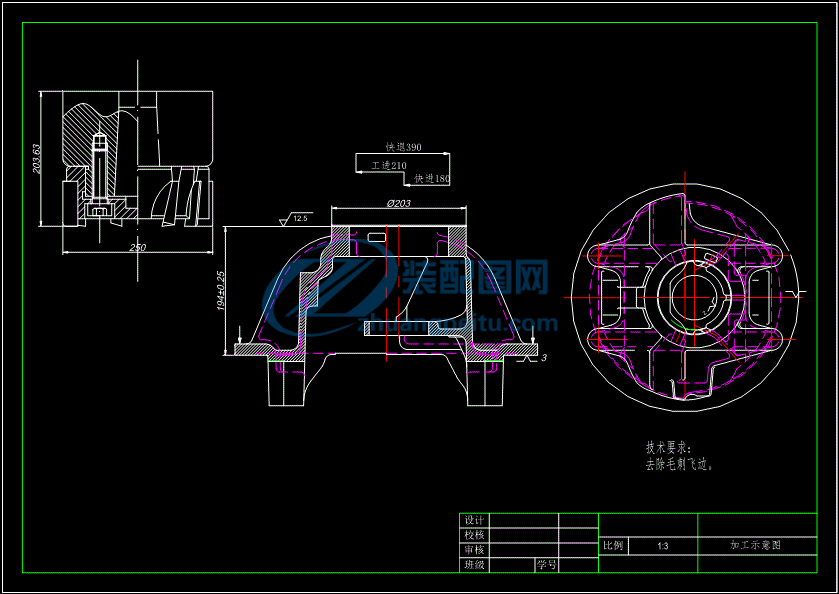
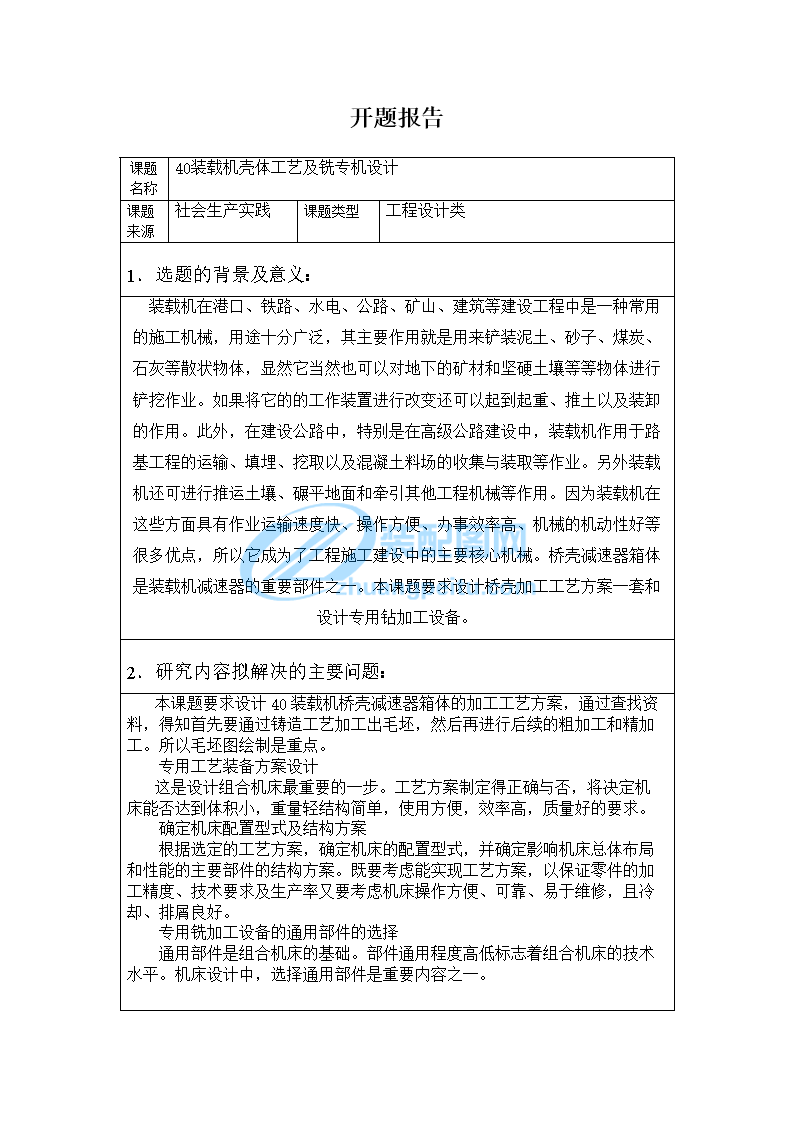
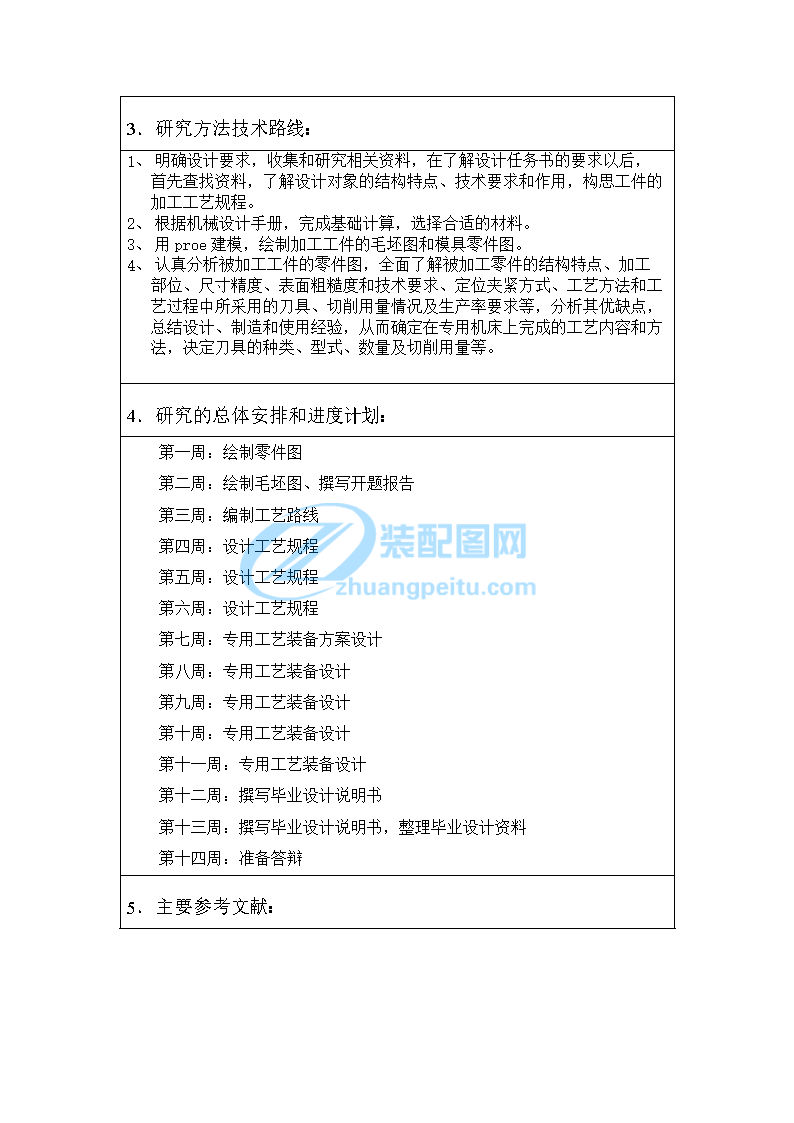
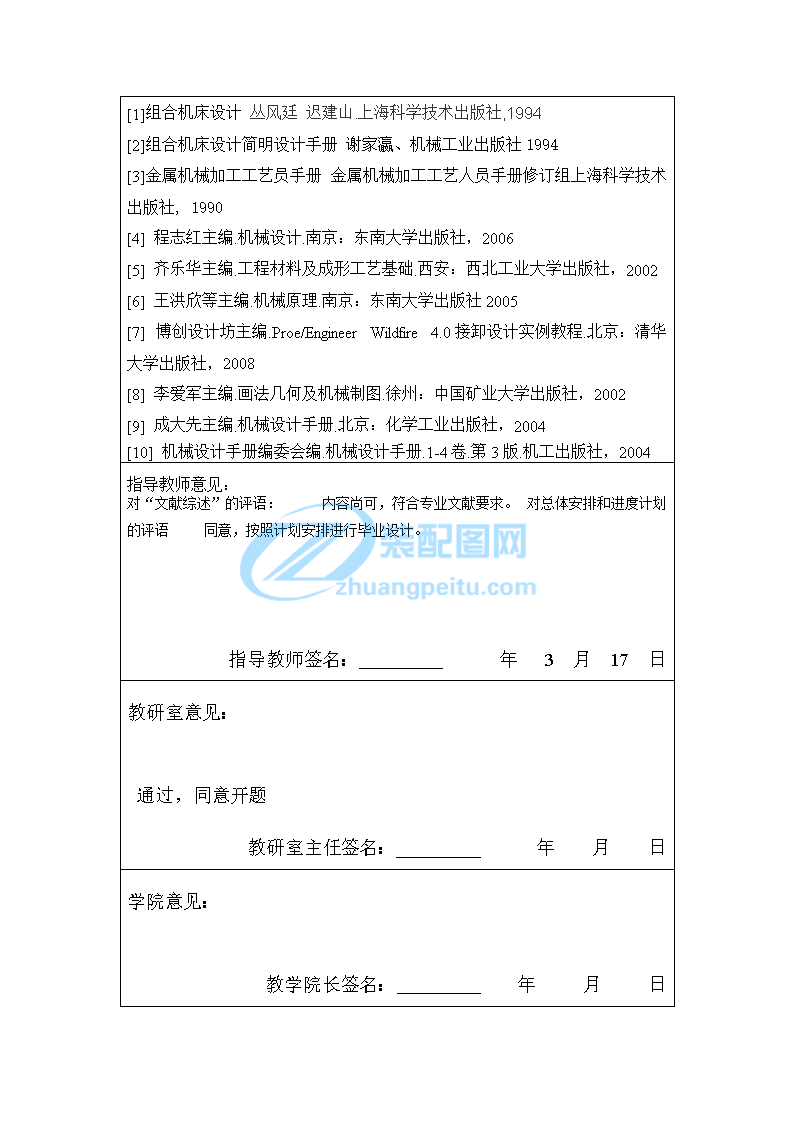
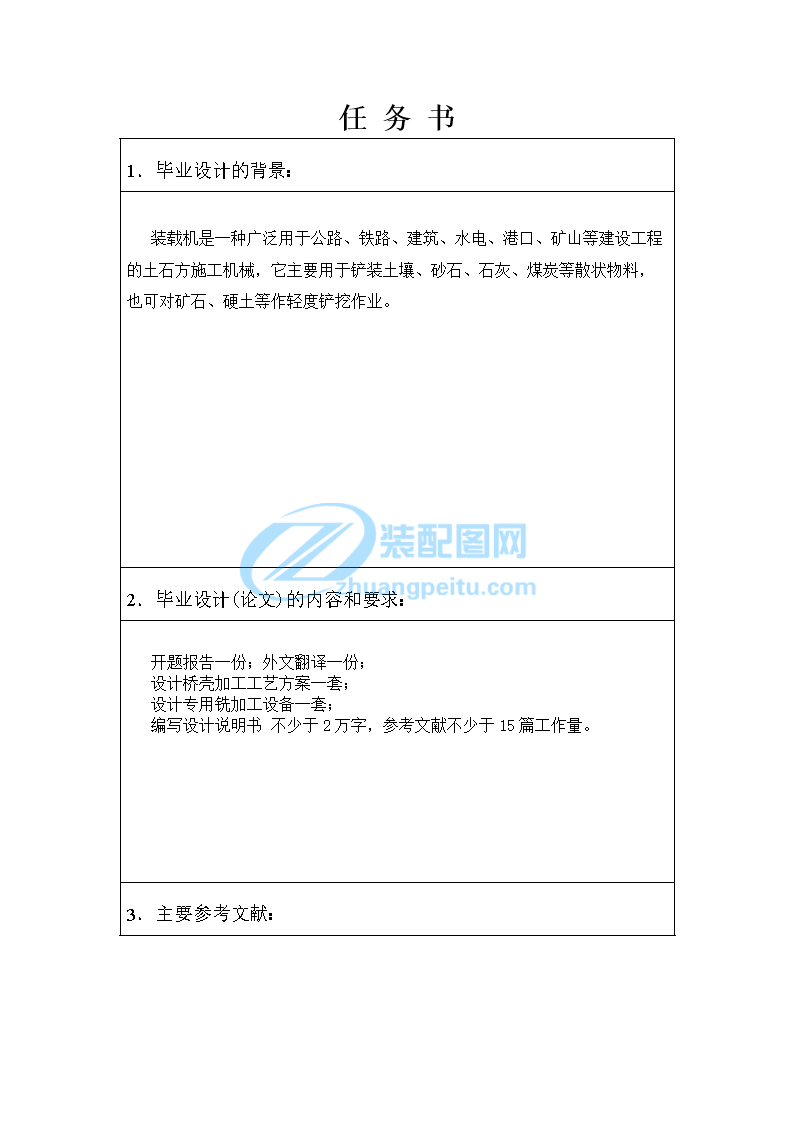
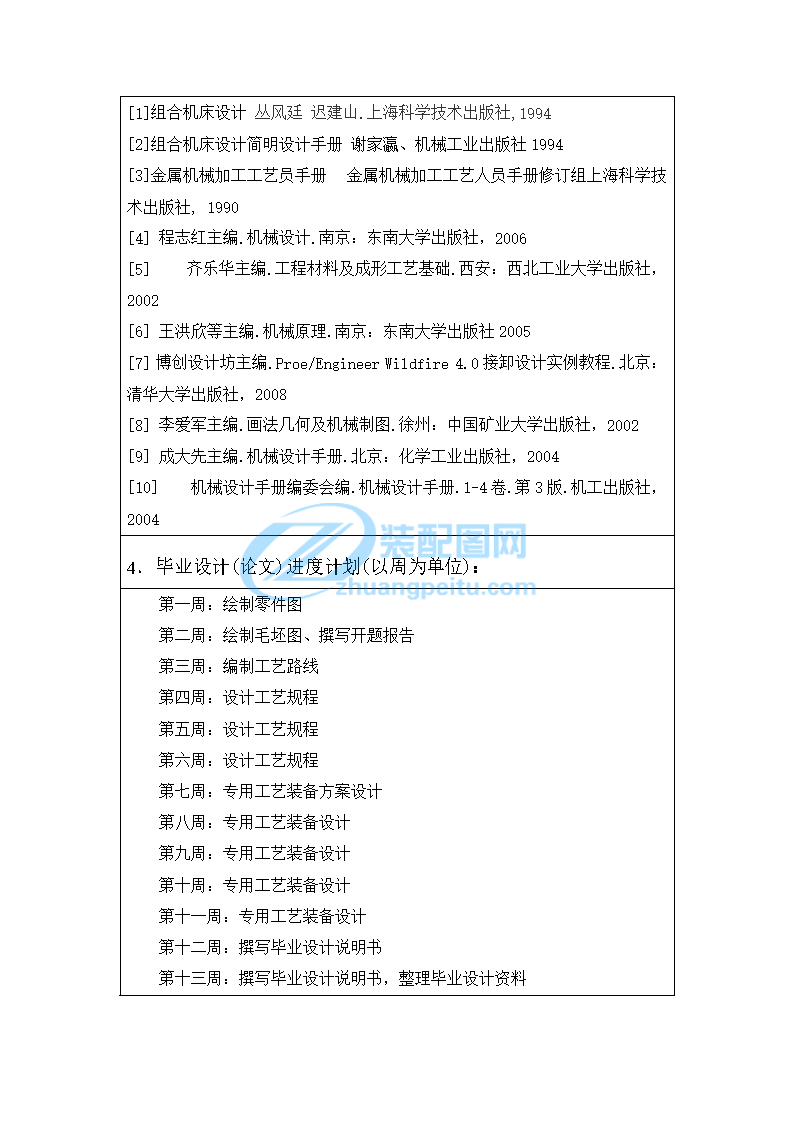

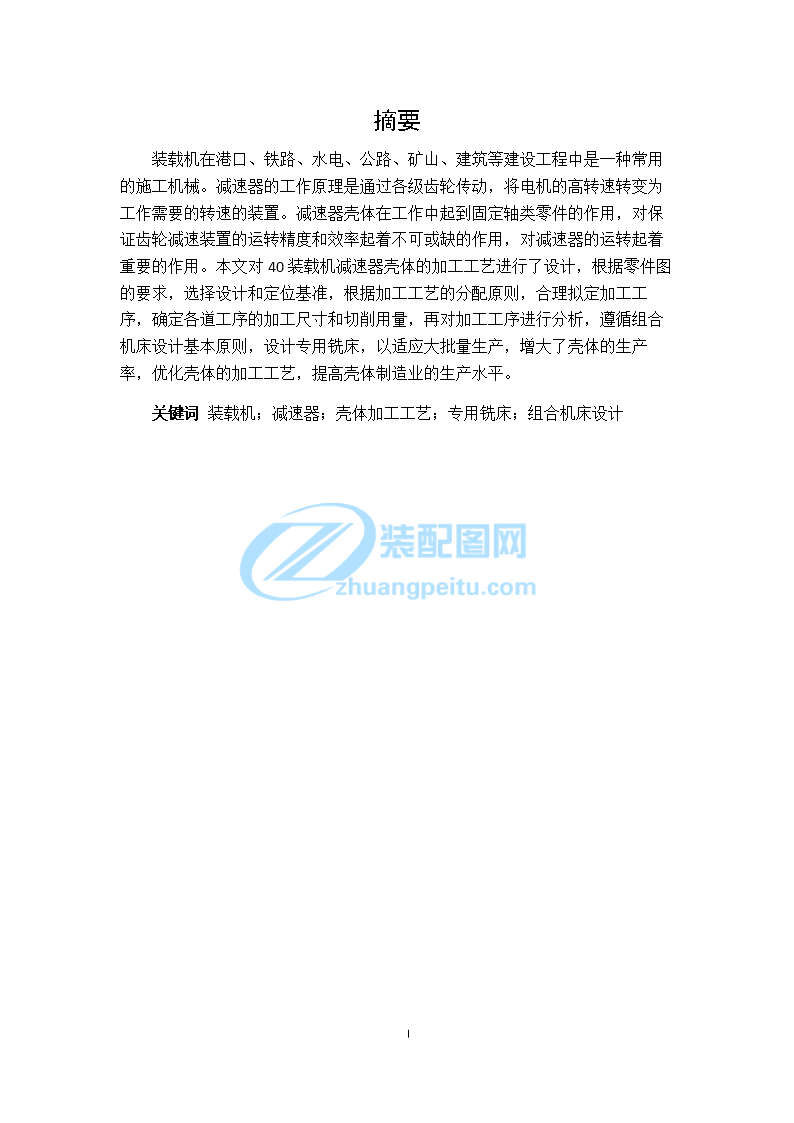
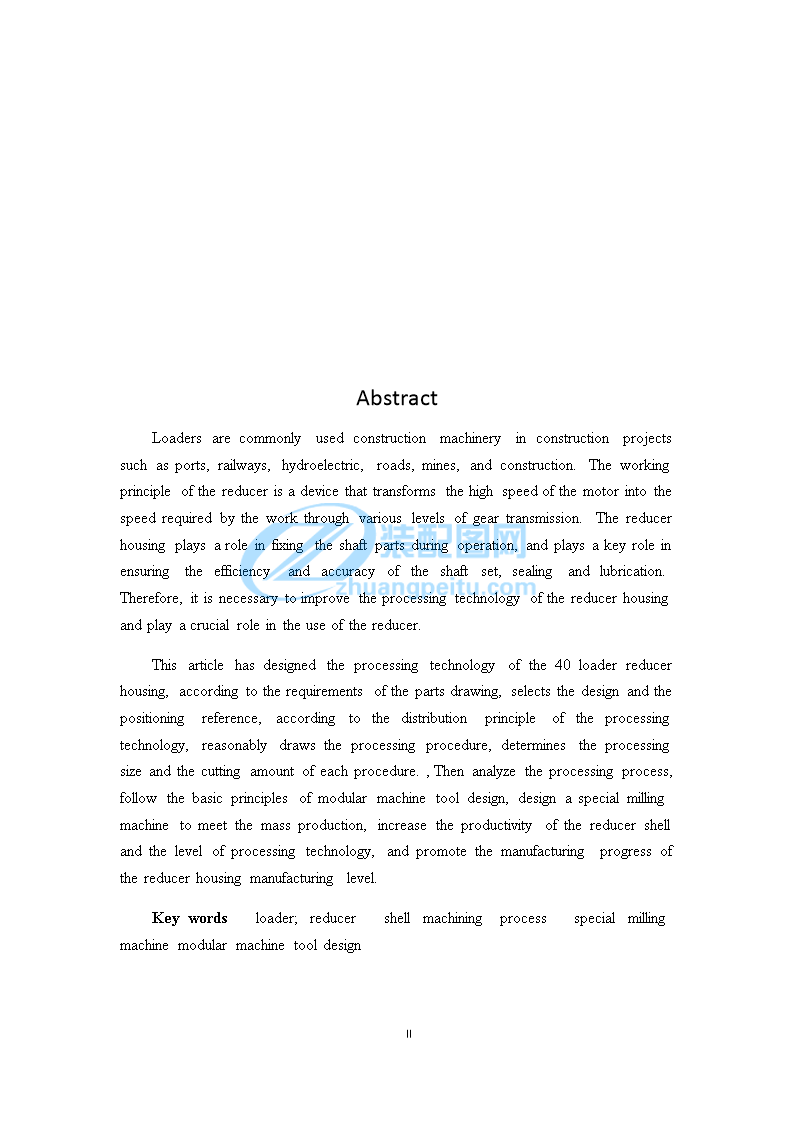
壓縮包內(nèi)含有CAD圖紙和說明書,咨詢Q 197216396 或 11970985
摘要
裝載機在港口、鐵路、水電、公路、礦山、建筑等建設(shè)工程中是一種常用的施工機械。減速器的工作原理是通過各級齒輪傳動,將電機的高轉(zhuǎn)速轉(zhuǎn)變?yōu)楣ぷ餍枰霓D(zhuǎn)速的裝置。減速器殼體在工作中起到固定軸類零件的作用,對保證齒輪減速裝置的運轉(zhuǎn)精度和效率起著不可或缺的作用,對減速器的運轉(zhuǎn)起著重要的作用。本文對40裝載機減速器殼體的加工工藝進行了設(shè)計,根據(jù)零件圖的要求,選擇設(shè)計和定位基準(zhǔn),根據(jù)加工工藝的分配原則,合理擬定加工工序,確定各道工序的加工尺寸和切削用量,再對加工工序進行分析,遵循組合機床設(shè)計基本原則,設(shè)計專用銑床,以適應(yīng)大批量生產(chǎn),增大了殼體的生產(chǎn)率,優(yōu)化殼體的加工工藝,提高殼體制造業(yè)的生產(chǎn)水平。
關(guān)鍵詞 裝載機;減速器;殼體加工工藝;專用銑床;組合機床設(shè)計
Abstract
Loaders are commonly used construction machinery in construction projects such as ports, railways, hydroelectric, roads, mines, and construction. The working principle of the reducer is a device that transforms the high speed of the motor into the speed required by the work through various levels of gear transmission. The reducer housing plays a role in fixing the shaft parts during operation, and plays a key role in ensuring the efficiency and accuracy of the shaft set, sealing and lubrication. Therefore, it is necessary to improve the processing technology of the reducer housing and play a crucial role in the use of the reducer.
This article has designed the processing technology of the 40 loader reducer housing, according to the requirements of the parts drawing, selects the design and the positioning reference, according to the distribution principle of the processing technology, reasonably draws the processing procedure, determines the processing size and the cutting amount of each procedure. , Then analyze the processing process, follow the basic principles of modular machine tool design, design a special milling machine to meet the mass production, increase the productivity of the reducer shell and the level of processing technology, and promote the manufacturing progress of the reducer housing manufacturing level.
