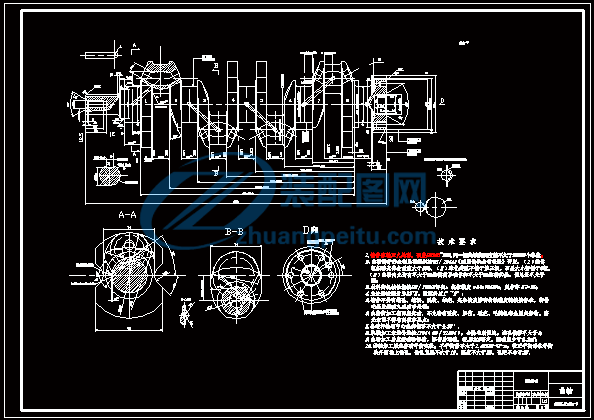
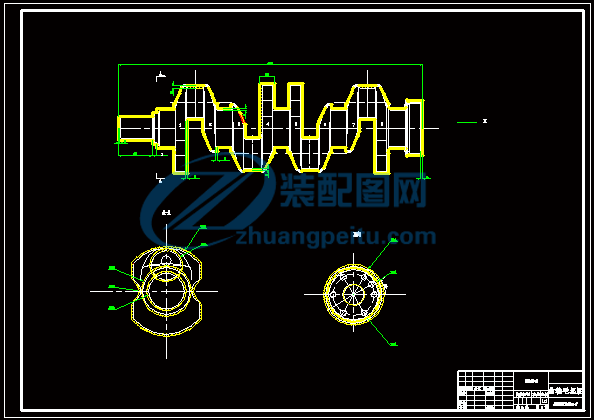
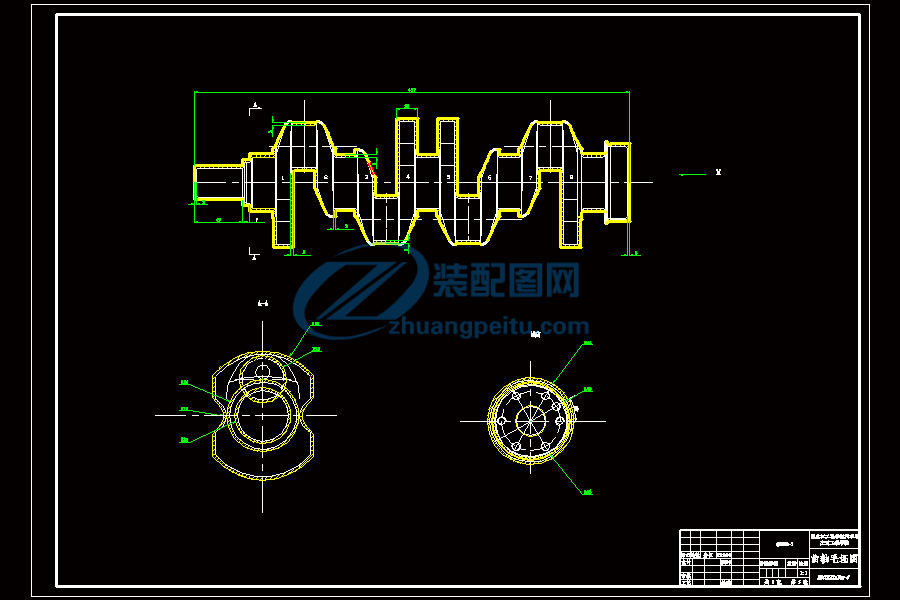
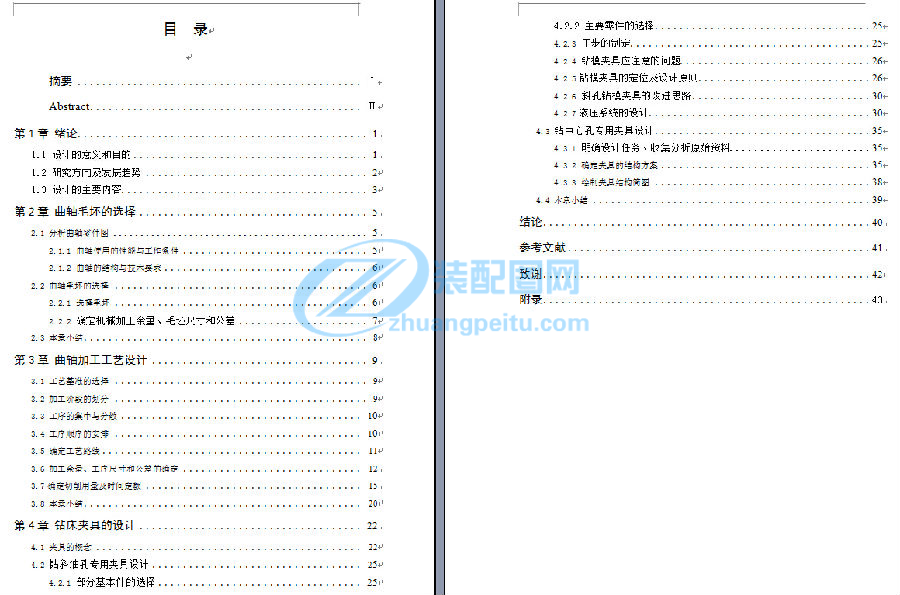
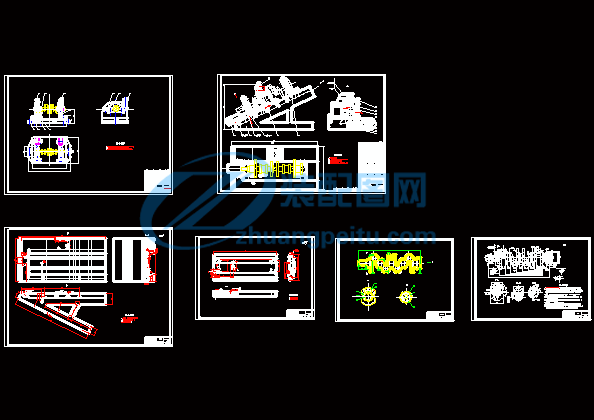
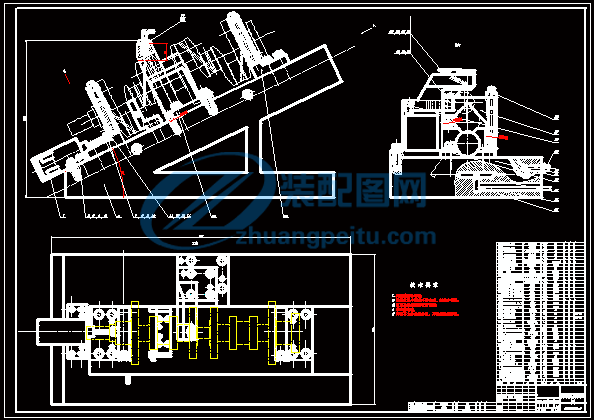
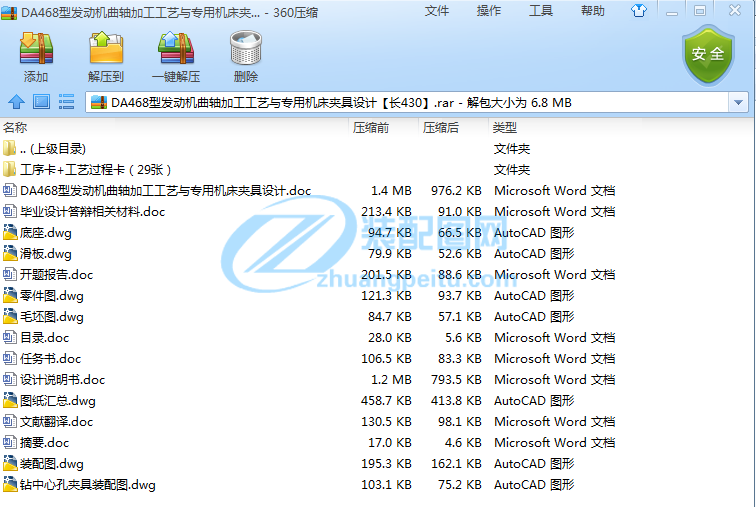
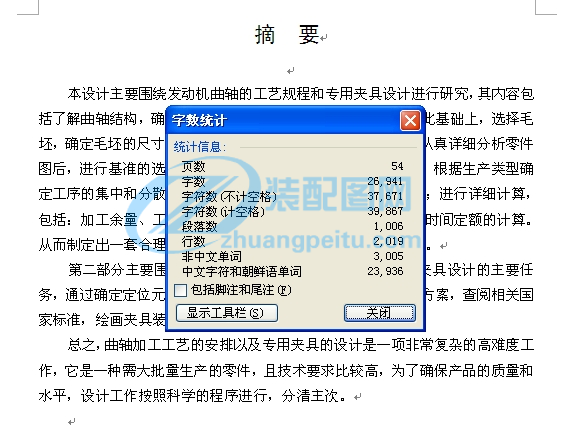
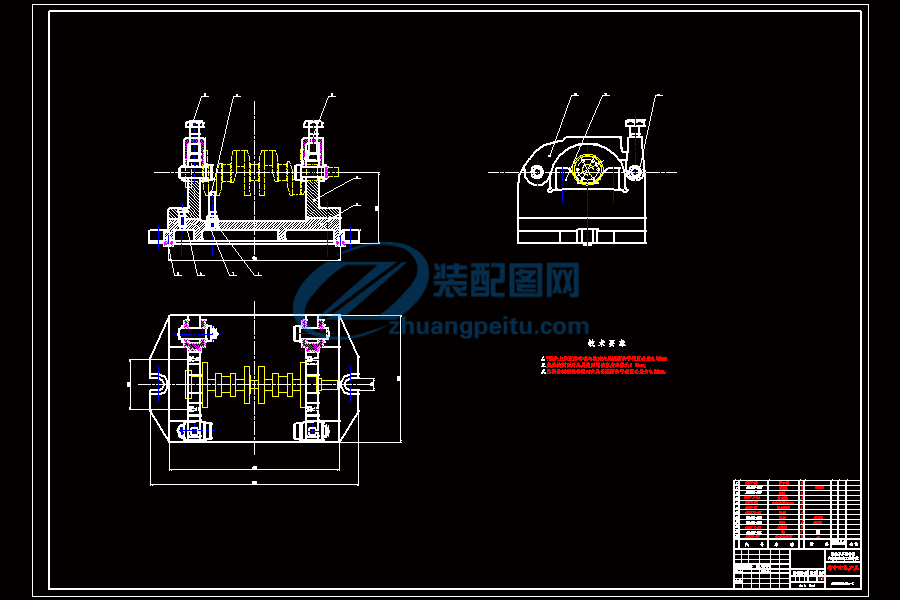
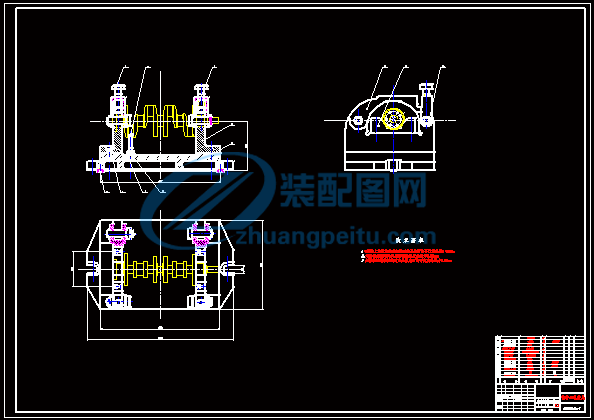
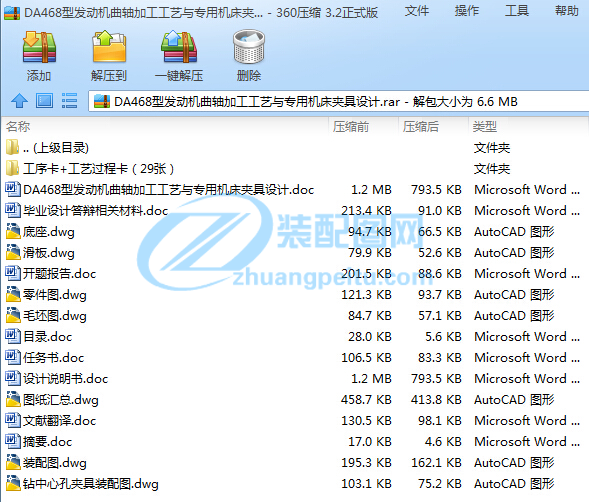
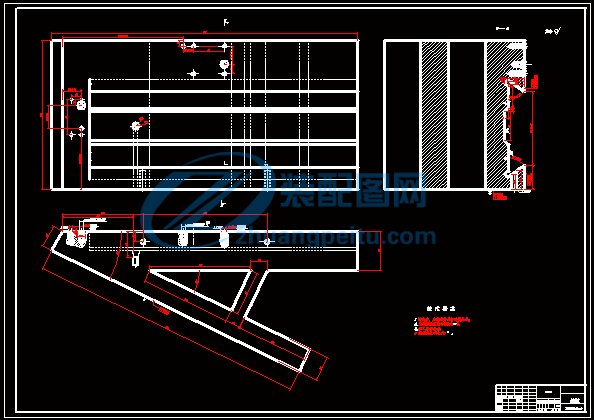
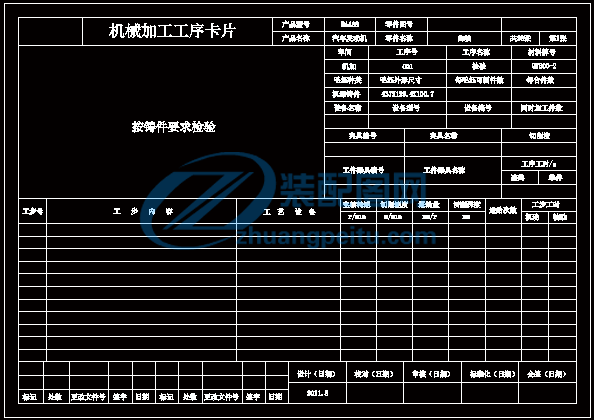
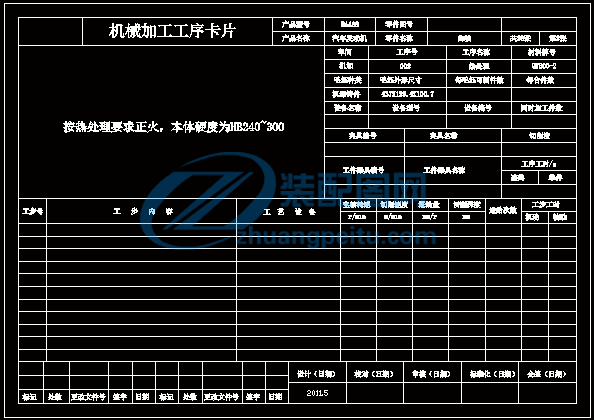
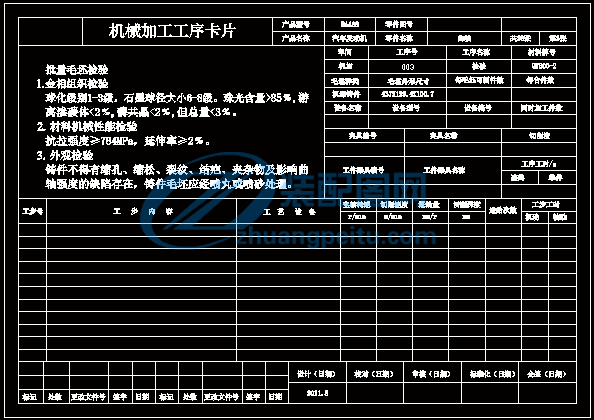
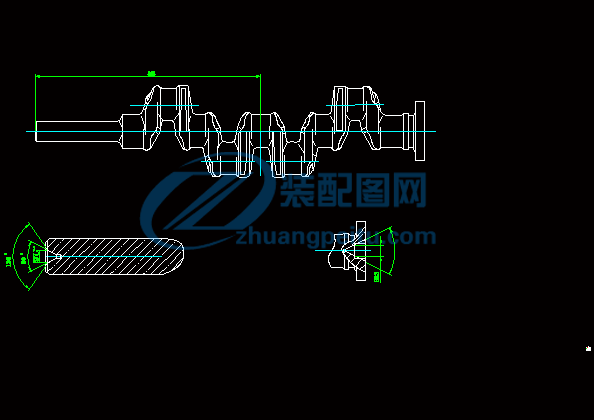
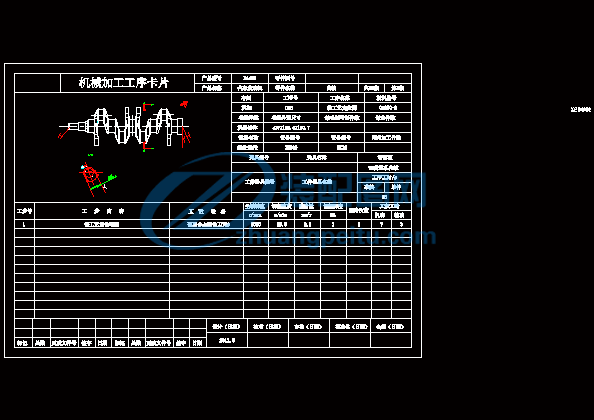
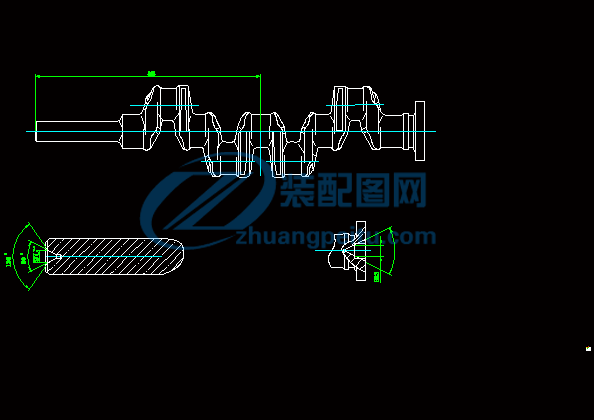
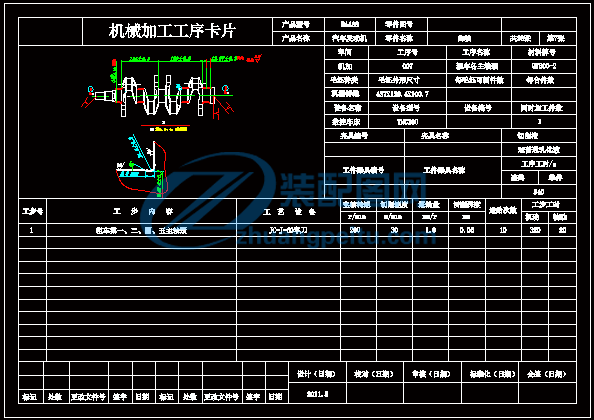
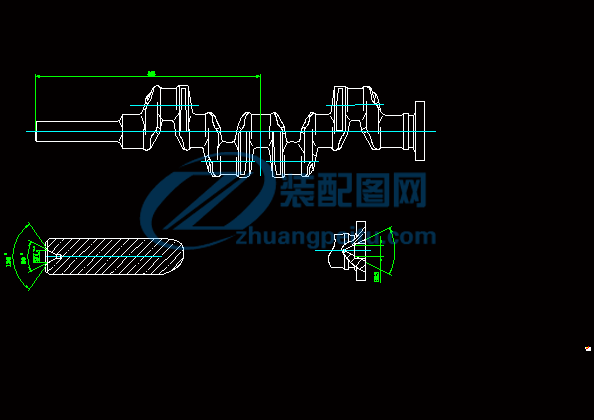
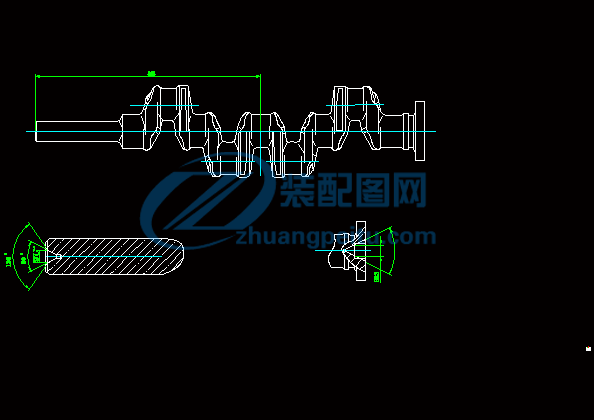
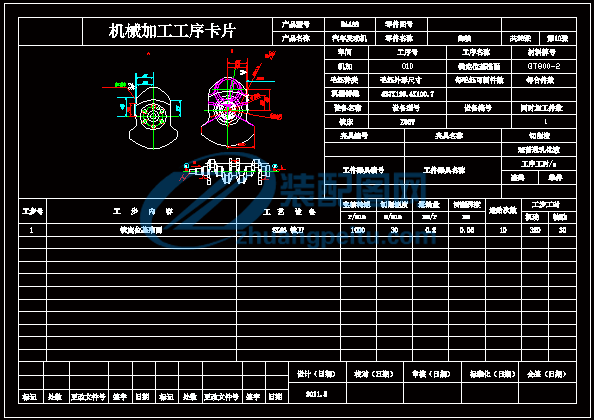
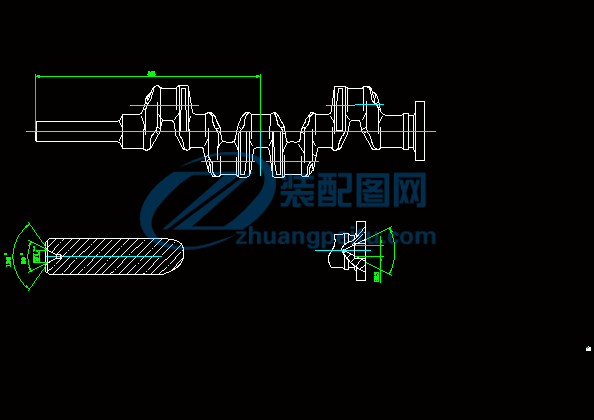
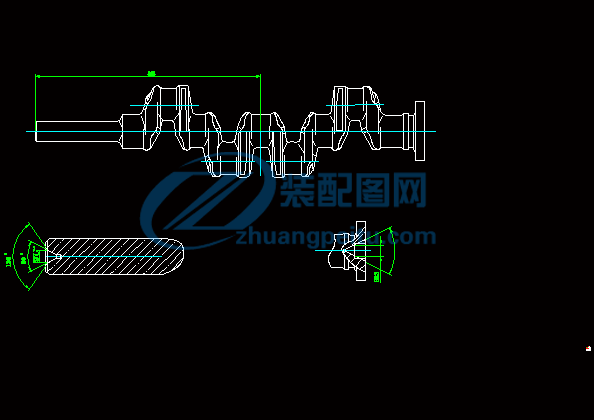
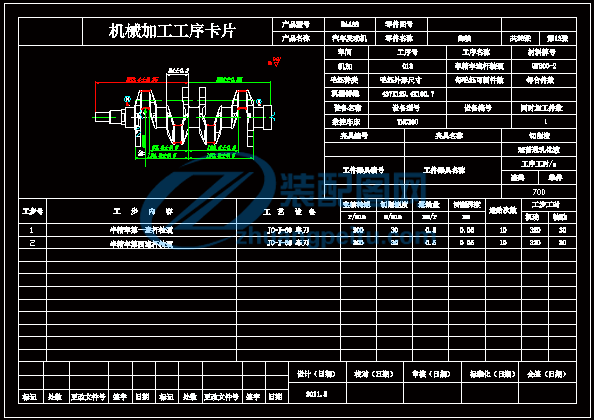
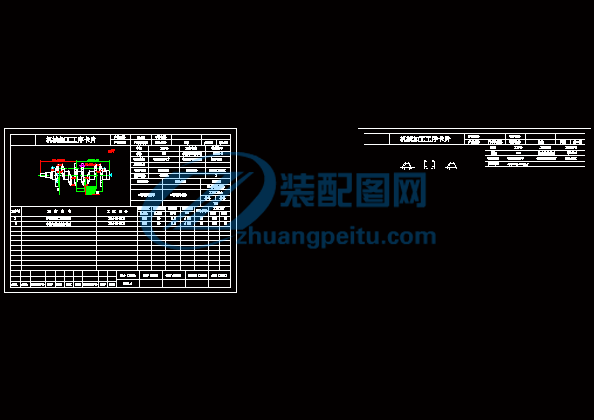
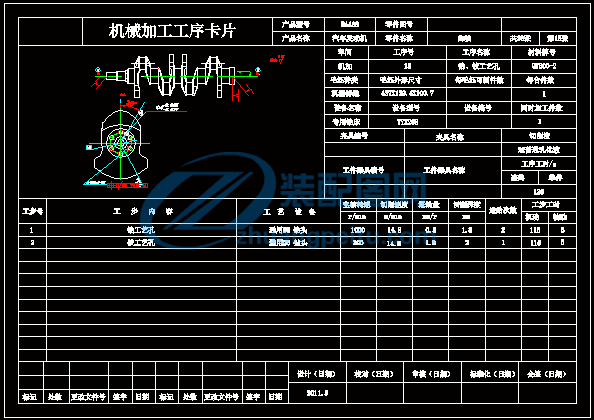
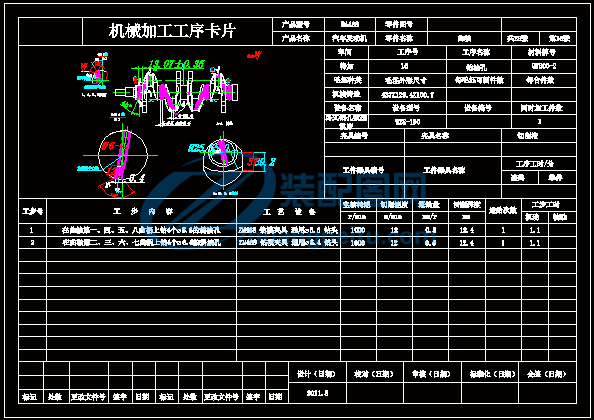
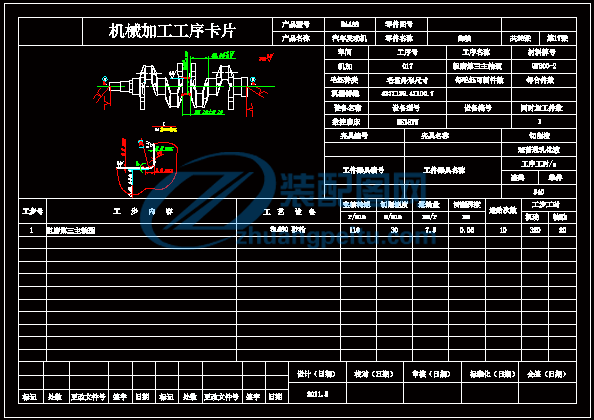
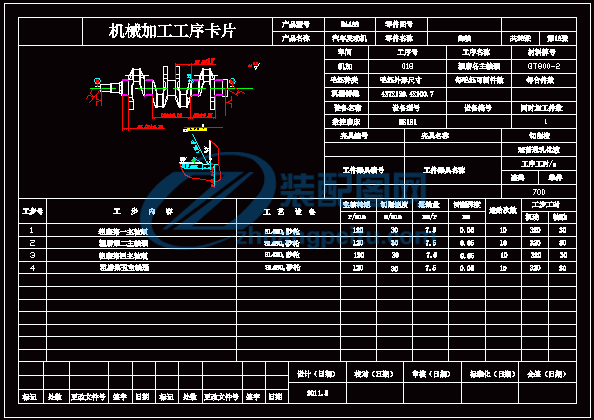
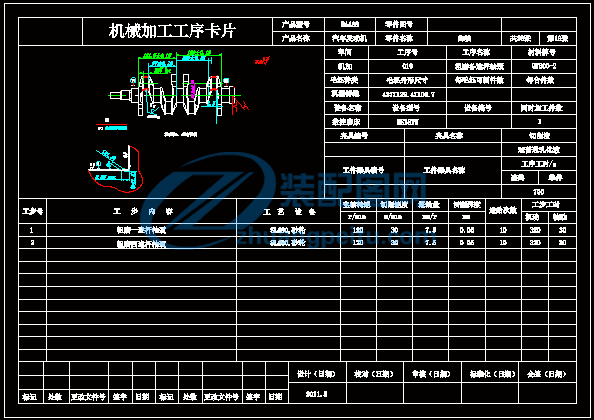

附錄 AInvestigation on Pressure Impact in ConcretePumping Hydraulic SystemAbstract:The pressure impact in hydraulic systems of such concrete pumping machinery as trailer concrete pump,transported concrete pump,and truck mounted concrete pump,is a key factor affecting their reliability and usage life.Based on the pressure forming principle of the oil in a hydrostatic closed