Key words loader; reducer shell machining process special milling machine modular machine tool design
III
目錄
摘要 I
Abstract II
目錄 III
1緒論 1
1.1課題的研究背景及意義 1
1.2組合機床發(fā)展現(xiàn)狀 1
1.3本文主要研究內(nèi)容 2
2減速器箱體的結(jié)構(gòu)和工藝性分析 3
2.1箱體的結(jié)構(gòu)性分析 3
2.2箱體的毛坯種類 3
2.3箱體的工藝性分析 4
3鑄造工藝設(shè)計 5
3.1鑄造工藝分析 5
3.1.1零件圖分析 5
3.1.2零件的技術(shù)要求 5
3.1.3鑄件結(jié)構(gòu)工藝性 5
3.2鑄造工藝方案的確定 5
3.2.1?鑄造方法的確定? 5
3.2.2?澆注位置的確定? 5
3.2.3分型面的選擇 6
3.3加工工藝參數(shù) 6
3.3.1加工余量的確定 6
3.3.2鑄造圓角的確定 8
3.3.3鑄造收縮率 8
3.4澆注系統(tǒng)的設(shè)計 8
3.4.1澆注位置的確定 8
3.4.2各個澆道截面積的計算 8
4減速器殼體加工工藝設(shè)計 10
4.1加工工藝的設(shè)計 10
4.1.1設(shè)計原則 10
4.1.2擬定加工工藝路線 10
4.2選擇定位基準(zhǔn) 10
4.2.1定位基準(zhǔn)選擇原則 10
4.2.2表面加工方法的選擇 11
4.2.3加工階段的劃分 11
4.2.4加工順序安排 11
4.3加工工藝路線的擬定 12
4.4確定加工余量和工序尺寸 12
4.4.1重要平面的加工余量及工序尺寸的確定 12
4.4.2其他加工工序尺寸及加工余量 13
4.4.3確定切削用量及時間定額 14
5、 機床夾具設(shè)計 25
5.1分析原始資料 25
5.2擬定夾具機構(gòu)方案,繪制夾具結(jié)構(gòu)草圖 26
5.2.1確定夾具類型 26
5.2.2擬定定位以及夾緊方案 26
5.3選擇、設(shè)計定位裝置的結(jié)構(gòu),確定主要尺寸并計算定位誤差 26
5.4選擇、設(shè)計夾緊裝置并驗算夾緊力 27
5.5確定對刀裝置 28
5.6確定其他裝置結(jié)構(gòu)、夾具體、并完成夾具總體設(shè)計 29
5.7擬定夾具總圖的主要技術(shù)要求 29
6專用銑床的設(shè)計 30
6.1組合機床的概述 30
6.2組合機床設(shè)計的基本內(nèi)容 30
6.2.1被加工零件的工序分析 30
6.2.2總體方案設(shè)計 30
6.2.4組合機床設(shè)計——三圖一卡設(shè)計 32
6.2.5移動工作臺的設(shè)計 32
6.3零件分析 32
6.4結(jié)構(gòu)方案和定位方案的確定 33
6.5選擇定位基準(zhǔn)原則和因注意的問題 33
6.5.1設(shè)計基準(zhǔn)要求 33
6.5.2定位基準(zhǔn)的要求 33
6.5.3確定壓板位置時應(yīng)注意的問題 34
6.6工藝分析 34
6.6.1加工精度要求 34
6.6.2被加工零件大小形狀特點,加工部位特點要求 34
6.7確定機床的配置型式 34
6.8組合機床的切削用量 35
6.8.1組合機床切削用量的選擇特點 35
6.8.2確定切削用量應(yīng)注意的問題 35
6.10組合機床總體方案設(shè)計 35
6.10.1被加工零件的工序圖 35
6.10.2加工示意圖 36
6.10.3生產(chǎn)率計算卡 36
6.10.4機床尺寸聯(lián)系總圖 37
總結(jié) 38
致謝 39
參考文獻 40
VII
1緒論
1.1課題的研究背景及意義
裝載機在港口、鐵路、水電、公路、礦山、建筑等建設(shè)工程中是一種常用的施工機械,用途十分廣泛,其主要作用就是用來鏟裝泥土、砂子、煤炭、石灰等散狀物體,顯然它當(dāng)然也可以對地下的礦材和堅硬土壤等等物體進行鏟挖作業(yè)。如果將它的的工作裝置進行改變還可以起到起重、推土以及裝卸的作用。此外,在建設(shè)公路中,特別是在高級公路建設(shè)中,裝載機作用于路基工程的運輸、填埋、挖取以及混凝土料場的收集與裝取等作業(yè)。另外裝載機還可進行推運土壤、碾平地面和牽引其他工程機械等作用。因為裝載機在這些方面具有作業(yè)運輸速度快、操作方便、辦事效率高、機械的機動性好等很多優(yōu)點,所以它成為了工程施工建設(shè)中的主要核心機械。橋殼減速器箱體是裝載機減速器的重要部件之一。本課題要求設(shè)計橋殼加工工藝方案一套和設(shè)計專用銑加工設(shè)備一套。
減速器的工作原理是通過各級齒輪傳動,將電機的高轉(zhuǎn)速轉(zhuǎn)變?yōu)楣ぷ餍枰霓D(zhuǎn)速的裝置。減速器殼體在工作中起到固定軸類零件的作用,對保證齒輪減速裝置的運轉(zhuǎn)精度和效率起著不可或缺的作用,對減速器的運轉(zhuǎn)起著重要的作用。
1.2組合機床發(fā)展現(xiàn)狀
在中國,組合機床的發(fā)展有了二十幾年的歷史,具有良好的科研和生產(chǎn)的基礎(chǔ),在許多行業(yè)之中得到很好的應(yīng)用,組合機床是目前機械制造業(yè)中實現(xiàn)產(chǎn)品更新?lián)Q代,進行技術(shù)創(chuàng)新,改善加工工藝,提高生產(chǎn)率不可缺少的裝備之一。組合機床是具有工序高度集中,集機電一體化程度較高的工藝設(shè)備。它的特點是工序集中、高效、高質(zhì)、經(jīng)濟實用。故被廣泛應(yīng)用于各類制造業(yè)中。我國傳統(tǒng)的組合機床一般采用機、電、液壓、氣控制,組合機床的加工對象一般是需要大批量生產(chǎn)的工件??梢栽谕粋€機床上完成許多道工序。組合機床種類很多,根據(jù)加工需要,設(shè)計不同的組合機床,將需要的工序集中到一臺機床上。隨著科學(xué)技術(shù)的發(fā)展,柔性組合機床的出現(xiàn),極大地提高了勞動生產(chǎn)率,能隨意改變工作循環(huán),控制和驅(qū)動系統(tǒng)。此外,最近幾年,加工中心和數(shù)控組合機床等裝備在機床行業(yè)中越來越重要。
組合機床是一種技術(shù)含量和綜合性很高的加工裝備,組合機床根據(jù)加工的需要來設(shè)計,涉及到加工工藝、加工方式、輔助加工、刀具、控制、裝配等技術(shù)。這些都需要很高的技術(shù)要求,我國在這方面的技術(shù)發(fā)展相對于發(fā)達國家還比較落后,國內(nèi)一些技術(shù)含量很高的組合機床都需要從國外進口,從而使得產(chǎn)品生產(chǎn)成本變高。需要決定市場,而市場決定技術(shù)。我們要不斷創(chuàng)新,將機床實現(xiàn)從“剛性”到“柔性”的轉(zhuǎn)變,更好的滿足生產(chǎn)需要。所以今后很長時間,組合機床技術(shù)裝備的高速度、高精度、柔性化和通信技術(shù)等的應(yīng)用將是我國組合機床行業(yè)發(fā)展的主要方向。
1.3本文的研究內(nèi)容
作者首先通過查找相關(guān)資料選擇毛坯的鑄造方法,選擇定位基準(zhǔn)和設(shè)計基準(zhǔn)。然后根據(jù)工藝路線擬定原則,擬定加工工藝路線,查找資料確定加工余量,確定每道工序的工序尺寸和切削參數(shù),繪制工序卡片。最后,根據(jù)工序要求和加工特點,結(jié)合加工工序的需要,設(shè)計一臺專用銑床,提高殼體加工的精度和效率。
2減速器箱體的結(jié)構(gòu)和工藝性分析
2.1箱體的結(jié)構(gòu)性分析
圖2-1減速器殼體零件圖
(1) 箱體的需要加工的地方一般是平面和孔,結(jié)構(gòu)較復(fù)雜。?
(2) 當(dāng)箱體選擇鑄造毛坯時,鑄造好后需要經(jīng)過時效處理,消除內(nèi)應(yīng)力。?
(3) 對于孔直徑大于60mm的孔,一般選擇鏜削,較小的孔一般選擇鉆、擴、鉸。?
(4) 對于精度要求比較高的孔,要分粗加工,半精加工,精加工。?
(5) 用塞規(guī)和千分尺可以檢測孔的精度。?
2.2箱體的毛坯種類
毛坯的鑄造時工件制造過程的一個重要部分,在制造毛坯時,考慮零件的技術(shù)要求、生產(chǎn)綱領(lǐng)、結(jié)構(gòu)特點和材料的力學(xué)性能等,能夠方便的確定毛坯的種類、制造方法、形狀和尺寸,以提高鑄件的經(jīng)濟性和加工的經(jīng)濟性。
常見的毛坯的制造方法有鑄造、鍛造和沖壓成型等,根據(jù)零件的加工需要和材料來選擇合理的制造方式。結(jié)構(gòu)較復(fù)雜的零件一般選擇鑄造的方式,結(jié)構(gòu)簡單的選擇鍛造的方式。在大批量生產(chǎn)中,模鍛和鑄造都是比較好的方式。
2.3箱體的工藝性分析
本殼體加工保證要加工孔的孔軸配合度為P7和M6,同軸度為0.03mm,表面粗糙度為Ra小于3.2um,垂直度為0.028mm。其它孔的表面粗糙度為Ra小于12.5um。上端面表面粗糙度為Ra小于3.2um,箱體表面粗糙度為Ra小于12.5um。
設(shè)計的減速器殼體選用切削性能較好,抗振性能較好,經(jīng)濟性較好,易成型和耐磨的球墨鑄鐵(QT400),所以在鑄造時工件的機械加工余量可以適當(dāng)減少。
加工箱體的主要平面一般都被作為加工中的設(shè)計基準(zhǔn)和定位基準(zhǔn),避免箱體與機器夾裝時的剛性接觸,影響加工的定位精度。
3鑄造工藝設(shè)計
3.1鑄造工藝分析
3.1.1零件圖分析
被加工的零件的零件圖要求清晰準(zhǔn)確,且有完整的尺寸標(biāo)注,以便于分析零件圖,判斷零件的結(jié)構(gòu)是否符合鑄造要求。零件圖的分析要注意下面兩個問題:? ???
(1) 分析零件符不符合鑄造的要求。? ???
(2) 考慮鑄造過程中零件可能會出現(xiàn)的缺陷。
?零件材料:QT-400
3.1.2零件的技術(shù)要求
鑄造時,零件的重要加工表面,不要出現(xiàn)縮孔,夾渣,縮松等缺陷。
3.1.3鑄件結(jié)構(gòu)工藝性
鑄件壁厚不小于最小壁厚5-6mm
3.2鑄造工藝方案的確定
3.2.1?鑄造方法的確定? ????
鑄造方法包括:造型方法、造芯方法、鑄造方法及鑄型種類的選擇????
(1) 造型方法、造芯方法的選擇? ???