pressure chamber,the mechanism of producing pressure impact is analyzed synthetically,and the theory that oil flow matches requirement, and pump displacement control harmonizes valve shifting time control,to mitigate pressure impact,is put forward.The quantitative controlling parameters about shifting time and displacement control are introduced to realize accurate control.The experiment investigations of pressure impact property and its control are carried through on an experimental system which is able to simulate concrete pumping condition.The basic law that pressure impact and controlling parameters vary with working condition respectively.The feasibility and validity of the technology proposed in this paper to control pressure impact are confirmed.Keywords: Pressure impact;Hydraulic system; Concrete pumping machinery.1 IntroductionDuring working process of such concrete machinery as trailer concrete pump,transported concrete pump,and truck mounted concrete pump,two oil cylinders drive two concrete delivery cylinders respectively,and quickly switch direction with the possible highest frequency of more than 30 times per minute,which generates serious hydraulic impact.It is an important factor resulting in bad performance and low use reliability of the machine, and vibration,noise and overheating etc.so it’s a key of improving concrete pumping machinery’s reliability to gain a mastery of pressure impact property in concrete pumping hydraulic system and its controlling technology.Such technological measures as follows were taken to reduce pressure impact: (1)installation of a hydraulic accumulator or unloading valves,(2) change of sliding spool’s structure,(3)control of the switching speed of sliding spool,etc[1].Though these measures play an important role in absorption of pressure surges,there are obvious limitations, and they are passive measures.Literature.2. investigated the switching process of concrete pumping hydraulic system,and put forward active measure of regulating oil pump’s displacement to reduce pressure impact.Literature[3]studied the intrinsic relationship between shifting time and pressure impact,and proposed a new concept of optimal shifting time.Therefore,in this paper, experiments were conducted to find out pressure impact forming law, and both oil pump’s displacement and directional—control valve’s shifting time were controlled simultaneously to seek optimal control scheme for effective reduction of pressure impact.2 Experimental principleThe pressure variation of the oil in a pressure chamber depends upon the difference between volumes of the oil flowing in and out the chamber[2].It’s obvious that effective reduction of this difference is of positive significance for depressing pressure impact. As far as concrete pumping hydraulic system is concerned, the pressure impact resulting from the main oil cylinders’ stroke terminal lies upon the suitability of shifting time to a great extent[3].So it’s feasible and effective for absorbing pressure impact to accurately control oil pump’s displacement according to hydraulic system’s requirement,and combine it with shifting time control technique.What is shown in Fig.1 is the principle drawing of the experimental system sued to study characteristics of pressure impact in concrete pumping hydraulic system and its controlling techniques.The main oil pump(1)is a swash-plate type axial piston pump,which is provided with the function of constant horsepower control。