?根據(jù)手工造型和機器造型的特點,選擇手工造型????
(2) 鑄造方法的選擇? ????
根據(jù)零件的各參數(shù),選擇砂型鑄造。????
(3) 鑄型種類的選擇? ????
根據(jù)鑄型的特點和應(yīng)用情況選用自硬砂。?
3.2.2?澆注位置的確定?
澆注位置選擇的原則:? ???
(1) 防止?jié)沧⑦^程中,液態(tài)金屬中的氣體和熔渣上浮,鑄件的重要平面和加工質(zhì)量要求高的面,一般都被置于鑄型的底部或側(cè)部;
(2) 防止鑄件的大平面出現(xiàn)缺陷,一般都朝下;
(3) 薄壁面積比較大的鑄件,一般將薄壁部分置于下部或側(cè)部;
(4) 在有些位置要設(shè)置冒口補縮?
所以澆注位置選擇在殼體頂部。
3.2.3分型面的選擇
分型面的選擇原則:
(1) 鑄件的分型面一般選擇鑄件的最大平面上,盡量選擇平面。 ?
(2) 盡可能只有一個分型面。 ?
(3) 型芯和活塊的數(shù)量盡可能少。 ?
(4) 鑄件的大部分甚至全部都最好在一個沙箱內(nèi),而且盡可能的將重要加工面和大平面置于下部。
由此,該零件分型面選取如圖3-1中G-G
圖3-1分型面位置圖
3.3加工工藝參數(shù)
3.3.1加工余量的確定
根據(jù)造型方法、材料類型進行查詢表3-1,查得加工余量等級為11-14,取加工余量等級為12
公差等級 CT
方法
鑄件材料
鋼
灰鑄鐵
球墨鑄鐵
可鍛鑄鐵
銅合金
鋅合金
砂型鑄造手工造型
11-14
11-14
11-14
11-14
10-13
10-13
砂型鑄造機器造型和殼型
8-12
8-12
8-12
8-12
8-10
8-10
金屬型鑄造(重力鑄造、低壓鑄造)
--
8-10
8-10
8-10
8-10
7-9
表3-1造型方法、材料公差等級表
根據(jù)零件基本尺寸、加工余量等級。鑄件尺寸為基本公差數(shù)值為10
根據(jù)表3-2和表3-3。取鑄件的加工余量等級為F,查得上端面機械加工余量為2.5mm,?90孔上端面機械加工余量為1.5mm。
表3-2毛坯鑄件的典型的機械加工余量等級
方法
要求的機械加工余量等級
鑄件材料
鋼
灰鑄鐵
球墨鑄鐵
可鍛鑄鐵
砂型鑄造手工造型
G-K
F-H
F-H
F-H
砂型鑄造機器造型和殼型
F-H
E-G
E-G
E-G
金屬型造型
-
D-F
D-F
D-F
表3-3鑄件的E~H級機械加工余量(RMA)
最大尺寸
要求的機械加工余量等級
大于
至
E
F
G
H
40
0.4
0.5
0.5
0.7
40
63
0.4
0.5
0.7
1
63
100
0.7
1
1.4
2
100
160
1.1
1.5
2.2
3
160
250
1.4
2
2.8
4
250
400
1.4
2.5
3.5
5
400
630
2.2
3
4
6
3.3.2鑄造圓角的確定
根據(jù)鑄造方法和材料,最小鑄造圓角半徑為3
3.3.3鑄造收縮率
取1%
3.4澆注系統(tǒng)的設(shè)計
3.4.1澆注位置的確定
(1)澆注位置的選擇原則:
a)鑄件的重要加工面應(yīng)處于型腔底面或側(cè)面;
b)鑄件的大平面應(yīng)盡量朝下;
c)鑄件的薄壁部分應(yīng)放在鑄件的下部或側(cè)面;
d)對于材料收縮大、壁厚不均勻的鑄件,應(yīng)使厚度大的部分朝上或置于分型面的附近,以利于安放冒口對該處補縮。
根據(jù)內(nèi)澆道的位置選擇垂直澆注。
(2)澆注系統(tǒng)的類型選擇
根據(jù)各澆注系統(tǒng)的特點及鑄件的大小選用封閉式澆注系統(tǒng)。
3.4.2各個澆道截面積的計算
用奧贊(Osann)公式計算每個內(nèi)澆道截面積有
式中
m-流過澆注系統(tǒng)最小橫截面積的鑄鐵金屬液總質(zhì)量(kg);
-金屬材料密度();
τ-澆注時間(s);
μ-流量因數(shù)(量綱為1);
可用澆口杯中液面到內(nèi)澆道中心的距離H。計算。
3.4.3冒口的設(shè)計
(1)冒口必須提供足夠的金屬液,補償鑄件凝固的體收縮,條件應(yīng)有:
式中:-冒口體積
-鑄件體積
-型壁移動所擴大的體積
-體收縮率
-冒口補縮效率。
(2)冒口的計算方法
常用冒口計算方法的有比例法、模數(shù)法和補縮液量法。這里我們選用比
例法。根據(jù)本鑄件的形狀和加工冒口。令鑄件冒口處的壁厚T=45.5mm,減速箱體為大批量生產(chǎn),并且采用上下兩箱造型,采用頂注式澆注系統(tǒng),上面設(shè)兩個冒口,澆注的時候重要的加工面朝下,由于鑄件的上端面易產(chǎn)生氣孔,砂眼。為了提高鑄造精度,因此只采用一個分型面。
4減速器殼體加工工藝設(shè)計
4.1加工工藝的設(shè)計
4.1.1設(shè)計原則
在保證質(zhì)量的前提下,要盡可能的提高生產(chǎn)率和降低生產(chǎn)的費用。要充分利用好現(xiàn)有的條件,結(jié)合國際上先進的技術(shù)和經(jīng)驗。要保持較好的勞動條件。要做到正確、完整和清晰的工藝規(guī)程,使用標(biāo)準(zhǔn)的術(shù)語、符號和單位。
4.1.2擬定加工工藝路線
(1) 確定定位基準(zhǔn)
(2) 確定各加工表面的加工方法
(3) 劃分加工階段
(4) 工序集中程度的確定
(5) 工序順序的安排
4.2選擇定位基準(zhǔn)
4.2.1定位基準(zhǔn)選擇原則
在制作零件時,用于定位的基準(zhǔn)稱為定位基準(zhǔn)。選擇正確的定位基準(zhǔn)在確定零件的技術(shù)要求和加工順序的順序方面起著關(guān)鍵的作用。定位基準(zhǔn)分為粗基準(zhǔn)和細(xì)基準(zhǔn)。一般以坯料未加工表面為基準(zhǔn),以后表面為基準(zhǔn),稱為精細(xì)基準(zhǔn)。定位基準(zhǔn)的選擇通常是根據(jù)零件的加工要求來選擇的,然后選擇一個表面作為粗基準(zhǔn),首先用粗處理精的表面。
(一)如何選擇精基準(zhǔn)
(1) 基準(zhǔn)重合原則:加工時可以選擇要加工的表面的設(shè)計基準(zhǔn)當(dāng)做定位基準(zhǔn),能夠防止因為基準(zhǔn)不重合造成的誤差。
(2) 基準(zhǔn)統(tǒng)一原則:每個工序選擇的基準(zhǔn)盡量相同,可以避免由于換基準(zhǔn)造成的誤差。
(3) 互為基準(zhǔn)原則:如果兩個表面的位置精度要求很高,形狀精度要求也很高,這時可以用這兩個表面作彼此的基準(zhǔn),進行后續(xù)的多次加工;
(4) 自為基準(zhǔn)原則:當(dāng)一個某個工序要求的加工余量很小,可以將加工表面作為自己的基準(zhǔn);
(2) 粗基準(zhǔn)選擇原則
粗基準(zhǔn)一般是第一道工序選擇的定位基準(zhǔn),主要是為了加工精基準(zhǔn)平面,方便后續(xù)的加工,選擇要遵循以下原則:
(1) 保證相互位置要求的原則。當(dāng)工件上存在不需要被加工的平面時,在滿足條件的情況下,可以選擇該平面為粗基準(zhǔn),這樣可以使得兩個表面之間的相互位置關(guān)系得到保證;
(2) 合理分配加工余量的原則。選擇重要的表面當(dāng)做粗基準(zhǔn),可以確保加工余量均勻;
(3) 便于工件裝夾原則。粗基準(zhǔn)平面要盡量平和光整,不要有缺陷,這樣可以使工件裝夾穩(wěn)定,可靠;
(4) 粗基準(zhǔn)一般不得重復(fù)使用原則。由于粗基準(zhǔn)的平面很粗糙,故通常粗基準(zhǔn)在同一尺寸方向上只允許用一次,重復(fù)使用會使誤差變大,影響加工。
故選擇?454的大平面為粗基準(zhǔn)。
4.2.2表面加工方法的選擇
一個工件的加工表面通常要經(jīng)過多道工序加工才能符合要求,故加工方法的選擇對加工表面的精度要求影響很大,對后續(xù)和之前的加工影響也很大。
加工方法的選擇原則
(1) 選擇的加工方法的經(jīng)濟性要確保符合所要求的精度和粗糙度;
(2) 能確保工件的形狀精度和位置精度;
(3) 確保零件的可加工性;
(4) 要適應(yīng)零件的生產(chǎn)類型。
4.2.3加工階段的劃分
加工表面要求的精度不同,加工階段的劃分也不同,主要有以下加工階段:
(1) 粗加工階段,在粗加工階段,主要時切除被加工表面的余量的大部分;
(2) 半精加工階段,除去粗加工時,表面上留下的一些誤差,為后續(xù)的精加工做好準(zhǔn)備;
(3) 精加工階段,保證工件的各項要求都符合零件圖上所要求的。
4.2.4加工順序安排
切削加工順序的安排:先粗后精,先主后次,先面后孔,基面先行
4.3加工工藝路線的擬定
表4-1 加工工序擬定路線
工序號
工序名稱
機床設(shè)備
量具
1
粗銑上端面
專用銑床
游標(biāo)卡尺
2
粗鏜?150孔
專用鏜床
塞規(guī),卡尺
3
半精鏜?150孔
專用鏜床
塞規(guī),卡尺
4
精鏜?150孔
專用鏜床
塞規(guī),卡尺
5
粗鏜?90孔
專用鏜床
塞規(guī),卡尺
6
半精鏜?90孔
專用鏜床
塞規(guī),卡尺
7
精鏜?90孔
專用鏜床
塞規(guī),卡尺
8
粗車階梯平面
專用車床
游標(biāo)卡尺
9
精車階梯平面
專用車床
游標(biāo)卡尺
10
精銑上端面
專用銑床
游標(biāo)卡尺
11
精?90孔上端面
專用車床
游標(biāo)卡尺
12
鉆、攻M12孔
專用鉆床
卡尺,塞規(guī)
13
鉆、攻7-M14孔
專用鉆床
卡尺,塞規(guī)
14
鉆3-?12孔
專用鉆床
卡尺,塞規(guī)
15
鉆14-?15,锪14-?32孔
專用鉆床
卡尺,塞規(guī)
16
鉆2-?3孔
專用鉆床
卡尺,塞規(guī)
17
鉆、攻4-M22孔
專用鉆床
卡尺,塞規(guī)
18
去毛刺
鉗工臺
19
清洗
清洗機
20
終檢
塞規(guī)、百分表等
4.4確定加工余量和工序尺寸
4.4.1重要平面的加工余量及工序尺寸的確定
為了保證后續(xù)的加工工序的零件尺寸,在銑削加工表面時,工序1的背吃刀量ap=2mm。工序5的背吃刀量ap=1.5mm,工序6的背吃刀量ap=0.5mm;工序2的背吃刀量1.5mm,工序3的背吃刀量0.5mm。
4.4.2其他加工工序尺寸及加工余量
(1) 鉆、攻M12×1.5孔
底孔尺寸:d=12-1.1×1.5=10.35mm;取10.5mm。
鉆孔:?10.5mm,2Z=10.5mm,ap=5.25mm
攻絲
(2) 鉆、攻7-M14×1.5孔
底孔尺寸:d=14-1.1×1.5=12.35mm;取12.5mm
鉆孔:?12.5mm,2Z=12.5mm,ap=6.25mm
攻絲
(3) 鉆3-?12孔
鉆孔:?11mm,2Z=11mm,ap=5.5mm
粗鉸:?11.95mm,2Z=0.95mm,ap=0.475mm,深12mm
精鉸:?12mm,2Z=0.05mm,ap=0.025mm,深12mm
(4) 鉆14-?15孔,锪14-?32孔
鉆孔:?14mm,2Z=14mm,ap=7mm
粗鉸:?14.95mm,2Z=0.95mm,ap=0.475mm
精鉸:?15mm,2Z=0.05mm,ap=0.025mm
锪孔:?32mm,2Z=17mm,ap=8.5mm,深1mm
(5) 鉆2-?3孔
鉆孔:?3mm,2Z=3mm,ap=1.5mm
(6) 鉆4-?22孔,鉆、攻4-M22孔
底孔尺寸:d=22-1.1×1.5=20.35,取20.5mm;
鉆孔:?20.5mm,2Z=20.5mm,ap=10.25mm
擴孔:?21.8mm,2Z=1.3mm,ap=0.65mm,深13mm
粗鉸:?21.94mm,2Z=0.14mm,ap=0.07mm,深13mm
精鉸:?22mm,2Z=0.06mm,ap=0.03mm,深13mm
攻絲
(7) 鏜?150孔
粗鏜:?145mm,2Z=3mm,ap=1.5mm
半精鏜:?148mm,2Z=1.6mm,ap=0.8mm
精鏜:?149.6mm,2Z=0.4mm,ap=0.2mm
(8) 鏜?90孔
粗鏜:?85mm,2Z=3mm,ap=1.5mm
半精鏜:?88mm,2Z=1.6mm,ap=0.08mm
精鏜:?89.6mm,2Z=0.4mm,ap=0.2mm
4.4.3確定切削用量及時間定額
1、 確定切削用量
1、 工序1——粗銑上端面
(1) 確定背吃刀量:取ap=2mm;
(2) 確定進給量:查表4-1,取=0.20mm/z
(3) 銑削速度:按照查表確定V=58m/min;
由可知,n=1000×58/(π×203)=73r/min,取n=75r/min,故實際銑削速度v=nπd/1000=58.8m/min,
機床功率/kW
鋼
鑄鐵及銅合金
每齒進給量/(mm/z)
YT15
YT5
YG6
YG8
5`10
0.09`0.18
0.12`0.18
0.14`0.24
0.20`0.29
>10
0.12`0.18
0.16`0.24
0.18`0.28
0.25`0.38
表4-2硬質(zhì)合金面銑刀銑削平面的進給量
表4-3精銑時銑刀每轉(zhuǎn)進給量
要求達到的粗糙度Ra/μm
3.2
1.6
0.8
0.4
每轉(zhuǎn)進給量/(mm/r)
0.5`1
0.4`0.6
0.2`0.3
0.15
當(dāng)nw=75r/min,工作臺的每分鐘進給量為:=×z×n=0.2×2.5×75=37.5mm/min;
由式可知取=0.03d;
故=0.5×203-=14.9,取=15mm;
取=1mm則基本時間:=5.84min=350s
輔助時間由式,取=0.15×350=52.5s
其他時間9%×(359+52.5)=36s
故工序1的單件時間為
2、工序2——粗鏜?150孔
(1)背吃刀量ap=1.5mm;
(2)進給量;取f=1mm/r;
(3)切削速度:由表4-4確定v=40m/min;則n=1000x40/3.14x150=84.9r/min;
由公式有,
式中L=48mm,l=45mm,=3mm,=4mm.f=1mm/r,n=84.9r/min,計算得=70s;
輔助時間:=0.15x9.2=10.4s;
其他時間:=7.2s
單件時間定額:=87.6s。
3、工序3——半精鏜?150孔
(1)背吃刀量ap=0.8mm;
(2)進給量;取f=0.8mm/r;
(3)切削速度:由表4-4確定v=60m/min;則n=1000x60/3.14x150=127r/min;
由公式有,
式中L=48mm,l=45mm,=3mm,=4mm.f=0.8mm/r,n=127r/min,計算得=59s;
輔助時間:=0.15x17=8.8s;
其他時間:=6.1s
單件時間定額:=73.9s。
4、工序4——精鏜?150孔
(1)背吃刀量ap=0.2m;
(2)進給量;取f=0.5mm/r;
(3)切削速度:由表4-4確定v=80m/min;則n=1000x80/3.14x150=169r/min;
由公式有,
式中L=48mm,l=45mm,=3mm,=4mm.f=0.5mm/r,n=169r/min,計算得=71s;
輔助時間:=0.15x17=10.6s;
其他時間:=7.3s
單件時間定額:=88.9s。
5、工序5——粗鏜?90孔
(1)背吃刀量ap=1.5mm;
(2)進給量;取f=1mm/r;
(3)切削速度:由表4-4確定v=40m/min;則n=1000x40/3.14x90=318r/min;
由公式有,
式中L=22mm,l=20mm,=3mm,=4mm.f=1mm/r,n=318r/min,計算得=9.2s;
輔助時間:=0.15x9.2=1.4s;
其他時間:=0.9s
單件時間定額:=11.5s。
6、工序6——半精鏜?90孔
(1)背吃刀量ap=0.8mm;
(2)進給量;取f=0.8mm/r;
(3)切削速度:由表4-4確定v=60m/min;則n=1000x60/3.14x90=212r/min;
由公式有,
式中L=22mm,l=20mm,=3mm,=4mm.f=0.8mm/r,n=212r/min,計算得=17s;
輔助時間:=0.15x17=2.6s;
其他時間:=1.7s
單件時間定額:=21.3s。
7、工序7——精鏜?90孔
(1)背吃刀量ap=0.2m;
(2)進給量;取f=0.5mm/r;
(3)切削速度:由表4-4確定v=80m/min;則n=1000x80/3.14x90=283r/min;
由公式有,
式中L=22mm,l=20mm,=3mm,=4mm.f=0.5mm/r,n=283r/min,計算得=20.7s;
輔助時間:=0.15x17=3.1s;
其他時間:=2.1s
單件時間定額:=25,9s。
8、工序8—粗車階梯平面
(1)確定背吃刀量:ap=1.5mm;
(2)確定進給量:取=0.4mm/r
(3)計算車削速度:由表4-3確定V=70m/min;n=1000x70/3.14x454=49r/min
表4-4硬質(zhì)合金車刀常用切削速度 單位:(m/min)
工件材料
硬度(HBW)
刀具材料
精車
(ap=0.3~2mm,f=0.1~0.3mm/r)