negative flow contr01.The pressured oil used to contr01 oil pump’s displacement comes from tilting system.In this controlling oil line,a 3-way,2-position directional valve(11)with one solenoid and a pressure reducing valve(12)are installed in series.When the solenoid of valve(11)is de-energized,the pressured oil from tilting system is stopped,and the pressured oil in the displacement control device of oil pump(1)is introduced into oil reservoir simultaneously by the valve(11).Here,the oil pressure in the displacement control device is zero or very low,the oil pump’s displacement can come to maximum.On the other hand,when the solenoid of valve(11)is energized,the pressured oil coming from tilting system is introduced by the valve(11),and is decompressed by pressure reducing valve (12),and comes into the displacement control device,so 8s to make oil pump’s displacement be reduced to minimum or zero.Two hydraulic cylinders(6.1,6.2)are connected in series,and four check valves and four throttle valves,which perform the functions of suction and cushioning.a(chǎn)re installed on the cylinders.Two non-contacting sensors(9,10)are used to provide shifting signals.Four pressure sensors are installed at the testing points M1,M2,M3 and M4 respectively.The signals provided by these sensors are collected and analyzed synchronously by a spectrum instrument and a microcomputer.The sampling frequency is 1 kHz.The sampling time is one minutes at a time so as to gain several pressure signals during shifting from a sampling.During the experimental process,the pressure signals only during such shifting process as oil cylinders(6.1and 6.2)extends and retracts to the end respectively were analyzed.When the sensor(10)obtains the signal of cylinder(6.2)retracting stroke terminal,the electrical system gives the instrument for regulating oil pump’s displacement to decrease its swash-plate’s angle,and gives signal to make valves(8,7)shift after a certain time 1ag. During such shifting process,the shifting time of valve(1)depends on following two factors:one is the sensor(10)’s installation position relative to the cylinder(6.2);the other is the shifting time lag . i.e.the difference between the times when main oil pump(1)begins ??regulating displacement and when the hydro-piloted directional contr01 valve (7)begins to shift.In order to simplify the experiments,the sensor(10)’s installation position relative to the cylinder(6.2)is changeless,and the oil pump’s displacement regulating time is also invariable.The difference between the times when the oil pump’s displacement begins to reduce and when begins to increase is 0.2s.3 Experimental results and analysis Figure.2 shows the curves of pressure versus time, which were measured at points M1 and M2 when time lag At.is 0.12s.It can be seen from the curves shown in Fig.2 that the pressure impact extent in the chamber in which the testing point M1 is situated decreases gradually along with an increase in the working pressure.The main reason is that the pump adopts constant power control,in response to the rise of the working pressure,the swash-plate’s tilting angle is decreased,and pump’s displacement is reduced。 