刀具材料
半精車(ap=2.5~6mm,f=0.35~0.65mm/r)
粗車
(ap=6.5~10mm,f=0.7~1mm/r)
灰鑄鐵
150~200
200~250
YG6
90~110
70~90
YG8
70~90
50~70
45~65
35~55
可鍛鑄鐵
120~150
YG6
130~150
YG8
100~120
70~90
由公式有
式中L=35mm,l=33mm,=3mm,=4mm.f=0.4mm/r,n=49r/min,計算得=229.5s;
輔助時間:=0.15×42=34.4s
其他時間:=23.7s
單件時間定額:=287.6s
9、工序9——精車階梯平面
(1)背吃刀量:ap=0.5mm;
(2)進給量;f=0.4mm;
(3)切削速度;查表4-3有,v=90m/min;則n=1000x90/3.14x454=63r/min;
由公式有,
式中L=35mm,l=33mm,=3mm,=4mm.f=0.4mm/r,n=63r/min,計算得=178.5s;
輔助時間:=0.15x33.3=26.7s;
其他時間:=18.4s
單件時間定額:=223.6s。
10、 工序10——精銑上端面
(1)確定背吃刀量:取ap=0.5mm
(2)確定進給量:由表4-2可知,取=0.5mm/r,即=0.04mm/z;
(3)計算銑削速度:確定銑削速度v=66mm/min。計算=84r/min;取轉(zhuǎn)速n=95r/min.則實際銑削速度為=74.5m/min。
有公式計算出,=0.04×2.5×95=95mm/min,=203mm,=15mm,=1mm;
上述結(jié)果代入公式有=2.3min=138s
輔助時間由式,取=0.15×138=21s
其他時間9%×(138+21)=14s
故工序1的單件時間為
11、工序11——精銑?90孔上端面
(1)背吃刀量:ap=1.5mm;
(2)進給量:f=0.4mm/r;
(3)切削速度:由表4-3,確定V=90m/min;則n=1000x90/3.14x454=63r/min;
由公式有,
式中L=9mm,l=7mm,=3mm,=4mm.f=0.4mm/r,n=63r/min,計算得=54.7s;
輔助時間:=0.15x54.7=8.2s;
其他時間:=5.6s
單件時間定額:=68.5s。
12、工序12——鉆、攻M12孔
(1) 鉆孔工步
1) 確定背吃刀量:ap=5.25mm;
2) 確定進給量:f=0.12mm/r
3) 切削速度:由表4-5可知,取V=20m/min,
則n=1000×20/(3.14×10.5)=606.6r/min,取n=680r/min。則實際切削速度為v=680×3.14×10.5/1000=22.4m/min
表4-5 在組合機床上用高速鋼刀具鉆孔時的切削用量
加工孔徑/mm
1~6
6~12
12~22
22~50
鑄鐵
160~200HBW
V/(m/min)
16~24
f/(mm/r)
0.07~0.12
0.12~0.2
0.2~0.4
0.4~0.8
200~241HBW
V/(m/min)
10~18
f/(mm/r)
0.05~0.1
0.1~0.18
0.18~0.25
0.25~0.4
300~400HBW
V/(m/min)
5~12
f/(mm/r)
0.03~0.08
0.08~0.15
0.15~0.2
0.2~0.3
根據(jù)鉆孔的基本時間公式有:
(45+4.8+1)/0.12×680=39.5s
輔助時間:=0.15×39.5=5.9s
其他時間:=4s
單件時間定額:=49.4s
(2) 攻絲工步
1) 進給量:f=1.5mm/r
2) 切削速度:由表4-6可知,v=8m/min,則n=1000×8/(3.14×12)=212.3r/min,取n=275r/min。則實際切削速度為v=275×3.14×12/1000=10.3m/min
表4-6 組合機床上加工螺紋的切削速度
工件材料
鑄鐵
鋼及合金鋼
鋁及鋁合金
V/(m/min)
5~10
3~8
10~20
根據(jù)攻螺紋基本時間公式有,=14.4s
輔助時間:=0.15×14.4=2.16s
其他時間:=1.5s
單件時間定額:=18.06s
故工序9單件時間定額為67.46s。
13、工序13——鉆、攻7-M14孔
(1)鉆孔工步
1)確定背吃刀量:ap=6.25mm;
2)確定進給量:f=0.2mm/r
3)切削速度:由表4-5可知,取V=20m/min,則n=1000×20/(3.14×10.5)=606.6r/min,取n=680r/min。則實際切削速度為v=680×3.14×10.5/1000=26.7m/min
根據(jù)鉆孔的基本時間公式有:
(45+4.8+1)/0.2×680=22.4s
輔助時間:=0.15×22.4=3.4s
其他時間:=2.3s
單件時間定額:=28.1s
(2)攻絲工步
1)進給量:f=1.5mm/r
2)切削速度:由表4-6可知,v=8m/min,則n=1000×8/(3.14×14)=181.9r/min,取n=195r/min。則實際切削速度為v=195×3.14×14/1000=8.5m/min。
根據(jù)攻螺紋基本時間公式有,=70.7s
輔助時間:=0.15×70.7=10.6s
其他時間:=7.3s
單件時間定額:=88.6s
故工序10單件時間定額為116.7s
14、工序14——鉆3-?12孔
(1) 鉆孔工步
1)確定背吃刀量:ap=5.5mm;
2)確定進給量:f=0.2mm/r
3)切削速度:由表4-5可知,取V=20m/min,
則n=1000×20/(3.14×11)=579r/min,取n=680r/min。則實際切削速度為v=680×3.14×11/1000=23.4m/min.
根據(jù)鉆孔的基本時間公式有:
(12+3.8+1)/0.2×680=7.4s
輔助時間:=0.15×7.4=1.1s
其他時間:=0.76s
單件時間定額:=9.26s
(2) 粗鉸工步
1) 確定背吃刀量:ap=0.475mm;
2)確定進給量:f=0.15mm/r
3)切削速度:取V=8m/min,
則n=1000×8/(3.14×11.95)=213.2r/min,取n=272r/min。則實際切削速度為v=272×3.14×11.95/1000=10.2m/min.
根據(jù)鉸孔基本時間公式有,=21s;
輔助時間:=0.15×21=3.1s
其他時間:=2.1s
單件時間定額:=26.2s
(3)精鉸工步
1) 確定背吃刀量:ap=0.025mm;
2)確定進給量:f=0.1mm/r
3)切削速度:取V=5m/min,
則n=1000×5(3.14×12)=132.6r/min,取n=195r/min。則實際切削速度為v=195×3.14×12/1000=7.3m/min.
根據(jù)鉸孔基本時間公式有,=51.6s;
輔助時間:=0.15×64=7.74s
其他時間:=5.3s
單件時間定額:=64.6s
故工序11的總單件時間定額:100.06s
15、工序15——鉆14-?15孔,锪14-?32孔
(1)鉆孔工步
1)確定背吃刀量:ap=7mm;
2)確定進給量:f=0.2mm/r
3)切削速度:由表4-5可知,取V=20m/min,
則n=1000×20/(3.14×14)=454r/min,取n=545r/min。則實際切削速度為v=545×3.14×14/1000=23.9m/min.
根據(jù)鉆孔的基本時間公式有:
(16+3.8+1)/0.2×545=11.4s
輔助時間:=0.15×11.4=1.71s
其他時間:=1.17s
單件時間定額:=14.28s
(2)粗鉸工步
1) 確定背吃刀量:ap=0.475mm;
2)確定進給量:f=0.2mm/r
3)切削速度:取V=8m/min,
則n=1000×8/(3.14×14.95)=170.2r/min,取n=195r/min。則實際切削速度為v=195×3.14×14.95/1000=9.15m/min.
根據(jù)鉸孔基本時間公式有,=32s;
輔助時間:=0.15×32=4.8s
其他時間:=3.3s
單件時間定額:=40.1s
(3)精鉸工步
1) 確定背吃刀量:ap=0.025mm;
2)確定進給量:f=0.15mm/r
3)切削速度:取V=5m/min,
則n=1000×5/(3.14×15)=106.1r/min,取n=195r/min。則實際切削速度為v=195×3.14×15/1000=9.18m/min.
根據(jù)鉸孔基本時間公式有,=34.4s;
輔助時間:=0.15×34.4=5.16s
其他時間:=3.56s
單件時間定額:=43.12s
(4)锪孔工步
1)背吃刀量:ap=17mm;
2)進給量:f=0.3mm/r
3)切削速度:取v=8m/min;則n=1000×8/(3.14×32)=79.6r/min,取n=97r/min.則實際切削速度為v=9.7m/min.
根據(jù)锪孔基本時間公式有,=4.1s;
輔助時間:=0.15×4.1=0.6s
其他時間:=0.4s
單件時間定額:=5.1s
故工序11的總單件時間定額:102.6s
16、工序16——鉆2-?3孔
1)確定背吃刀量:ap=1.5mm;
2)確定進給量:f=0.1mm/r
3)切削速度:由表4-5可知,取V=8m/min,
則n=1000×8/(3.14×3)=849r/min,取n=960r/min。則實際切削速度為v=960×3.14×3/1000=9m/min.
根據(jù)鉆孔的基本時間公式有:
5.37s
輔助時間:=0.15×5.37=0.8s
其他時間:=0.55s
單件時間定額:=6.72s。
17、工序17——鉆、攻4-M22孔
(1)鉆孔工步
1)確定背吃刀量:ap=10.25mm;
2)確定進給量:f=0.2mm/r
3)切削速度:由表4-5可知,取V=20m/min,
則n=1000×20/(3.14×20.5)=310r/min,取n=392r/min。則實際切削速度為v=392×3.14×20.5/1000=25.2m/min.
根據(jù)鉆孔的基本時間公式有:
40.8s
輔助時間:=0.15×11.4=6.12s
其他時間:=4.22s
單件時間定額:=51.44s
(2)擴孔工步
1) 確定背吃刀量:ap=0.65mm;
2)確定進給量:f=1mm/r
3)切削速度:取V=20m/min,
則n=1000×20/(3.14×21.8)=292r/min,取n=392r/min。則實際切削速度為v=392×3.14×21.8/1000=26.8m/min.
根據(jù)擴孔基本時間公式有,=2.2s;
輔助時間:=0.15×=0.33s
其他時間:=0.23s
單件時間定額:=2.76s
(3) 粗鉸工步
1) 確定背吃刀量:ap=0.07mm;
2)確定進給量:f=0.25mm/r
3)切削速度:取V=8m/min,
則n=1000×8/(3.14×21.94)=116r/min,取n=195r/min。則實際切削速度為v=195×3.14×21.94/1000=13.5m/min.
根據(jù)鉸孔基本時間公式有,=17.5s;
輔助時間:=0.15×17.5=2.6s
其他時間:=1.8s
單件時間定額:=21.9s
(4) 精鉸工步
1) 確定背吃刀量:ap=0.03mm;
2)確定進給量:f=0.15mm/r
3)切削速度:取V=5m/min,
則n=1000×5/(3.14×22)=72r/min,取n=97r/min。則實際切削速度為v=97×3.14×22/1000=6.7/min.
根據(jù)鉸孔基本時間公式有,=58.7s;
輔助時間:=0.15×58.7=8.8s
其他時間:=6s
單件時間定額:=73.5s
(5) 攻絲工步
1)進給量:f=1.5mm/r
2)切削速度:由表4-6可知,v=8m/min,則n=1000×8/(3.14×22)=115.8r/min,取n=195r/min。則實際切削速度為v=195×3.14×22/1000=13.5m/min。
根據(jù)攻螺紋基本時間公式有,=32.4s
故工序14的總單件時間定額為182s
5、 機床夾具設(shè)計
表5-1 零件分析
工件名稱
40裝載機減速器殼體
圖號
材料
QT400
生產(chǎn)類型
大批生產(chǎn)
夾具類型
銑床型號
銑床夾具
專用機床
同時裝夾工件數(shù)目
1
5.1分析原始資料
圖5-1為裝載機減速器殼體的零件圖,毛坯材料為QT400
要求設(shè)計工序1——粗銑上端面的專用夾具,本工序采用的是?250mm的三面刃銑刀安裝在專用機床上,一套夾具只裝夾一件工件。
切削參數(shù):ap=2mm,=0.20mm/z,n=37.5r/min,v=23.9m/min。
5.2擬定夾具機構(gòu)方案,繪制夾具結(jié)構(gòu)草圖
5.2.1確定夾具類型
這個選擇的工序是要加工一個平面,即殼體上端面。每套夾具上面裝夾一件工件,夾具宜采用直線進給式,單件加工;
5.2.2擬定定位以及夾緊方案
(1)定位
作者分析即將要加工的零件的零件圖,得出如下結(jié)論:被加工表面的垂直度,與中間?70孔端面的垂直距離以及與工藝凸臺的加工要求等。因此,減速器殼體要限制六個自由度,才能保證定位精度。分析零件圖,了解工件的結(jié)構(gòu)和各項要求,定位方案如下:
以中間?70孔、大平面和兩個加強筋之間的凹槽為定位基準(zhǔn),?70孔用液壓驅(qū)動的三爪卡盤定位,大平面用支承釘,凹槽用同樣輪廓的塞柱卡住。這樣能限制住六個自由度。
(2)擬定夾緊方案
由零件圖可以看出,加工零件的加工表面時,零件可以垂直放置,也可水平放置,這里選擇垂直放置,銑刀在切削時,切削力主要在銑刀旋轉(zhuǎn)的切線方向上,所以加工時,讓銑刀平面與工件被加工面保持平行,從工件的一側(cè)垂直加工到另外一側(cè),這樣才能保證銑刀在切削工件時產(chǎn)生的切削力主要集中于垂直于殼體的側(cè)面,因此,殼體的夾緊力方向也主要在切削力方向。實現(xiàn)這種夾緊的結(jié)構(gòu)比較簡單,并具有良好的性能。
5.3選擇、設(shè)計定位裝置的結(jié)構(gòu),確定主要尺寸并計算定位誤差
(1)定位元件的選擇或者設(shè)計
綜合考慮夾緊方式和定位基準(zhǔn)的特點,和夾具體上定位元件的安裝要求,大平面定位采用支承釘定位;?70孔定位則采用標(biāo)準(zhǔn)元件,采用三爪卡盤;凹槽的定位可以根據(jù)零件加強筋凹槽輪廓設(shè)計定位原件。工件的夾緊采用壓板豎直放置,壓住殼體的大平面位置,用液壓驅(qū)動來實現(xiàn)夾緊。
(2)夾具體的材料
為了節(jié)約成本,使用HT200通過鑄造加工,壓板則使用45鋼為佳。
(3)定位誤差的計算
影響工序尺寸的定位誤差,由于設(shè)計基準(zhǔn)和定位基準(zhǔn)重合,所以定位基準(zhǔn)為0,只用考慮位置誤差。
當(dāng)△d/3>△w時,說明該定位方法符合加工要求,不會產(chǎn)生加工誤差
由于定位銷的尺寸為直徑70mm,中間的尺寸為,公差為0.022mm
經(jīng)過計算可得 0.7/3=0.23mm>0.025mm。
綜上考慮,擬定的定位方案可以確保加工要求,可以使用。
5.4選擇、設(shè)計夾緊裝置并驗算夾緊力
(1) 選擇、設(shè)計夾緊裝置的結(jié)構(gòu)
(2) 被加工工件的加工精度、粗糙度、生產(chǎn)率、加工時間等都受到夾緊裝置設(shè)計的影響,故,夾緊裝置要滿足如下要求:
a.夾緊裝置夾緊后,要能確保定位基準(zhǔn)的準(zhǔn)確,不能使其遭到破壞。
b.防止工件和夾具發(fā)生形變,要限制夾緊力的大小。
c.操作安全、方便、省力,具有良好的結(jié)構(gòu)工藝性,便于制造,方便使用和維修。
d.夾緊機械必須可靠。
d.要根據(jù)實際情況來確定夾緊裝置的復(fù)雜程度。
根據(jù)加工零件的要求,將液壓驅(qū)動的壓板安裝夾具體上面,工件放在夾具體后,蓋上壓板,并通過液壓缸產(chǎn)生的夾緊力,將工件夾緊。本要求減輕操作工人的勞動強度,采用氣動或者液壓夾緊的方式,由于是大批量生產(chǎn),夾具不宜復(fù)雜,簡單的螺母夾緊則比較理想,在一定程度上還是可以減輕工人的勞動強度。
圖5-2定位與夾緊裝置的液壓系統(tǒng)圖
(3) 驗算夾緊力
計算圓周切削力根據(jù)切削用量手冊可知,面銑刀在加工球墨鑄鐵材料是的圓周切削力的計算公式為:
式中:--在銑刀銑削時,考慮工件材料及銑刀類型的系數(shù);
——銑削深度(mm)
——每齒進給量(mm/z)
——銑刀的齒數(shù)
——銑刀銑削時,考慮工件材料機械性能不同的修正系數(shù)
——銑刀直徑(mm)
——銑削寬度(mm)
夾緊力計算公式:
經(jīng)計算可知,滿足工件被加工時的夾緊要求。
5.5確定對刀裝置
當(dāng)對刀裝置