the main oil cylinder’s velocity becomes smaller.So the pressure impact decreases.It’s also seen from Fig.2 that there are two pressure peaks in the curves measured at testing point M1.The time of producing those two pressure peaks corresponds with the two transitional positions of directional control valve(7)during its spool shifts.Figure.3 shows the curves of pressure versus time, which were measured at points M1 and M3 when time lag At:is 0.09s, and the working pressure is10 Mpa. It can be seen from Fig.3 that the second pressure peak in the curve measured at point M1 is much smaller than the first one.The main reason is as follows:when the sliding spool of directional control valve(7)moves to the first transitional position,it’s impossible that obvious variation of swash—plate’s tilting angle takes place,and the oil flow is still big. When the sliding spool of directional control valve(7) moves to the second transitional position, swash-plate’s tilting angle has become relatively small,and the oil flow is also small.Therefore,the volume difference of the oil between flowing in and flowing out the pressure chamber at the second transitional position is much smaller than at the first transitional position,which results in that the second pressure peak is much smaller than the first one.It can be seen;by a comparison between Fig. 2(a)and Fig.3,that the time lag At: has obvious influence upon pressure impact at the testing point M1.Too short time lag.附錄 B混凝土運(yùn)輸車中液壓泵壓力的影響摘要 本文介紹了混凝土運(yùn)輸車中液壓泵中的壓力大小對整個(gè)液壓系統(tǒng)的影響,液壓泵的壓力大小是影響整個(gè)工作系統(tǒng)的可靠性和使用壽命的關(guān)鍵因素,如何確定液壓油在封閉液壓缸中產(chǎn)生的壓力的大小,要通過綜合和理論上進(jìn)行分析才能確定該工況下產(chǎn)生壓力的影響,比如,油流量的要求,泵排量的控制,協(xié)調(diào)閥反應(yīng)時(shí)間的控制,通過這些方面的控制,通過改變其中任何一個(gè)都可以減輕壓力對整個(gè)系統(tǒng)的影響,只要通過定量控制這些參數(shù)的變化時(shí)間以及位移的控制就能做到,本文介紹了為實(shí)現(xiàn)準(zhǔn)確控制,通過實(shí)驗(yàn)調(diào)查壓力的影響以及控制其影響的實(shí)驗(yàn)系統(tǒng),這個(gè)實(shí)驗(yàn)系統(tǒng)能夠模擬混凝土泵在工作情況中的基本參數(shù),這種壓力的影響和控制參數(shù)的不同分別與工作條件的可行性和有效性的技術(shù),本文提出了如何控制壓力影響進(jìn)行了驗(yàn)證。關(guān)鍵詞 壓力的影響; 液壓系統(tǒng) ; 混凝土運(yùn)輸液壓系統(tǒng)中的液壓泵1 簡介在工作過程中,例如混凝土運(yùn)輸裝置比如用卡車作為混凝土泵的運(yùn)輸裝置,用來放置混凝土泵,混凝土運(yùn)輸車,兩個(gè)汽油氣缸來驅(qū)動(dòng)兩個(gè)具體交換氣瓶分別和快速切換方向,頻率最高能夠超過 30 次每分鐘,這會(huì)產(chǎn)生嚴(yán)重的液壓沖擊,這是一個(gè)重要因素對于增加系統(tǒng)的不良性能并且降低系統(tǒng)的可靠性,如何降低這種這種機(jī)器振動(dòng)、噪聲和系統(tǒng)溫度過高的影響,關(guān)鍵的因素是增強(qiáng)混凝土機(jī)械泵的可靠性并且掌握壓力的影響,完善混凝土運(yùn)輸系統(tǒng)中液壓泵以及液壓系統(tǒng)及其控制技術(shù)。采取如下幾種措施可以減少壓力對系統(tǒng)的影響;1 安裝液壓儲(chǔ)能器或卸載閥,2 改變滑動(dòng)閥芯的結(jié)構(gòu),3 控制開關(guān)速度滑動(dòng)閥芯等。雖然這些措施具有很重要的作用,可以吸收激增的壓力,但還是有明顯的局限性,他們是被動(dòng)的措施,調(diào)查過程中對于具體的液壓系統(tǒng),提出了新的方法調(diào)節(jié)油泵流量,減少壓力的影響,通過研究液壓油流量時(shí)間和壓力的內(nèi)在影響,提出了新的方法來優(yōu)化流量時(shí)間,因此,通過大量的實(shí)驗(yàn)在次基礎(chǔ)下找出壓力影響的規(guī)律,在油泵轉(zhuǎn)速和方向閥的改變時(shí)間被控制的同時(shí),尋求最佳控制計(jì)劃,有效減少壓力影響。2 實(shí)驗(yàn)原理壓力的變化取決于在壓力室中液壓油流入量與流出量之間的差異,很明顯,有效的減少這種差別是具有重要意義的減少壓力的影響。至于混凝土運(yùn)送液壓系統(tǒng)而言,壓力造成的影響主要是液壓油在液壓缸終端的撞擊的移動(dòng)時(shí)間過快。所以根據(jù)液壓系統(tǒng)的要求,可行和有效的吸收壓力的影響,以及精確控制油泵流量和活塞運(yùn)動(dòng)時(shí)間的控制。如圖 1 所示是研究壓力影響的液壓系統(tǒng)的原理圖,混凝土運(yùn)送系統(tǒng)的液壓系統(tǒng)及其控制技術(shù),主油泵 1 是一種柱塞泵,這是提供液壓力的裝置。出油控制對照來控制油泵系統(tǒng),通過這個(gè)控制油路 3 個(gè)油路,2 個(gè)換向閥 11,同一個(gè)的電磁鐵和降壓閥 12 安裝在一起。當(dāng)電磁閥 11 斷電時(shí)液壓油換向系統(tǒng)停止工作,并迫使液壓油流入油泵 1,進(jìn)入油箱。在這種情況下,液壓油的壓力控制裝備的位移為零或者非常低,油泵位移可以到最高。在另一方面,當(dāng)電磁閥打開,液壓油的壓力來自剛介紹的換向閥 11 并通過減壓閥減壓,并通過位移控制裝置,使油泵的位移減少到最小或零。兩個(gè)液壓缸 6.1 6.2 串聯(lián) 和 4 個(gè)單向閥和 4 個(gè)節(jié)氣門閥它們履行的只能是吸收壓力和緩沖。在液壓缸上安裝 2 個(gè)非接觸式傳感器 9 10 用來提供活塞移動(dòng)信號,4 個(gè)壓力傳感器安裝在測試點(diǎn) M1、 M2 、M3 、M4 ,分別提供這些傳感器收集的信號和分析同步的光譜儀和一個(gè)微型計(jì)算機(jī),采樣頻率為 1KHZ ,根據(jù)每分鐘的采樣時(shí)間,從而在壓力信號轉(zhuǎn)變的過程中獲得采信息。在實(shí)驗(yàn)過程中收集的壓力信號,只有在改變過程中,液壓缸 6.1 ,6.2 前移和縮回到缸底,分別進(jìn)行分析,當(dāng)傳感器 10 得到液壓缸 6.2 的信號移動(dòng)到行程終端,發(fā)出電子信號,調(diào)節(jié)油泵的位移,以減少油泵的泵油量,發(fā)出信號使閥門 8.7 移動(dòng),在一定時(shí)間滯后,在這個(gè)移動(dòng)過程中,閥門移動(dòng)的時(shí)間量取決于以下 2 個(gè)因素;一個(gè)是傳感器 10 的相對于液壓缸 6.2 的安裝位置;另一個(gè)是時(shí)間間隔 。即區(qū)別主油泵 1 開始調(diào)節(jié)油量的時(shí)間以及定向閥開始移動(dòng)為了簡??化實(shí)驗(yàn)傳感器 10 的安裝位置相對液壓缸 6.2 是不變的,而且油泵位移調(diào)節(jié)時(shí)間也是不變的,之間的差異時(shí)間油泵位移開始減少時(shí),開始增加 0.2 秒。3 試驗(yàn)結(jié)果和分析 圖 2 顯示壓力隨時(shí)間變化的曲線,這是衡量點(diǎn) M1 和點(diǎn) M2 在何時(shí)滯后的。是在 0.12 秒,從中可以看出在曲線圖中所示的壓力的影響程度,在范圍內(nèi),其中測試點(diǎn)供應(yīng)量 M1 位于逐漸減少與增加的工作壓力。主要原因是泵采用恒功率控制,以應(yīng)對上升的工作壓力,泵的位移減少。主油缸中的油量流速減少,因此壓力影響減少,同時(shí)還能夠從圖 2 看出有兩個(gè)高峰期的壓力曲線測試點(diǎn)M1,這 2 個(gè)時(shí)間產(chǎn)生的壓力峰值符合 2 個(gè)位置過渡控制閥 7 在其閥芯的改變。圖 3 顯示的是時(shí)間壓力的曲線,這些測量點(diǎn)時(shí),M1 和 M3 的時(shí)間間隔在 0.09 秒,工作壓力 10MPA,在圖中可以看出,第二圖中峰值曲線測量點(diǎn)的量 M1遠(yuǎn)小于第一點(diǎn),主要原因如下,當(dāng)方向控制閥發(fā)生移動(dòng)閥芯方向到達(dá)第一個(gè)過渡位置時(shí),這是不可能明顯改變液壓油流量的位置,液壓油流量依然很大,當(dāng)方向控制閥的滑閥芯過渡第 2 過渡位置時(shí),油的流量變小,因此,液壓油流動(dòng)容積的差異和產(chǎn)生的壓力的影響在第二次過渡階段是遠(yuǎn)遠(yuǎn)小于第一次過渡階段的,結(jié)果表明在這個(gè)第二高峰期的壓力遠(yuǎn)小于第一次??梢钥闯鐾ㄟ^比較圖 2和圖 3,在該時(shí)間內(nèi)產(chǎn)生壓力的影響明顯比在測試點(diǎn) M1 的時(shí)間間隔短。